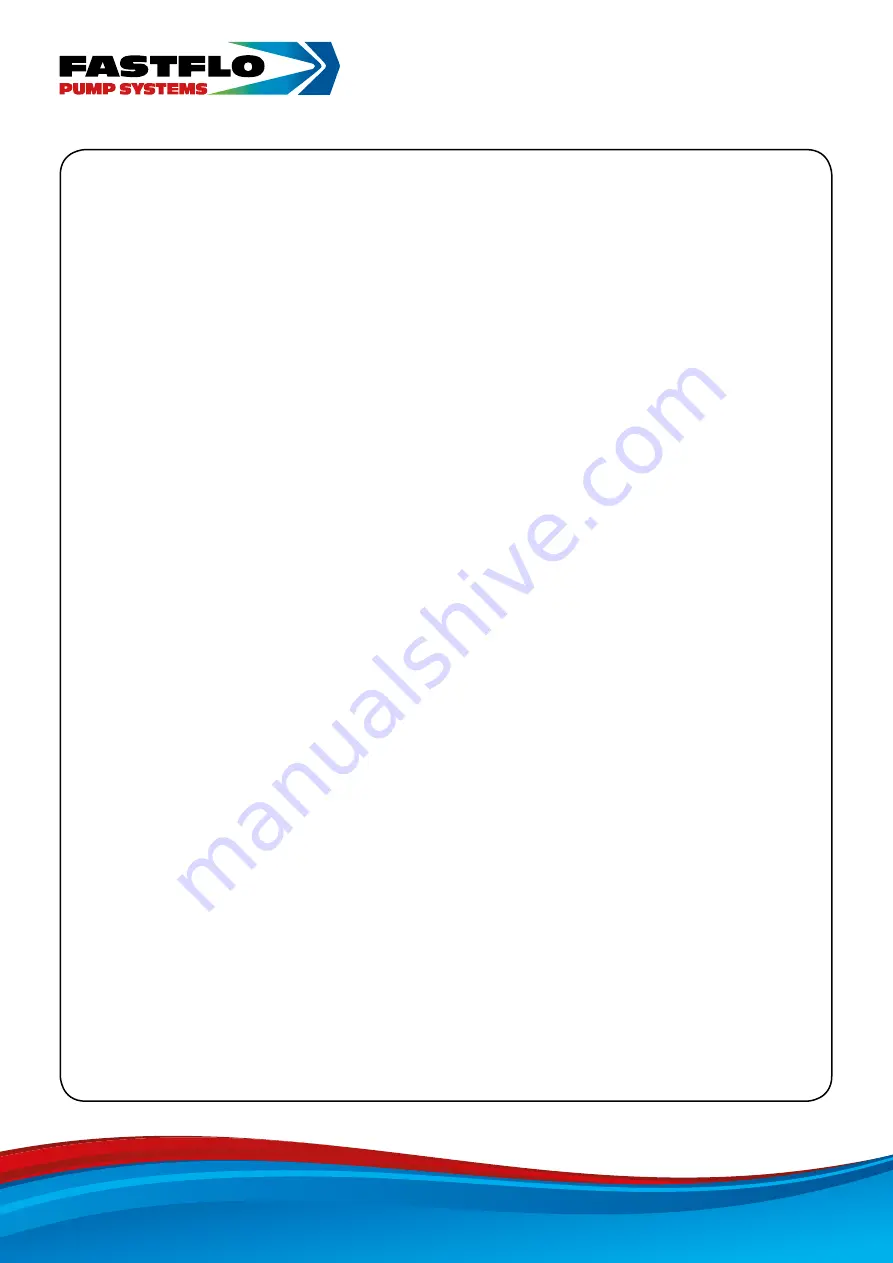
®
Providing Pumping Solutions
www.fastflo.co.nz |
Call Free: 0800 327 835
7
6. Install 90º ramp/inspection bend (large inspection type) or 90º M&F inspection junction (supplied by others)
on inside of tank, so as to direct liquid flow downwards into the pump chamber. This also allows access for
plugging and water testing gravity drain.
Sewer drain is now ready to be laid from pump station inspection bend or junction back up to dwelling/
building.
7. Install vent from top of tank if required. Refer to separate page on Vent Requirements.
8. Cut discharge hole in tank wall with a hole saw, in desired position/direction (normally 75mm above top
rib). Insert the small rubber discharge uniseal into discharge hole on inside of tank, and lubricate with o’ring
lubricant or similar.
Hole sizes are as follows:-
For 50mm PVC pressure pipe
= 76mm hole saw size
For 80mm PVC pressure pipe
= 102mm hole saw size
For 100mm PVC pressure pipe
= 127mm hole saw size
9. Screw vertical discharge pipe into pump outlet (if not already installed).
Note: If overall discharge height out of tank is lower than standard height, then shorten vertical discharge
pipe to suit.
Glue swept discharge bend (with valves attached) onto vertical pipe before installing pump(s), making sure
bend is facing over top of pump(s).
Note: The non-return ball valve(s) “Y” leg must always be facing upwards, as per the prefabricated
position. This must not be altered to any other position, as this will cause operational failure.
10. Install pump(s) in tank, as close to centre as possible. Pump(s) should sit on flat base of tank, so that when
valves are installed later, they are easily accessible when lid is open. Allow enough room for gravity drain
inlet bend/junction if directly opposite pump discharge position.
11. Install short PVC discharge pipe with coupling nut from inside tank. Push through the rubber uniseal
the required distance, so as to match up to pump pipework, and tighten quick connect coupling. Extend
discharge pipework beyond pump station to discharge point, in pipe material selected.
12. Hang rope(s) or chain(s) on hook(s) at top corner of tank. If hooks not mounted, position in corners adjacent
to pumps. KEEP CHAIN(S) WELL AWAY FROM PUMP FLOATS – ON OPPOSITE SIDE OF PUMP FLOATS, TO
AVOID MALFUNCTION.
13. Electrician to install 32mm/50mm PVC electrical conduit(s) and wiring between pump station and control
box/panel (mounted on building adjacent to pump station). Refer to electrical installation diagram and
instructions. Refer to Electrical Wiring Instructions for testing pump(s) and alarms.
14. Feed pump and alarm float cables through conduit(s) to control box/panel.
Summary of Contents for MINI Series
Page 2: ......
Page 23: ...Providing Pumping Solutions www fastflo co nz Call Free 0800 327 835 23...
Page 24: ...Providing Pumping Solutions www fastflo co nz Call Free 0800 327 835 24...
Page 25: ...Providing Pumping Solutions www fastflo co nz Call Free 0800 327 835 25...
Page 26: ...Providing Pumping Solutions www fastflo co nz Call Free 0800 327 835 26...
Page 27: ......
Page 28: ...Providing Pumping Solutions...