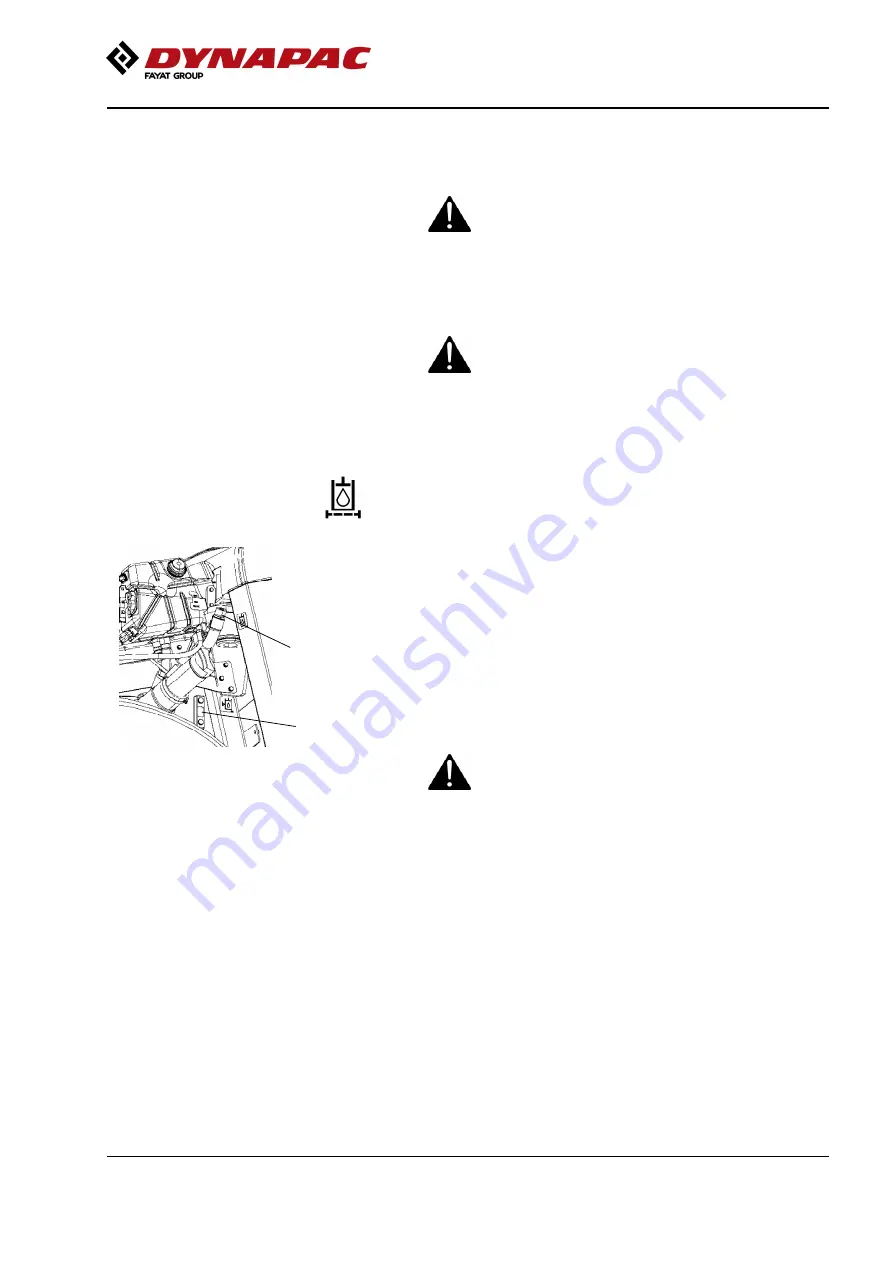
Maintenance - 1000h
4812158701_G.pdf
2019-10-01
Maintenance - 1000h
Performed after 1000 operating hours (each year)
Park the roller on a level surface.
The engine must be switched off and the
parking brake activated when checking or
adjusting the roller, unless otherwise specified.
Park the roller on a level surface.
The engine must be switched off and the
parking brake activated when checking or
adjusting the roller, unless otherwise specified.
Ensure that there is good ventilation (air
extraction) if the engine is run indoors. Risk of
carbon monoxide poisoning.
Ensure that there is good ventilation (air
extraction) if the engine is run indoors. Risk of
carbon monoxide poisoning.
Hydraulic filter - Replacement
Fig. Hydraulic reservoir
2. Filler cap/Bleeding filter
3. Sight glass
2
3
Undo the filler cap/bleeder filter (2) on top of the
reservoir so that over-pressure inside the reservoir can
be eliminated.
Make sure that the bleeding filter (2) is not clogged, air
must have unobstructed passage through the cap in
both directions.
If passage in either direction is blocked, clean the filter
with a little diesel oil and blow through with
compressed air until the block is removed, or replace
the cap with a new one.
Wear protective goggles when working with
compressed air.
Wear protective goggles when working with
compressed air.
131
Summary of Contents for DYNAPAC CA5000
Page 2: ......
Page 12: ...e 4812158701_G pdf 2019 10 01...
Page 16: ...Introduction 4812158701_G pdf 2019 10 01 4...
Page 22: ...Safety Optional 4812158701_G pdf 2019 10 01 10...
Page 26: ...Special instructions 4812158701_G pdf 2019 10 01 14...
Page 70: ...Machine description 4812158701_G pdf 2019 10 01 58...
Page 104: ...Operating instructions Summary 4812158701_G pdf 2019 10 01 92...
Page 106: ...Preventive maintenance 4812158701_G pdf 2019 10 01 94...
Page 116: ...Maintenance 4812158701_G pdf 2019 10 01 Service Checklist 104...
Page 122: ...Maintenance 10h 4812158701_G pdf 2019 10 01 110...
Page 128: ...Maintenance 50h 4812158701_G pdf 2019 10 01 116...
Page 169: ......
Page 170: ...Dynapac Compaction Equipment AB Box 504 SE 371 23 Karlskrona Sweden www dynapac com...