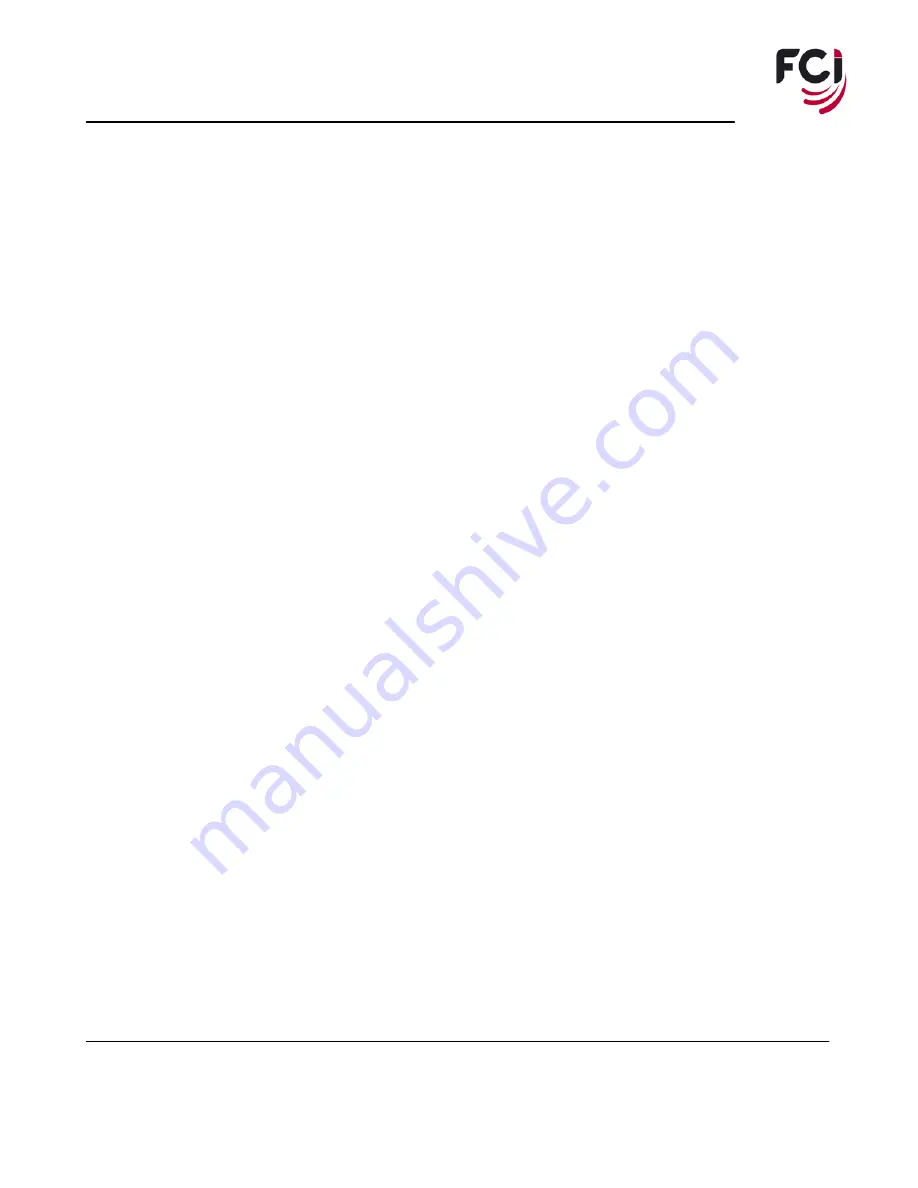
FCI USA LLC
Manual Part. No.
10118656-9090
Issued: (2011/09/12)
Page 6 of 7
Revision B
Maintenance
It is recommended that each operator of the tool be made aware of, and responsible for, the following
maintenance steps:
1.
The tool utilizes a “floating shear” to cut the terminal from the carrier strip during the crimping
process and to cut the carrier strip from the previous termination into small, manageable strips. It
is good practice to keep the scrap strips clear of the hand tool.
2.
Remove dust, moisture, and other contaminants with a clean brush, or soft, lint free cloth.
3.
Do not use any abrasive materials that could damage the tool.
4.
If an instance should occur of a crimped terminal remaining in the upper crimp tooling, do not use
any sharp instruments to remove the terminal as this might scratch the tooling.
5.
Make certain all pivot points, pins and bearing surfaces are protected with a thin coat of high
quality machine oil. Do not oil excessively.
6.
When tool is not in use, store in a clean, dry area.
Jams
Should this tool ever become stuck or jammed in a partially closed position:
Do not attempt to pull the
handles open or “clamp” the handles closed as damage to the ratchet mechanism may result.
•
Depending on the situation, the tool may either be cleared by removing the upper tooling bolt or,
using a bypass to release the ratchet pawl.
Notes
1.
This tool should only be used for the terminals and wire gauges specified within this manual.
2.
This tool is not adjustable.
a.
Variations in tools, terminals, and wire stranding and insulation types may affect crimp
height.
3.
The tool may not give a good insulation wrap (crimp) for all insulation sizes. This tool is intended
for standard conductor sizes.
4.
FCI does not repair hand tools (see warranty). If the crimp tooling is damaged or worn,
replacement tooling must be purchased.
5.
FCI does not certify crimp hand tools.
6.
Check for damaged parts. Before further use of the tool, determine that it would operate properly
and perform its intended function – check for alignment of moving parts, binding of moving parts,
breakage of parts, mounting, and any other conditions that may affect the operation.