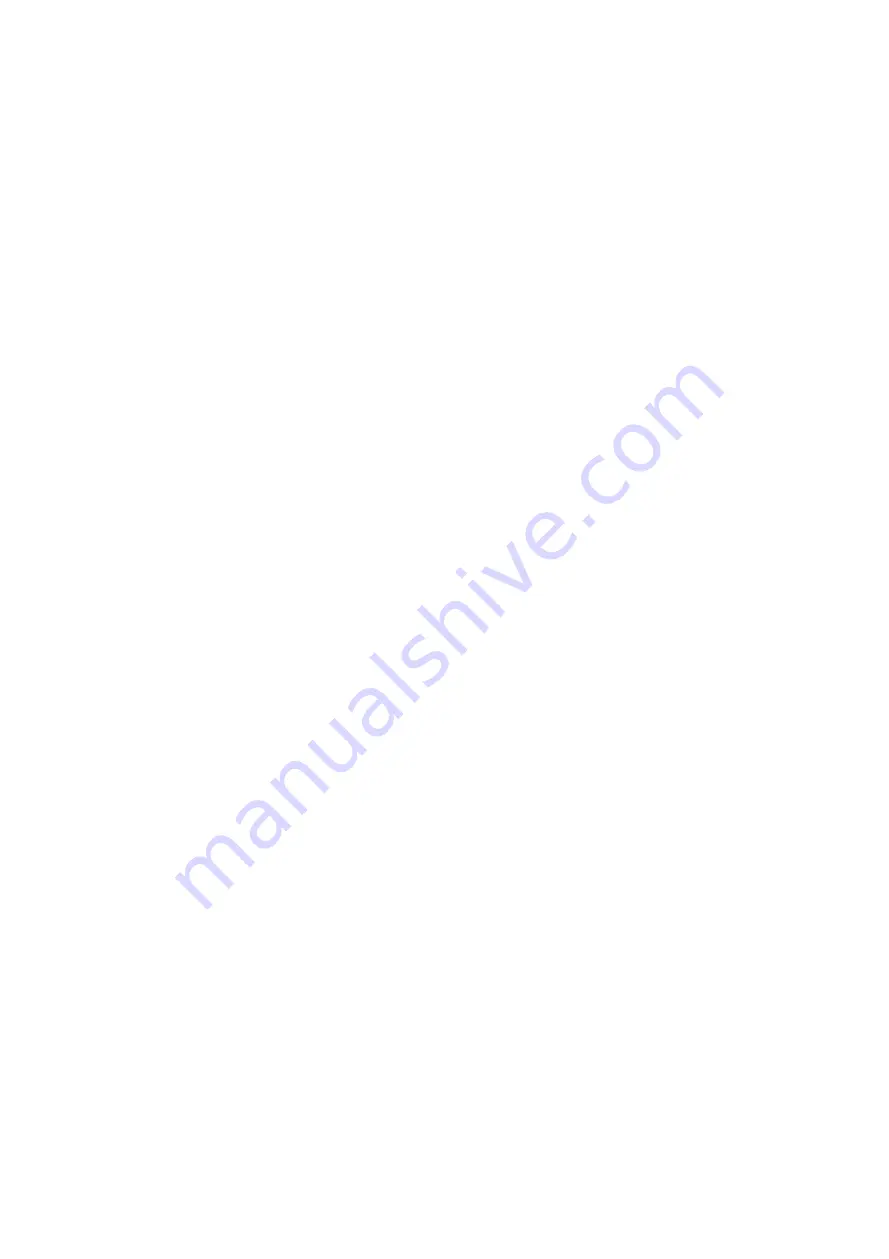
ORIGINAL INSTRUCTIONS
11
- 1. Guide bracket
- 2. Saw blade
- 3. Locking bolt
- 4. Handle
- 5. lift handle
- 6. Machine head
- 7. Clamping device
- 8. Set screw
- 9. Moving saw blade guard
- 10. Lock switch
- 11. screw
- 12. Sawdust bag
- 13. Set screw
- 14. Scale
- 15. Fixed saw table
- 16. Allen key
- 17. Rotary table
- 18. Scale
- 19. Table insert
- 20. ON/OFF switch
- 21. Latched position lever
- 22. Saw shaft lock
- 23. Opening of the dust collector
- 24. Tie rod
- 25. Set screw for drag guide
- 26. Screw for cutting depth limiting
- 27. Stop for cutting depth limiting
- 28. Screw for cutting depth limiting
- 29. Adjusting screw (45°)
- 30. Adjusting screw (45°)
- 31. Inner flange
- 32. Workpiece support
- 33. pull rod
- 34. Handle / Set screw for rotary table
- 35. Stop rail
- 36. Tilt protection
- 37. Laser(not included for this model)
- 38. screw (not included for this model)
- 39. ON/OFF switch laser(not included for this model)
Summary of Contents for FSO20254
Page 10: ...ORIGINAL INSTRUCTIONS 10 3 DESCRIPTION...
Page 12: ...ORIGINAL INSTRUCTIONS 12 4 USE...
Page 13: ...ORIGINAL INSTRUCTIONS 13...
Page 14: ...ORIGINAL INSTRUCTIONS 14...