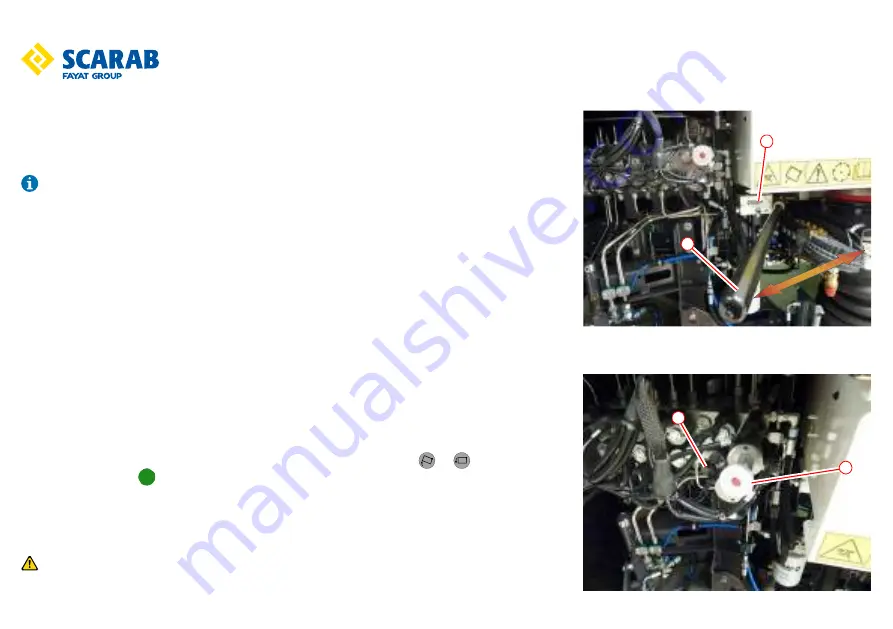
Manual No. SCAZ043075 1.7.01
35
E&OE
M25H Road Sweeper
Operating Instructions
Using the auxiliary hand pump
In the event of hydraulic system failure, an auxiliary manually operated hydraulic pump is fitted, to
enable the hopper to be operated. This is located on the left hand side of the vehicle, adjacent to the
hydraulic and water valves. The pump handle is stowed in the cab in a locker under seat.
It should be noted that it will require a substantial number of pumping cycles to complete the
following operations. The assistance of a second person is preferable.
Follow the procedure below:
1. Switch the engine and ignition off. Apply the handbrake.
2. Open left hand gantry door to access the main valve block.
3. Insert the pump handle
q
, into the pump
w
.
4. To raise hopper, press in and turn to latch the control on top of raise and lower solenoid
e
.
To lower hopper, pull out and turn to latch the control on top of raise and lower solenoid
e
.
5. Push in and hold unloader valve
r
.
6. Operate the pump handle to raise or lower the hopper manually.
7. When hopper is in position required, release unloader valve
r
and unlatch control
e
.
8. Stow handle when finished with.
Alternate procedure, this will require two people to perform:
1. Apply the handbrake. Switch the ignition on but do not start engine.
2. Insert the pump handle
q
, into the pump
w
.
3. One person is required to press and hold the raise or lower buttons or and the safety
interlock button on the remote control.
4. Second person then operates the pump handle to raise or lower the hopper manually.
5. When hopper is in position required, release the buttons on the remote control.
6. Stow pump handle when finished with.
Never work under a raised hopper unless an appropriate prop is used.
4
3
2
1
Summary of Contents for SCARAB M25H
Page 69: ...Manual No SCAZ043075 1 7 01 69 E OE M25H Road Sweeper Operating Instructions Operator Notes ...
Page 70: ...Manual No SCAZ043075 1 7 01 70 E OE M25H Road Sweeper Operating Instructions Operator Notes ...
Page 71: ...Manual No SCAZ043075 1 7 01 71 E OE M25H Road Sweeper Operating Instructions Operator Notes ...
Page 72: ...Manual No SCAZ043075 1 7 01 72 E OE M25H Road Sweeper Operating Instructions Operator Notes ...
Page 73: ...Manual No SCAZ043075 1 7 01 73 E OE M25H Road Sweeper Operating Instructions Operator Notes ...