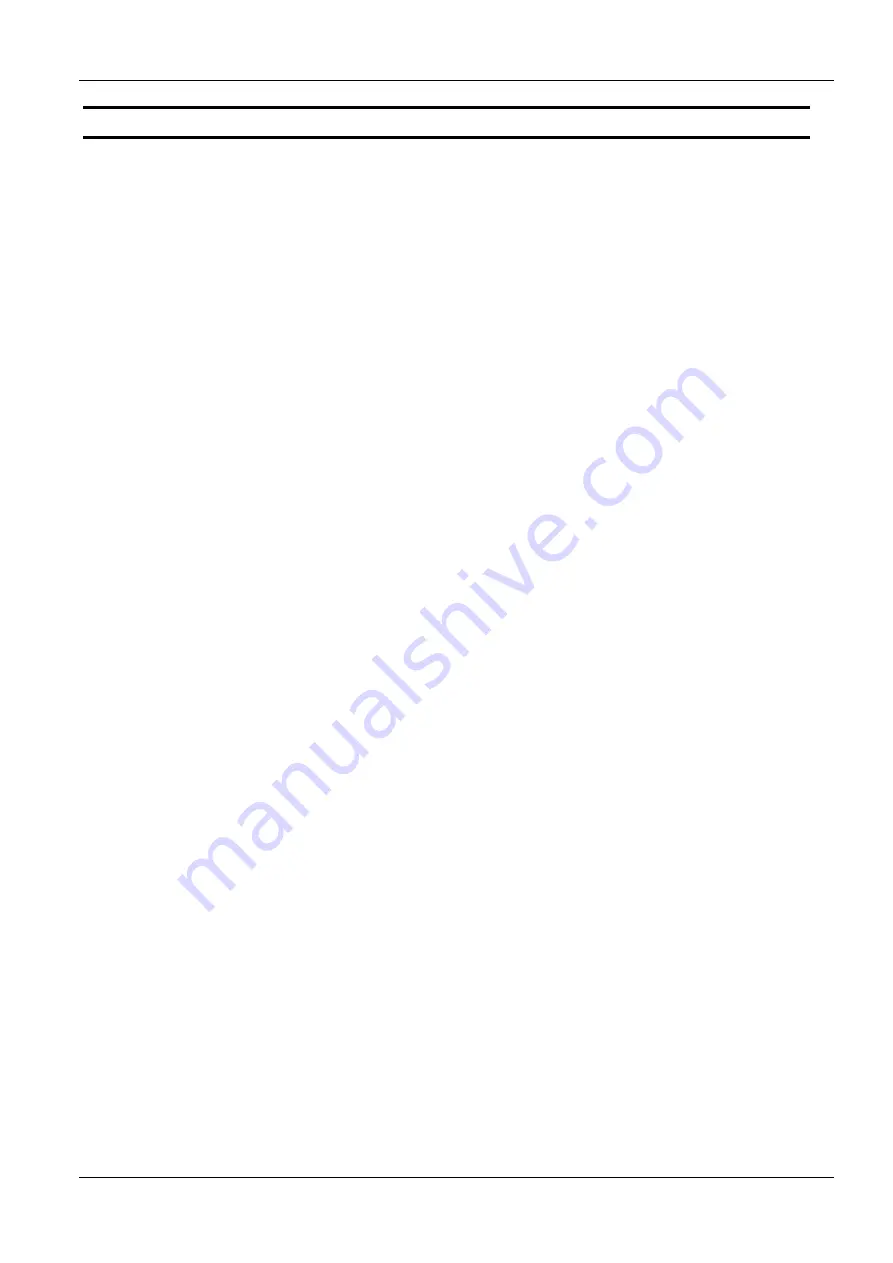
TST
Startup
WUI
FEIG ELECTRONIC GmbH
Page 4 of 20
WUI_Inbetriebnahme2_GB.doc
1 Safety
information
ATTENTION: IMPORTANT SAFETY INSTRUCTIONS
IT IS IMPORTANT FOR THE SAFETY OF PERSONS TO OBSERVE THESE INSTRUCTIONS. THESE
INSTRUCTIONS MUST BE KEPT:
-
All work concerning installation, set-up and maintenance must be carried out exclusively by qualified
staff. You must specifically pay attention to the following regulations : VDE0100, EN 50110
(VDE0105), EN 60204 (VDE0113), EN 50178 (VDE0160), EN 60335 (VDE0700), fire prevention
regulations, accident prevention regulations and the regulations relevant to industrial gates
(ZH1/494, EN12453, EN12978)
-
The control system should only be opened when the power supply is completely switched off.
-
If the potential-free contacts of the relay outputs or other contact points are operated with external
power. i.e. with a dangerous voltage which can still be live after switching off the control system or
when the mains plug is disconnected, an appropriate warning sticker must be clearly visible on the
control system casing. ("ATTENTION! all mains electricity circuits must be switched off before
accessing the connecting terminals.")
-
The control system must never be operated when it is open.
-
The control system should only be operated with dismantled CEE connector if the mains supply can
be completely disconnected from the control system by means of a corresponding switch. The mains
plug or the switch used as a substitute must be easily accessible.
-
If the connecting cable of this appliance is damaged, it must be replaced by the manufacturer or his
after-sales service or by a similarly qualified person in order to avoid dangers.
-
Even after switching off the power supply, there are still dangerous voltages for up to ½ a minute on
the DC-bus capacitors. The discharge time until the voltage values are less than 60 V DC is a
maximum of 1 minute. Touching internal control system components during this discharge time is
dangerous.
-
If the switching power supply is defective, the discharge time for the DC-bus capacitors to reach less
than 60 V DC can increase significantly. Here, discharge times of up to 2 minutes can occur.
- If the 24 V control system is short-circuited or extremely overloaded, the switching power supply
does not start although the DC-bus capacitors are charged. The display and LEDs remain dark. It is
not possible to start the power supply unit until after the short-circuit or extreme overload has been
resolved.
-
After switching off the power, the power supply unit is still supplied for several seconds by the DC-
bus capacitors and still maintains the power supply function for a certain time depending on the
power supply unit loading.
- The control system must not be operated without a connected protection earth. The absence of
protection earth results in dangerous high voltages, caused by discharge capacities, on the control
system housing. The protection earth connection must be carried out in accordance with EN50178
Section 5.2.11.1 for increased leakage currents >3,5mA.
- The system must not be switched on or operated when wet. This can result in destruction of the
control system.
-
If the control systems are used outside the specified temperature range, it must be ensured, using a
regulated and monitored heating system, that the specified operating temperature range is
maintained when the power supply is switched on and during operation of the control system.
-
It is prohibited to operate the control system if the keypad or screen is damaged.. Damaged keypads
and screens must be replaced. Touching the keypad with sharp objects must be avoided in order to
avoid damaging the keypad. The keypad is basically only intended to be touched with the fingers.
-
Before switching on the control system for the first time, it must be ensured that the plug connectors
and evaluation cards (plug-in modules) are in the correct position. Misplaced or skewed plugging-in
the cards can result in damage to the control system as can installing unauthorised third-party cards.
-
When the gate is operated in dead-man operating mode, it must be ensured that the gate area can
be viewed by the operator as safety equipment such as safety rail and light barrier are not effective
in this mode.
-
It is forbidden to operate the contactors manually. If the protective foil is destroyed, the guarantee is
void.