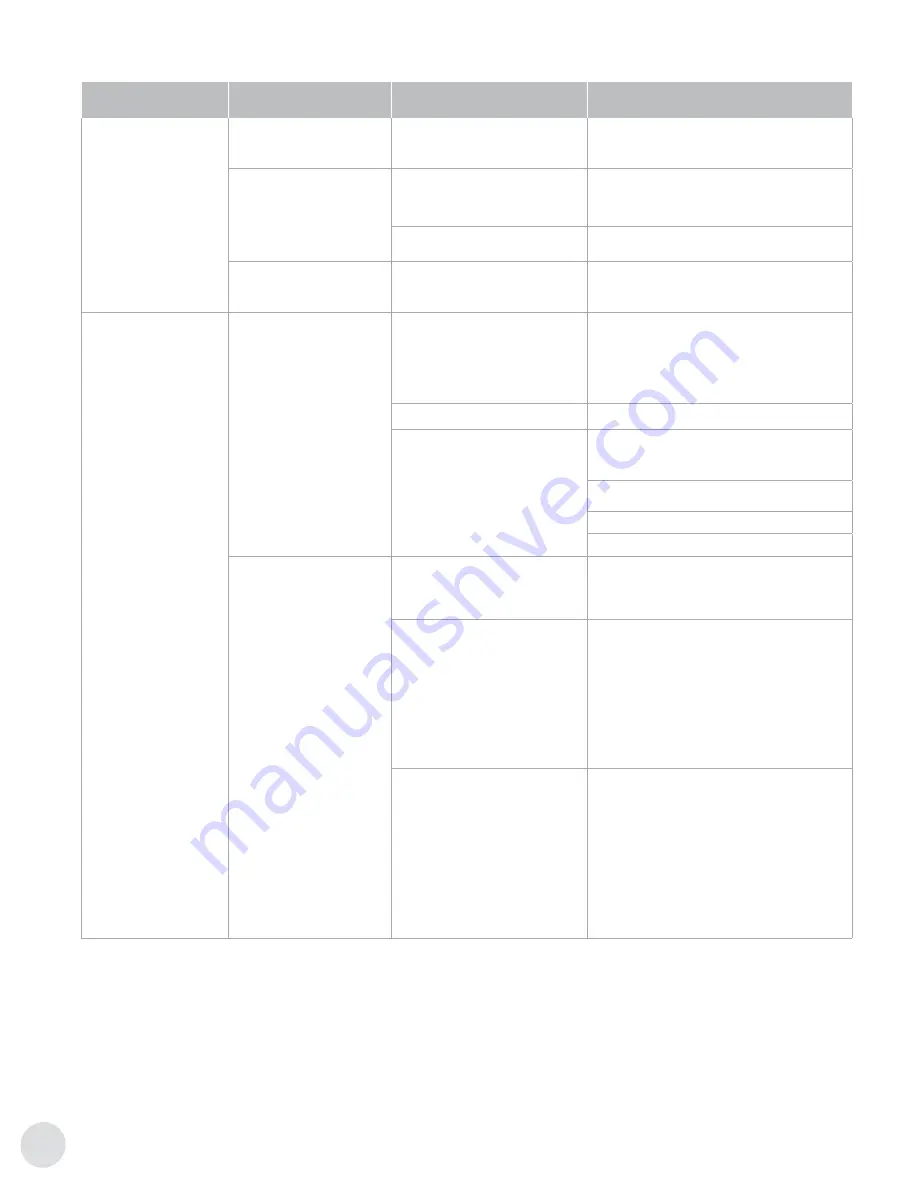
22
22
Tr
ou
bl
es
ho
ot
ing
Problem
Conditions*
Possible Cause
Remedy**
Heater operating
but does not deliver
adequate heat.
No alarm.
Manifold pressure at
maximum for propane.
Heater connected to natural gas.
The as delivered heater is set for LPG operation.
Increase manifold pressure to within natural gas
limits.
Manifold pressure at
maximum for appropriate
fuel.
Corrosion, dirt or other debris
restricts burner orifii.
•
Service burner.
•
Drill out each orifice with #47 drill (0.0785"
diameter)
Duct system restricted.
Inspect tie duct or cross ducts
for mud.
Gas manifold and supply
pressure slowly drop while
operating.
Vapour withdrawal causes
refrigeration effect that lowers
LPG tank pressure.
Remove snow accumulation on propane tanks.
Heater fails to start.
Alarm indicated.
•
Fan does not start.
•
Controller LEDs
– POWER on.
– ALARM red.
– AIR SW alternating.
Motor thermal overload
relay open.
1. 240V single-phase models:
Reset
overload located on motor junction box.
2. Three-phase models: Reset thermal
overload relay located on control panel
below contactor.
Motor breaker open.
Close breaker.
•
Air switch closed when
expected open.
•
Air switch jumped.
•
Air switch frozen.
•
Air switch out of calibration.
Inspect air switch.
Remove jumper.
Clear any ice or debris from air switch ports.
Calibrate air switch.
•
Fan does not start.
•
Controller LEDs
– POWER on.
– ALARM red.
– AIR SW alternating.
•
High limit exceeded.
Cycling thermostat loose inside
sensor duct and high limit
thermostat limit reached.
Fasten thermostats in place.
Cycling thermostat leads shorted
and high limit thermostat limit
reached.
1. Remove any test jumper shorting
thermostat leads.
2. Verify leads are not shorted together
between sensor box and control panel.
3. Inspect wire insulation for damage and
verify no shorts to ground.
4. Verify manifold pressure is within
nameplate limits.
High limit thermostat leads
shorted.
1. Remove any test jumper shorting
thermostat leads.
2. Verify leads are not shorted together
between sensor box and control panel.
3. Inspect wire insulation for damage and
verify no shorts to ground.
4. Verify interior of sensor box is dry.
5. Seal or replace any damaged or missing
gasket. Close lid.
Summary of Contents for Hellfire 900
Page 26: ...26 26 Figure 3 155 Clearance Figure 2 140 Clearance Installation...
Page 27: ...27 27 Figure 4 155 Clearance Turned 90 Degrees Installation...
Page 37: ...37 37 Heater Specifications THERMON HEATING SYSTEMS INC H 9 SchematicsMaintenance...
Page 38: ...38 38 Heater Specifications THERMON HEATING SYSTEMS INC...
Page 39: ...39 39 Heater Specifications THERMON HEATING SYSTEMS INC...
Page 40: ...40 40 Heater Specifications THERMON HEATING SYSTEMS INC...
Page 41: ...41 41 Heater Specifications THERMON HEATING SYSTEMS INC...
Page 42: ...42 42 Heater Specifications THERMON HEATING SYSTEMS INC...
Page 54: ...54 54 NOTES...
Page 55: ...55 55 NOTES...