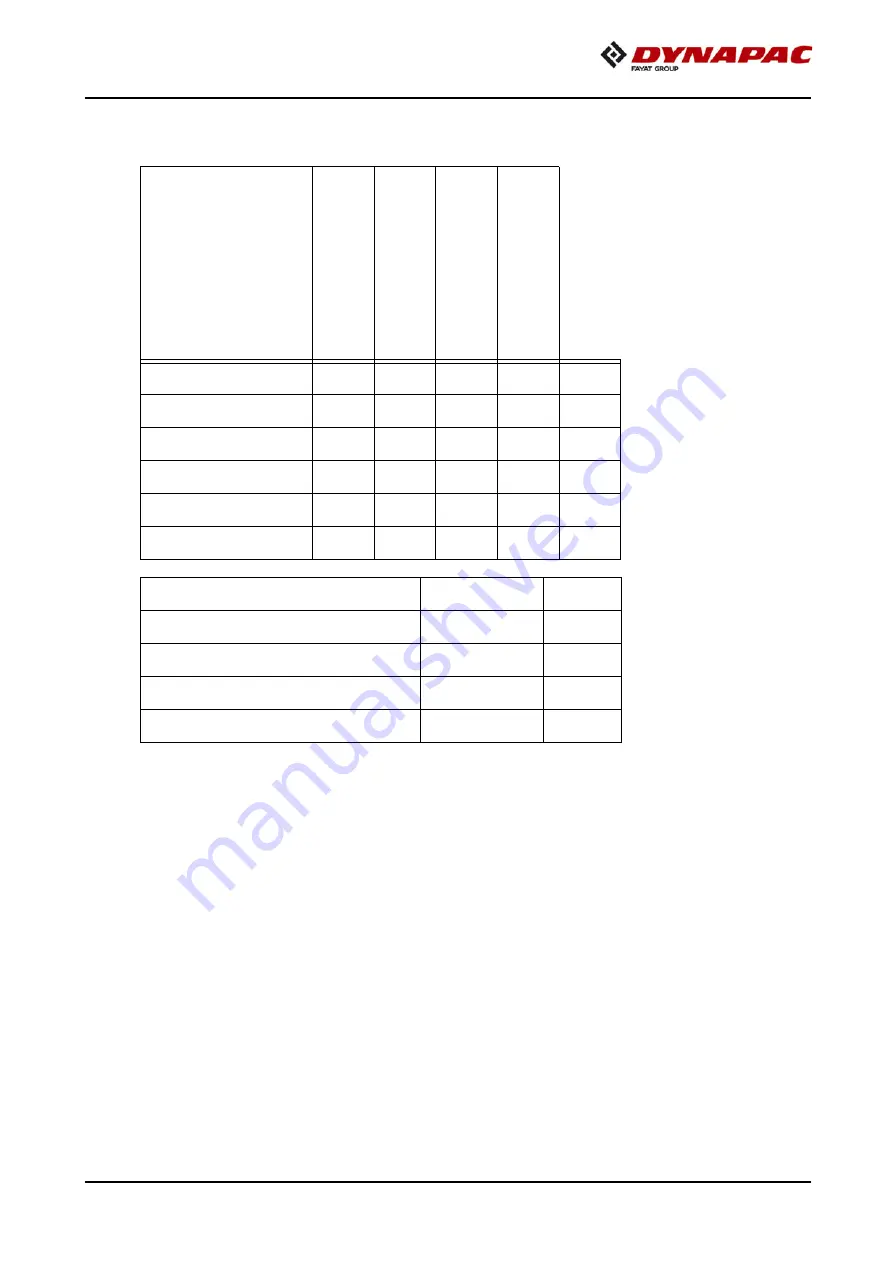
B 15
5.8
Performance data SD2500WS
Screed used
Basic width
(without cut-of
f shoes)
Minimum paving width
(with cut-of
f shoe)
Fully variable hydr
.
a
d
justment up to
Maximum paving width
(with
extension parts)
V5100TV(E)
2.55
2.00
5.10
8.80
m
V5100TV
2.55
2.00
5.10
8.80
m
V5100TH
2.55
2.00
5.10
6.60
m
V6000TV(E)
3.00
2.45
6.00
9.00
m
V6000TV
3.00
2.45
6.00
9.00
m
V6000TVH
3.00
2.45
6.00
7.50
m
Transport speed
0 - 20
km/h
Operating speed
0 - 30
m/min
Paving height
-100 - 300
mm
Max. grain size
40
mm
Theoretical paving performance
750
t/h
Summary of Contents for DYNAPAC SC2500WS
Page 1: ...Operating Instructions Paver Finisher SD2500W SC2500WS Type 897 898 11 0419 4812074033...
Page 2: ...www dynapac com...
Page 14: ...12...
Page 28: ...A 2...
Page 37: ...B 9 4 Safety devices 4 5 6 7 10 7 9 3 2 5 11 7 13 1 12 8 14...
Page 51: ...B 23 71 70 40 41 42 xxxxxxxxxxxxxxxxx 9 73 12 12 13 9...
Page 94: ...C 13 28...
Page 98: ...D 13 4 10 13 16 15 17 11 12 9 8 7...
Page 100: ...D 13 6 10 13 16 15 17 11 12 9 8 7...
Page 102: ...D 13 8 10 13 16 15 17 11 12 9 8 7...
Page 104: ...D 13 10 18 19 20 21...
Page 106: ...D 13 12 22 23 24 25...
Page 108: ...D 13 14 26 27 28...
Page 110: ...D 13 16 29...
Page 112: ...D 13 18 33 32...
Page 114: ...D 13 20 35 34 36 37...
Page 116: ...D 13 22 38 40 41 39 42...
Page 118: ...D 13 24 38 40 41 39 42...
Page 120: ...D 13 26 38 40 41 39 42...
Page 122: ...D 13 28 44 43 45 46...
Page 124: ...D 13 30 48 52 50 47 51 49...
Page 126: ...D 13 32 48 52 50 47 51 49...
Page 128: ...D 13 34 48 52 50 47 51 49...
Page 130: ...D 13 36 54 58 56 53 57 55...
Page 132: ...D 13 38 54 58 56 53 57 55...
Page 134: ...D 13 40 54 58 56 53 57 55...
Page 136: ...D 13 42 60 59...
Page 138: ...D 13 44 64 61 62 66 65 63...
Page 140: ...D 13 46 64 61 62 66 65 63...
Page 142: ...D 13 48 68 67...
Page 144: ...D 13 50 70 69...
Page 146: ...D 13 52 72 71...
Page 148: ...D 13 54 74 73...
Page 150: ...D 13 56 76 75...
Page 152: ...D 13 58 78 77...
Page 154: ...D 13 60 3 Remote control...
Page 156: ...D 13 62 121 120 121...
Page 158: ...D 13 64 122 124 125 123 125 122 124...
Page 160: ...D 13 66 122 124 125 123 125 122 124...
Page 162: ...D 13 68 126 128 129 127 129 126 128...
Page 164: ...D 13 70 126 128 129 127 129 126 128...
Page 166: ...D 13 72 131 132 133 130...
Page 168: ...D 13 74 135 136 137 134...
Page 170: ...D 13 76 139 138...
Page 172: ...D 13 78 141 140 141...
Page 174: ...D 13 80 142 143...
Page 176: ...D 13 82 145 144 146 147 148...
Page 178: ...150 149 D 13 84...
Page 180: ...D 13 86...
Page 181: ...D 22 1 D 22 Operating the display...
Page 185: ...D 22 5 1 1 Menu operation procedure for adjusting parameters A B C...
Page 211: ...D 22 31 Service menu Password protected menu for various service settings...
Page 241: ...D 22 61 Example C...
Page 243: ...D 22 63 2 3 Error codes A Scan QR Code to access failure code chart...
Page 249: ...D 31 5 Control platform moveable o 6 2 5 7 4 8 3 9 10...
Page 253: ...D 31 9 Protective roof o A D B C B A C D 1 3 4 5 2...
Page 284: ...D 31 40 Illuminated balloon o 5 4 3 2 11 13 9 8 6 1 7 10 12...
Page 290: ...D 31 46...
Page 295: ...D 43 5 13 11 12 10 15 120...
Page 297: ...D 43 7 13 11 12 10 15 120...
Page 300: ...D 43 10 13 68...
Page 302: ...D 43 12 A B C...
Page 304: ...D 43 14 D 68 50 56 55 49...
Page 306: ...D 43 16 35 34 15 13 16 69 63 61 64 46 45 68 75 126 130...
Page 308: ...D 43 18 A 33 15 13 16 10...
Page 312: ...D 43 22 A B 59 67 37 36 54 48 53 47...
Page 314: ...D 43 24 15 13 73 70 54 48 53 47 71 72 123 127 126 130 126 130...
Page 318: ...D 43 28 13 15 74 73 70 69...
Page 321: ...D 43 31...
Page 322: ...D 43 32 13 15 74 73 70 69...
Page 324: ...D 43 34 13 15 11 12...
Page 326: ...D 43 36 13 11 15 69 75 12...
Page 346: ...E 13 14 Symbol Meaning Outer auger bearing Auger end bearing...
Page 363: ...E 13 31 Symbol Meaning RL Extension pipe left RR Extension pipe right RL RR...
Page 404: ...F 29 4...
Page 405: ...F 33 1 F 33 Maintenance conveyor 1 Maintenance conveyor...
Page 412: ...F 33 8...
Page 413: ...F 40 1 F 40 Maintenance auger assembly 1 Maintenance auger assembly...
Page 425: ...F 41 1 F 41 Maintenance auger assembly 1 Maintenance auger assembly external drive version...
Page 482: ...F 55 34...
Page 519: ...F 61 1 F 61 Maintenance hydraulic system 1 Maintenance hydraulic system...
Page 536: ...F 61 18...
Page 537: ...F 72 1 F 72 Maintenance travel drive steering 1 Maintenance travel drive steering...
Page 548: ...F 72 12...
Page 549: ...F 83 1 F 83 Maintenance electrical system 1 Maintenance electrical system...
Page 559: ...F 83 11 Relays in the engine compartment K Function 0 Engine start...
Page 570: ...F 90 8...
Page 571: ...F 100 1 F 100 Tests stopping 1 Tests checks cleaning stopping...
Page 585: ...F 115 3 2 1 6 5 7 4 3 6 8 9...
Page 592: ...F 115 10...
Page 593: ......
Page 594: ...www dynapac com...