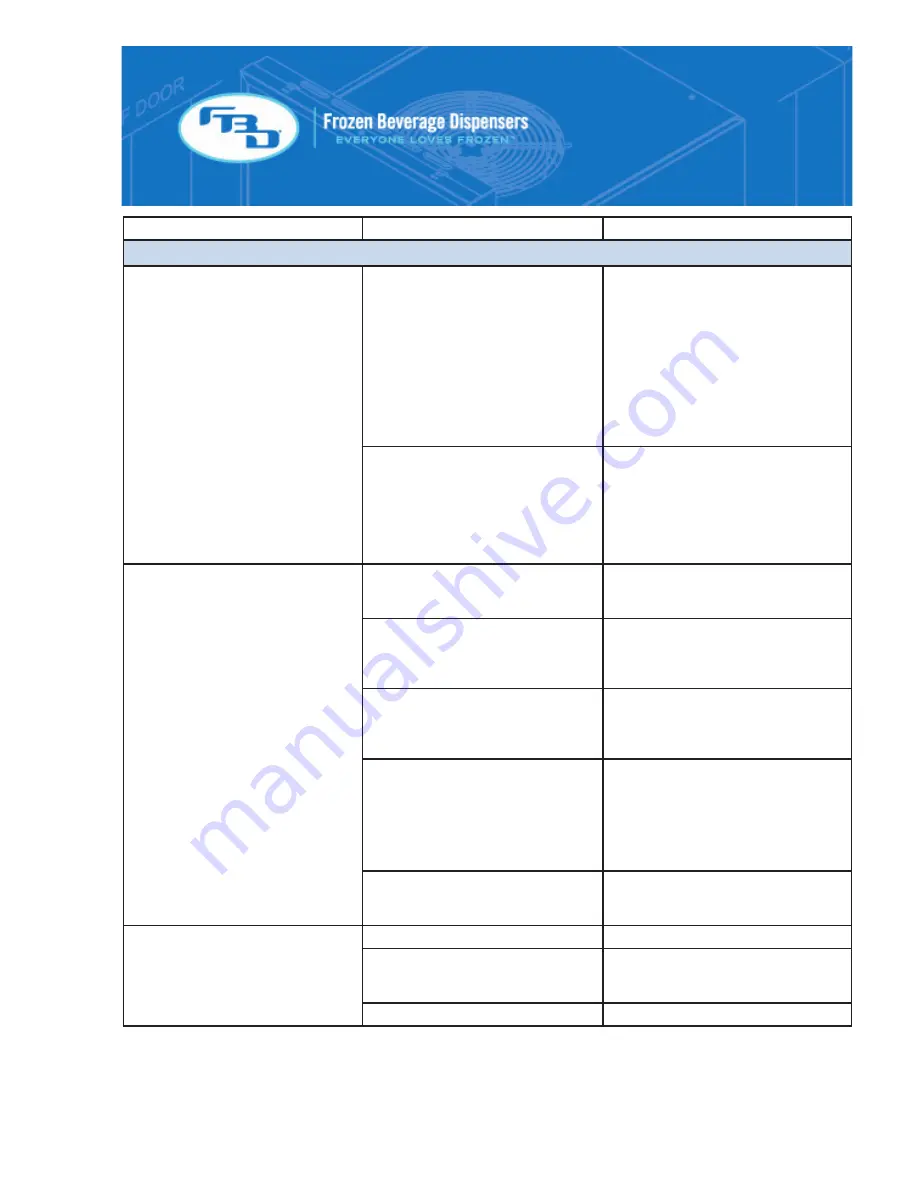
28
TROUBLE
CAUSE
REMEDY
Out of product displayed (Out of
Water, Syrup or CO
2
).
(continued from previous page)
Excessive pressure drops in
syrup lines.
Observe "Syrup Press" readouts
as barrel fills to verify. Increase
line diameter or relocate syrup
source closer to unit. Syrup
pressures may only be raised (by
increasing pump CO
2
pressure) if
separate regulators are installed
for dispenser and syrup pumps.
Never exceed pump manufactur-
er's recommended maximum CO
2
inlet pressure.
Transducer problem (H
2
O or
syrup).
Check pressure readouts (H
2
O
and syrup) for proper settings. If
CO
2
is not within 70-72 psig (483-
496 kPag), adjust regulator and/
or check transducer. H
2
O will be
about 15 psig (103 kPag) higher.
Replace transducer if necessary.
Product does not flow freely or
does not flow at all from dispens-
ing valve.
Faulty CO
2
check valve.
Check tank pressure. If low,
inspect CO
2
check valve. Clean or
replace if necessary.
Solution solenoid valve won't
open.
Energize solution solenoid and
check for 24VAC at coil (see
Section 10.6
). Clean or replace
solenoid if necessary.
Ice particles in dispensing valve.
Run defrost cycle. If necessary,
open and close dispensing valve
several times or run warm water
over valve.
Product in cylinder is frozen too
hard or solid.
1. Check water/syrup flow rates
and brix. Adjust if necessary
(see
Section 6.4
).
2. Defrost barrel. Assure barrel is
filled to 90% of capacity, then
press RUN.
CO
2
shutoff is closed.
Open CO
2
shutoff and adjust sec-
ondary CO2 regulators inside of
dispenser to to 60 psig (414 kPag).
Product leaking from rear of cold
pack.
Rear seal worn or damaged.
Replace with new seal.
Seal is not positioned correctly.
From inside barrel reseat seal and
make sure it is flush with back of
barrel.
Beater drive coupling is worn.
Replace coupling.