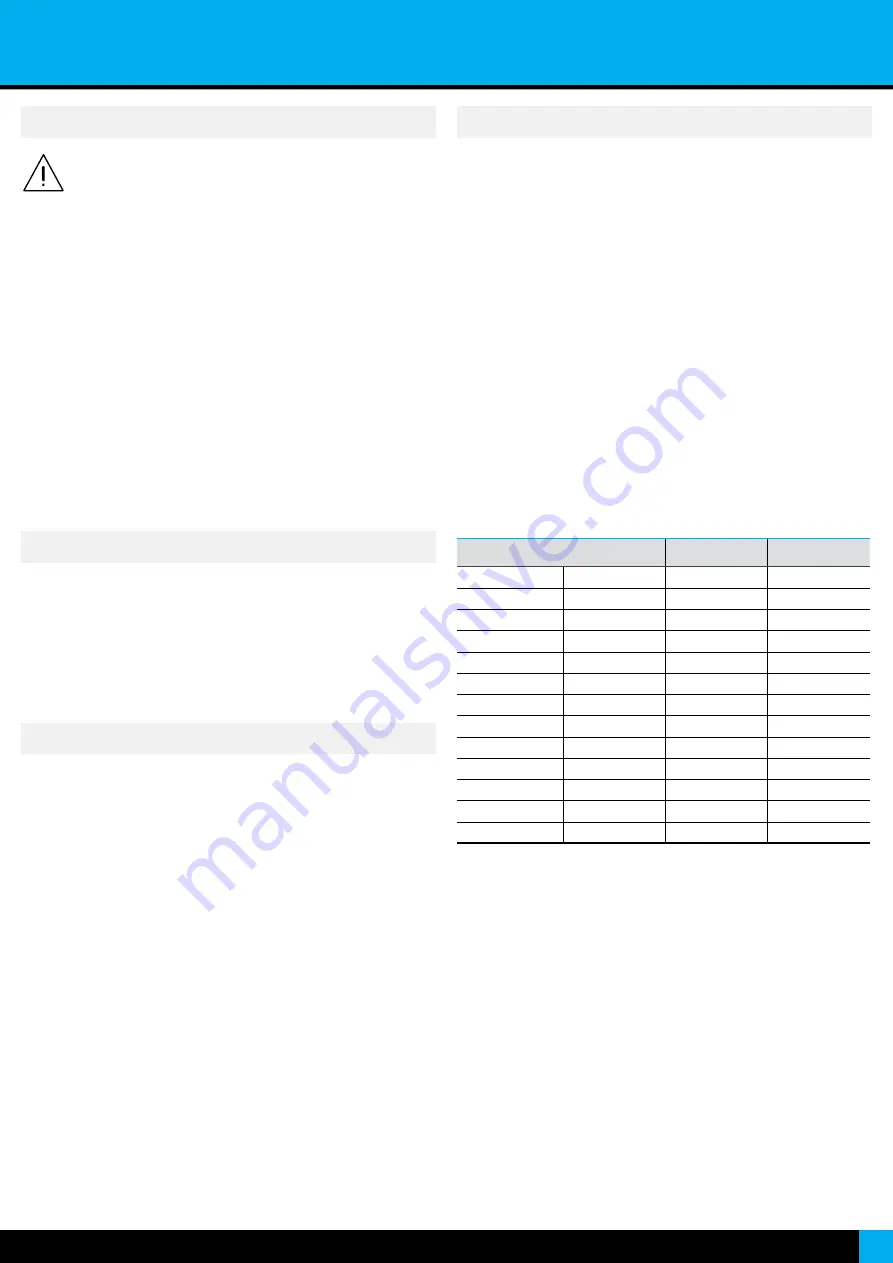
Section INDUSTRIAL . ISOLATED SIGNAL CONVERTERS
3
If this is the first time you are configuring the instrument, below
are the steps to follow during a first installation. Read all the
manual sections in order to have a full and clear view of the
characteristics of the instrument. Do not forget to read the installation
precautions at section 17.
1. Install the instrument at the DIN rail
2. Read how to operate the instrument (see section 10)
3. Connect the input, the output and the power terminals (see section 9).
4. Configure the input and output signals
• choose a predefined configuration code (see section 8)
• introduce the code at the instrument (see section 13.1)
5. If
needed, customize the input and output signal ranges (see section 13.6)
6. If needed, configure the display reading (see section 13.7), the key ‘
UP
’
(
5
) ‘
force
’ menu (see section 13.8), and the key ‘
LE
’ (
3
) ‘
messages
’ function
(see section 13.9).
7. If needed, block access to the ‘
configuration menu
4.
Installation and start-up
To measure process or temperature signals and provide a standard
process signal in 4/20 mA or 0/10 Vdc. Accepts signals from standard
thermocouples, Pt and Ntc sensors, potentiometers, resistances and
process signals. Signal acquisition, linearization and transmission to
remote acquisition devices. Isolation between circuits provided. Ranges
can be scaled to the desired range.
5. Typical applications
The instrument includes a configurable ‘
messages
’ function that provides
advanced system information on the display, available to the operator
with a single click at the front key ‘
LE
’ (
3
).
This information is helpful during start-up, installation, system
verification, routine maintenance and troubleshooting, as messages and
values provide information on the actual input and output signal value,
actual percentage of the input signal compared to the full scale and
scaled process values.
This information is available at any time, and is displayed sequentially
when requested (except while on ‘
SOS mode
’). Access to this information
reduces maintenance time, improves time invested in failure location,
and helps for an easy resolution of the problem.
Additionally, each instrument can be assigned a custom label code of up
to 8 characters (see Table 1), that can be displayed at the front display
or at the messages sequence, making system identification of each
instrument an easy task.
To configure the ‘
messages
The instrument includes a configurable ‘
SOS mode
’ function that provides
a way to manually configure a fixed output signal. This output signal
remains fixed, independent of the input signal value or sensor state.
This function allows to perform urgent maintenance or repair tasks at the
input section of the system, for example replacing temperature probes
or pressure transducers, while the instrument still provides a controlled
signal that allows the process to continue its activity, under human
surveillance. When the maintenance or repair task has been performed,
the instrument can be taken back to the standard working mode, where
the output signal is proportional to the input.
When manually activated, the ‘
SOS mode
’ generates the output signal
configured, and the front display remains flashing with the message
‘
SoS
’. All other systems are disabled, which means that :
• no error messages will be shown on display
• no key ‘
UP
’ (
5
) ‘
fast access
’ menu is accessible
• no key ‘
LE
’ (
3
) ‘
messages
’ function is accessible
• no ‘
Eco
’ mode activates
Only key ‘
SQ
’ (
<
) is accessible, to access the ‘
configuration menu
’
(eventually this access can be password locked) in order to deactivate
the ‘
SOS mode
’. Deactivation of ‘
SOS mode
’ must be performed manually
by configuring the function to ‘
oFF
’.
To configure the ‘
SOS mode
’ function, see section 13.10.
6. SOS mode
Table 1
|
Available label codes (‘Label’ parameter)
Letters
Numbers
Special
A
n
0
-
b
o
1
_
c
P
2
.
d
q
3
º
E
r
4
(blank)
F
S
5
G
t
6
h
u
7
I
V
8
J
W
9
K
X
L
Y
M
Z
7. Messages
Labeling examples (‘Label’ parameter): an application measures ambient
temperature from a Pt100, burner temperature from a thermocouple J,
and pressure from 4/20 mA pressure transducer. All signals are converted
to 4/20 mA for retransmission to PLC or SCADA. Three I4P converters are
being used, to measure Pt100, thermocouple J and 4/20 mA signals. Each
I4P can be configured the following label for easy identification :
•
Label for ambient temperature : TAmb.ºC
•
Label for burner temperature : TBur.ºC
•
Label pressure measurement: Prs.Bar