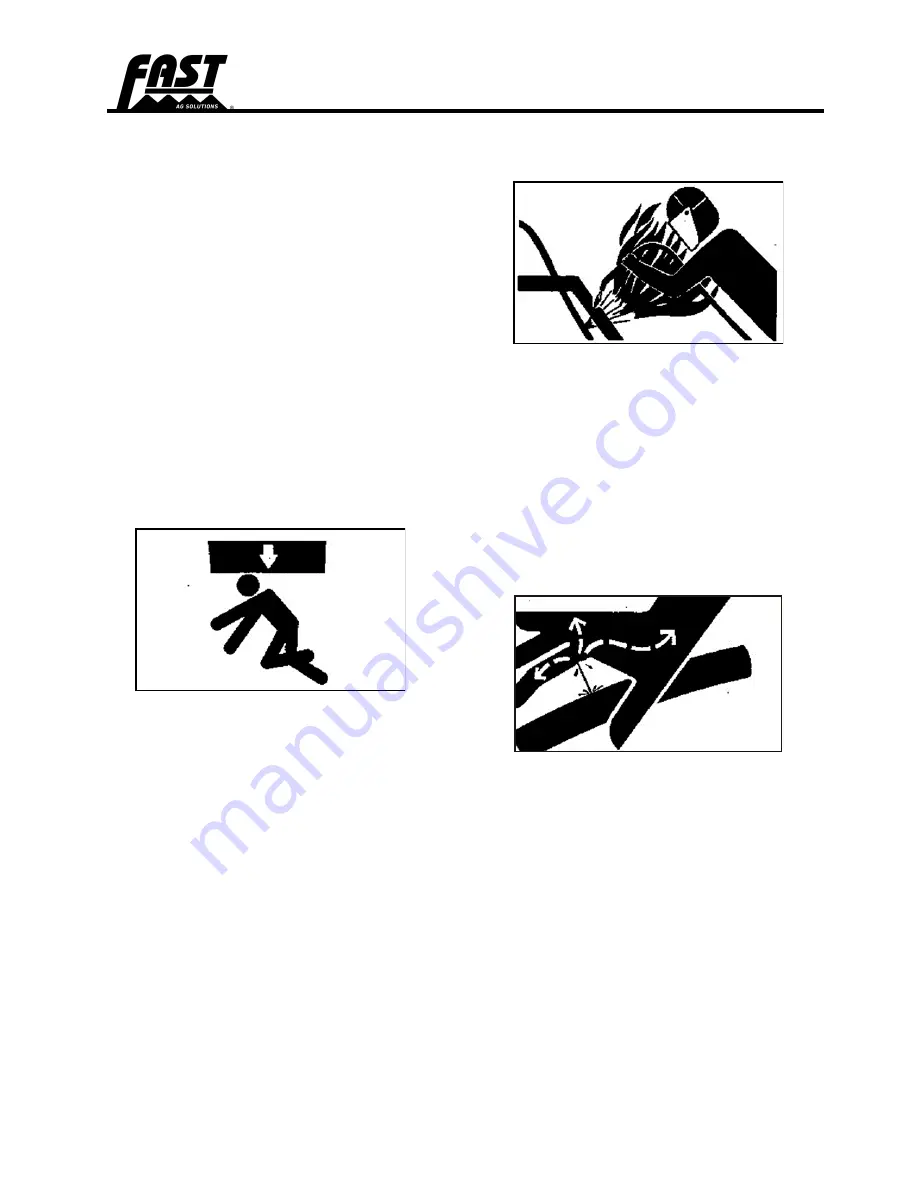
SAFETY
SAFETY
3PT Sprayer 9553P / 9573P
Page 23
machine elements that must be raised for
service work.
Keep all parts in good condition and properly
installed. Fix any damage immediately.
Replace worn or broken parts. Remove any
buildup of grease, oil, or debris.
On self-propelled equipment, disconnect the
battery ground cable (-) before making any
adjustments on electrical systems or welding
on the machine.
On towed implements, disconnect wiring
harnesses from tractor before servicing
electrical system components or welding on
the machine.
Support Raised Equipment
Always use a safety support when working
on, under, or around the machine. Transport/
Service locks can be used for this purpose.
Shut off the tractor’s engine and remove the
key when working on the machine.
If air has been allowed to enter hydraulic
hoses or cylinders, bleed the hydraulic
system before use. If there is a failure in the
hydraulic system, unsupported or raised
equipment could suddenly lower, causing
serious personal injury or death.
If support is not available, completely lower
wings and frame, relieve hydraulic pressure
and disconnect hoses from tractor.
Avoid Heating Near Pressurized Fluid
Lines
Flammable spray can be generated by
heating near pressurized fluid lines, resulting
in severe burns to yourself and bystanders.
Do not heat by welding, soldering, or using a
torch near pressurized fluid lines or other
flammable materials. Pressurized lines can
accidentally burst when heat goes beyond
the immediate flame area.
Avoid High-Pressure Fluids
Inspect hydraulic hoses periodically – at
least once per year – for leakage, kinking,
cuts, cracks, abrasion, blisters, corrosion,
exposed wire braid, or any other signs of
wear or damage.
Replace worn or damaged hose assemblies
immediately with Fast Ag Solutions approved
replacement parts.
Escaping fluid under pressure can penetrate
the skin causing serious injury.
Avoid the hazard by relieving pressure
before disconnecting hydraulic or other lines.
Tighten all connections before applying
pressure.
Summary of Contents for 9553P
Page 1: ...9553P 9573P 60 100 3PT SPRAYER OWNER S MANUAL...
Page 2: ...820103 9553P 9573P 60 100 3PT Sprayer 2023 11 30...
Page 33: ...SAFETY SAFETY 3PT Sprayer 9553P 9573P Page 33...
Page 34: ...SAFETY SAFETY 3PT Sprayer 9553P 9573P Page 34 Main Frame...
Page 35: ...SAFETY SAFETY 3PT Sprayer 9553P 9573P Page 35...
Page 36: ...SAFETY SAFETY 3PT Sprayer 9553P 9573P Page 36 Tanks and Platform...