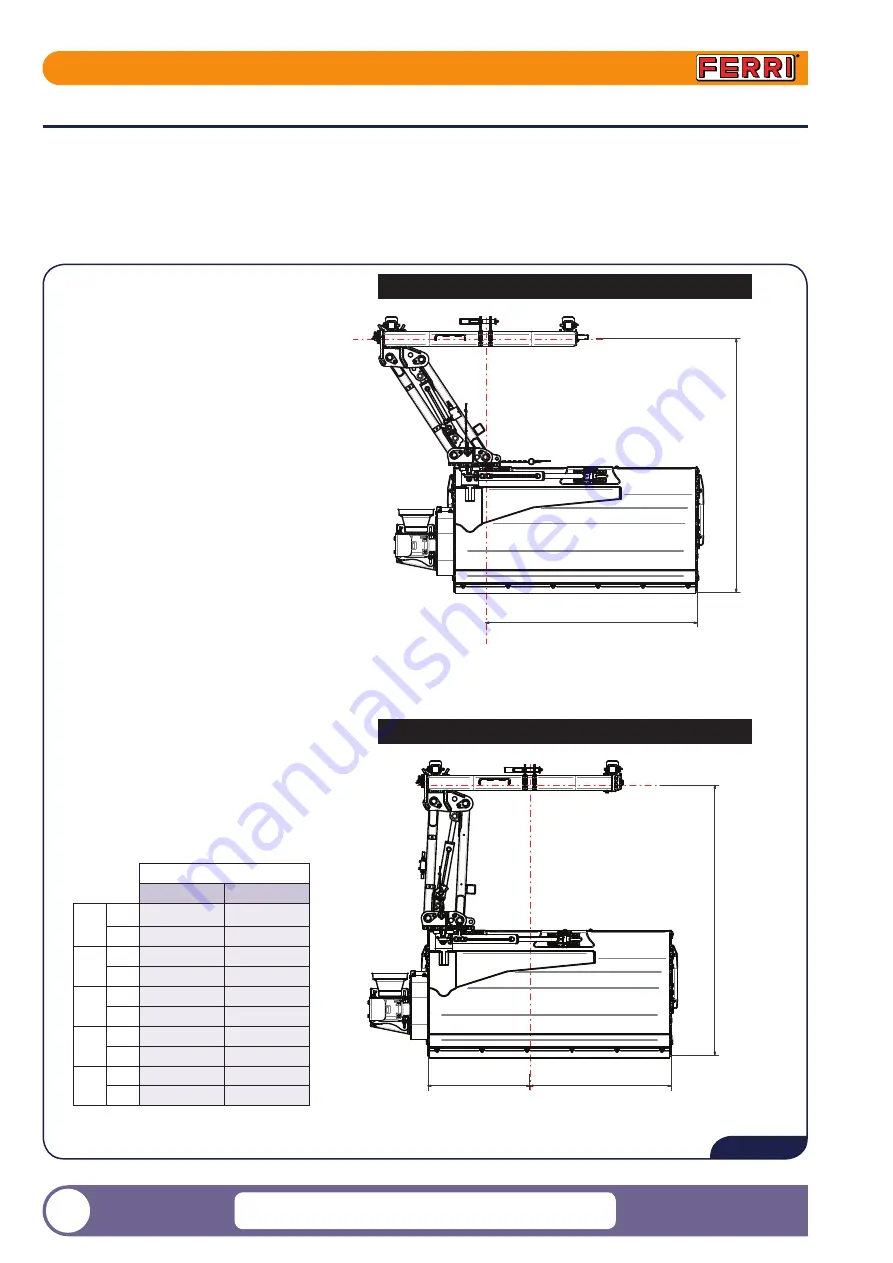
40
ZMLE
Rev. 2.0
TECHNICAL CHARACTERISTICS
3.5
03-Raggio di lavoro (ZMLE)
TAB 2
ZMLE 1400 ZMLE 1600
A
m
1,21
1,41
ft.
3' 12"
4’ 8”
B
m
1,69
1,69
ft.
5’ 7”
5’ 7”
C
m
0,68
0,68
ft.
2' 3"
2’ 3”
D
m
0,74
0,94
ft.
2' 5”
3’ 1”
E
m
1,8
1,8
ft.
5' 11"
5’ 11”
C
D
A
E
B
3.6.2 Left coupling
INTERNAL LEFT COUPLING
EXTERNAL LEFT COUPLING
Summary of Contents for ZMLE Series
Page 2: ......
Page 6: ...6 ZMLE Rev 2 0 TABLE OF CONTENTS Page left intentionally blank INDICE...
Page 81: ...81 Rev 2 0 ZMLE USE AND OPERATION 6 17 06 Posizione di trasporto ZMLE A 1 A B C E D 2 2...
Page 83: ...83 Rev 2 0 ZMLE USE AND OPERATION 6 18 06 Posizione di trasporto ZMLE A 1 2 2 B A E C A...
Page 84: ...84 ZMLE Rev 2 0 USE AND OPERATION Page left intentionally blank 06 Posizione di trasporto ZMLE...
Page 116: ...116 ZMLE Rev 2 0 WARRANTY Page left intentionally blank 11 GARANZIA...
Page 123: ...NOTES...