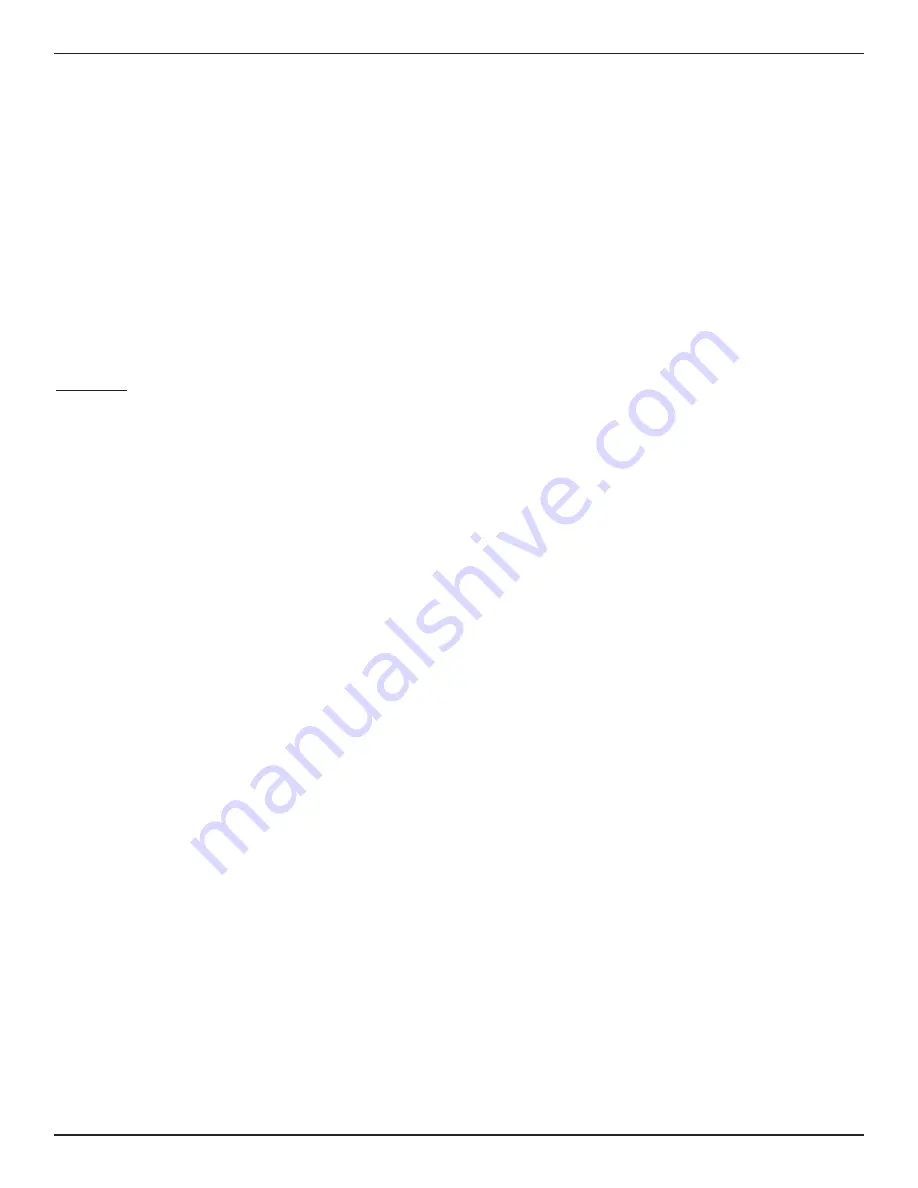
FLT
®
Series FlexSwitch
TM
MAINTENANCE
Fluid Components International LLC
37
4 MAINTENANCE
Warning:
To avoid hazards to personnel, ensure that all environmental isolation seals are properly maintained.
Caution:
The insturment contains electrostatic discharge (ESD) sensitive devices. Use standard ESD precautions when handling the
control circuit. See Section 2, Operation, for ESD details.
The FCI instrument requires very little maintenance. There are no moving parts or mechanical parts subject to wear in the instrument. The
sensor assembly which is exposed to the process media is all stainless steel construction and is only susceptible to chemical attack based on
the corrosion relationship of the RTD thermowell material with the process media.
Maintenance
Without detailed knowledge of the environmental parameters of the application surroundings and process media, FCI cannot make specific
recommendations for periodic inspection, cleaning, or testing procedures. However, some suggested general guidelines for maintenance
steps are offered below. Use operating experience to establish the frequency of each type of maintenance.
Calibration
Periodically verify the calibration of the output and re-calibrate if necessary. See Section 3 for instructions.
Cleaning
If cleaning is necessary, use a cloth dampened with plain water to avoid danger of ignition due to electrostatic charges on painted enclosure
according to EN/IEC 60079-0 clause 7.4.2 and 7.4.3.
Electrical Connections
Periodically inspect cable connections on terminal strips and terminal blocks. Verify that terminal connections are tight and in good condition
with no sign of corrosion.
Remote Enclosure
Verify that the moisture barriers and seals protecting the electronics in the local and remote enclosures are adequate and that no moisture is
entering those enclosures.
Electrical Wiring
FCI recommends occasional inspection of the system’s interconnecting cable, power wiring and sensing element wiring on a common sense basis
related to the application environment. Periodically inspect conductors for corrosion as well as the cable insulation for signs of deterioration.
Sensing Element Connections
Verify that all seals are performing properly and that there is no leakage of the process media. Check for deterioration of the gaskets and
environmental seals used.
Sensing Element Assembly
Periodically remove the sensing element for inspection based on historical evidence of debris, foreign matter, or scale buildup during ap-
propriate plant shutdown schedules and procedures. Check for corrosion, stress cracking, and/or buildup of oxides, salts, or other substances.
The thermowells must be free of excessive contaminants and be physically intact. Any debris or residue buildup could cause inaccurate
switching. Clean the sensing element with a soft brush and available solvents that are compatible with the instruments wetted metal.
Summary of Contents for FLT93B
Page 10: ...GENERAL FLT Series FlexSwitchTM 4 Fluid Components International LLC INTENTIONALLY LEFT BLANK ...
Page 103: ...FLT Series FlexSwitchTM APPENDIX E CUSTOMER SERVICE Fluid Components International LLC 97 ...
Page 104: ...APPENDIX E CUSTOMER SERVICE FLT Series FlexSwitchTM 98 Fluid Components International LLC ...