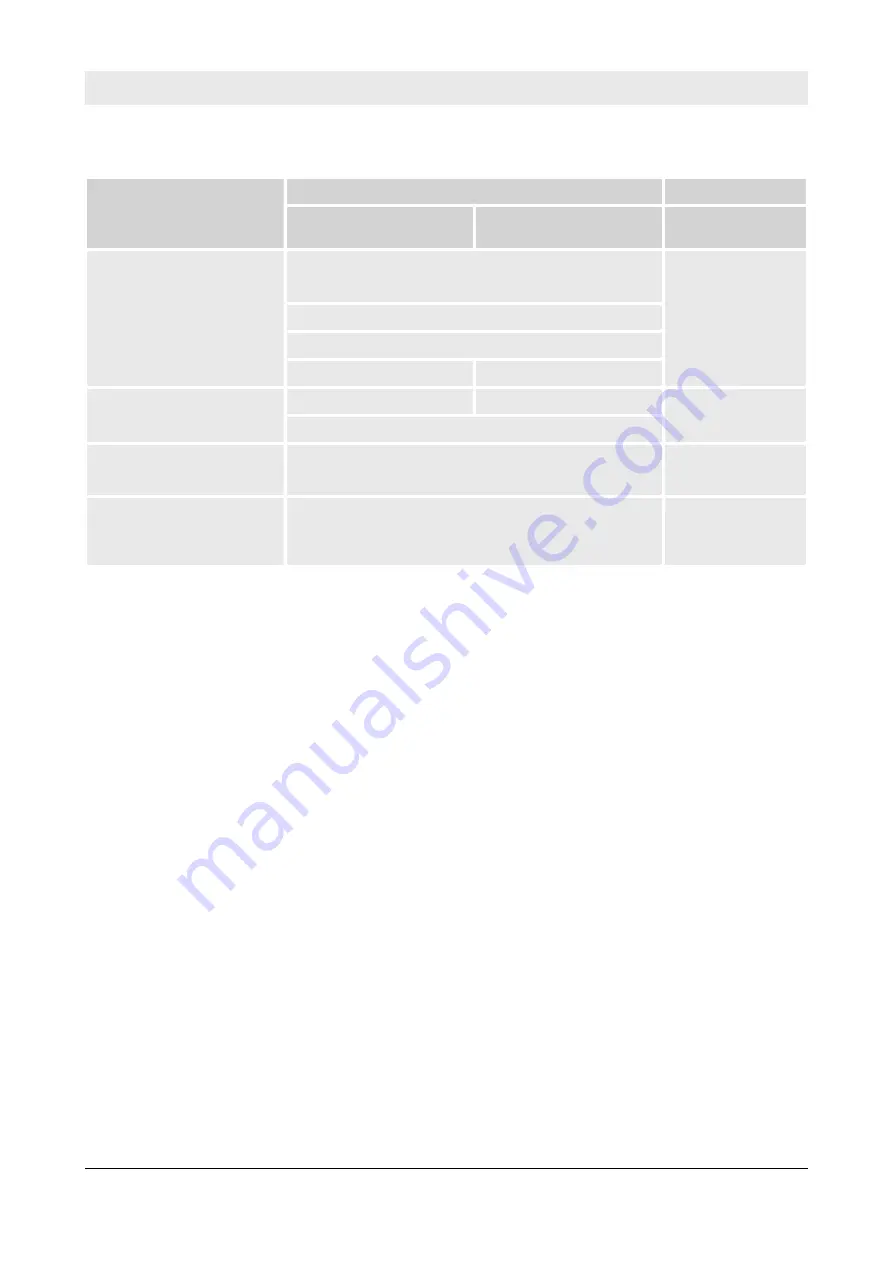
8.4 List of fuels and lubricants
Assembly group
Fuel or lubricant
Filling quantity
Summer
Winter
Observe the level
mark!
Engine oil
SAE 10W-40
Specification:
Chapter 8.3.1 ‘Engine oil’ on page 64
0.9 l
(0.24 gal us)
SAE 15W-40
SAE 10W-30
SAE 30
SAE 10W
Fuel
Diesel
Winter diesel fuel
3.0 l
(0.8 gal us)
Specification:
Chapter 8.3.2 ‘Fuel’ on page 64
Exciter shaft housing
as engine oil
0.4 l
(0.11 gal us)
Steering rod
Hydraulic oil (ISO), HV 32
Chapter 8.3.4 ‘Mineral oil based
0.4 l
(0.11 gal us)
Maintenance – List of fuels and lubricants
DRP20D
67
Summary of Contents for DYNAPAC DRP20D
Page 6: ...Table of contents DRP20D 6...
Page 7: ...1 Introduction Introduction DRP20D 7...
Page 11: ...2 Technical data Technical data DRP20D 11...
Page 15: ...3 Concerning your safety Concerning your safety DRP20D 15...
Page 38: ...Concerning your safety Safety components DRP20D 38...
Page 39: ...4 Indicators and control elements Indicators and control elements DRP20D 39...
Page 41: ...5 Checks prior to start up Checks prior to start up DRP20D 41...
Page 47: ...6 Operation Operation DRP20D 47...
Page 54: ...Operation Parking the machine in secured condition DRP20D 54...
Page 55: ...7 Loading transporting the machine Loading transporting the machine DRP20D 55...
Page 61: ...8 Maintenance Maintenance DRP20D 61...
Page 93: ...9 Troubleshooting Troubleshooting DRP20D 93...
Page 98: ...Troubleshooting Malfunctions during operation DRP20D 98...
Page 99: ...10 Disposal Disposal DRP20D 99...
Page 101: ......
Page 102: ......