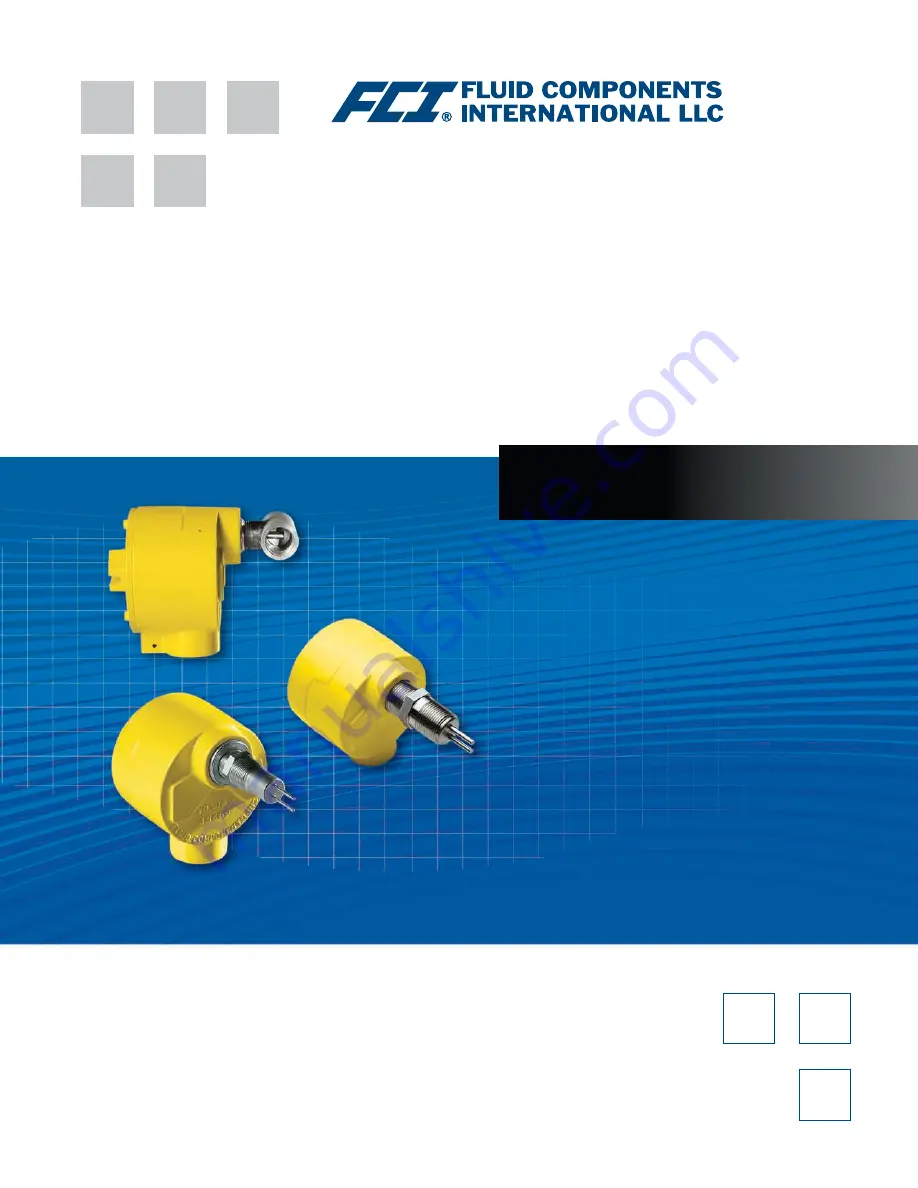
FLT
®
93 Series FlexSwitch
™
Flow, Level, Temperature Switch / Monitor
Models: FLT93B, FLT93C, FLT93F,
FLT93L, FLT93S
Installation, Operation
& Maintenance Manual
Installation, Betrieb und Wartungshandbuch
Manual de Instalación, Operación y Mantenimiento
安装、操作和维护手册
Fluid Components International LLC (FCI). All rights reserved.
Doc. No. 06EN003401
Summary of Contents for FLT93B
Page 10: ...GENERAL FLT Series FlexSwitchTM 4 Fluid Components International LLC INTENTIONALLY LEFT BLANK ...
Page 103: ...FLT Series FlexSwitchTM APPENDIX E CUSTOMER SERVICE Fluid Components International LLC 97 ...
Page 104: ...APPENDIX E CUSTOMER SERVICE FLT Series FlexSwitchTM 98 Fluid Components International LLC ...