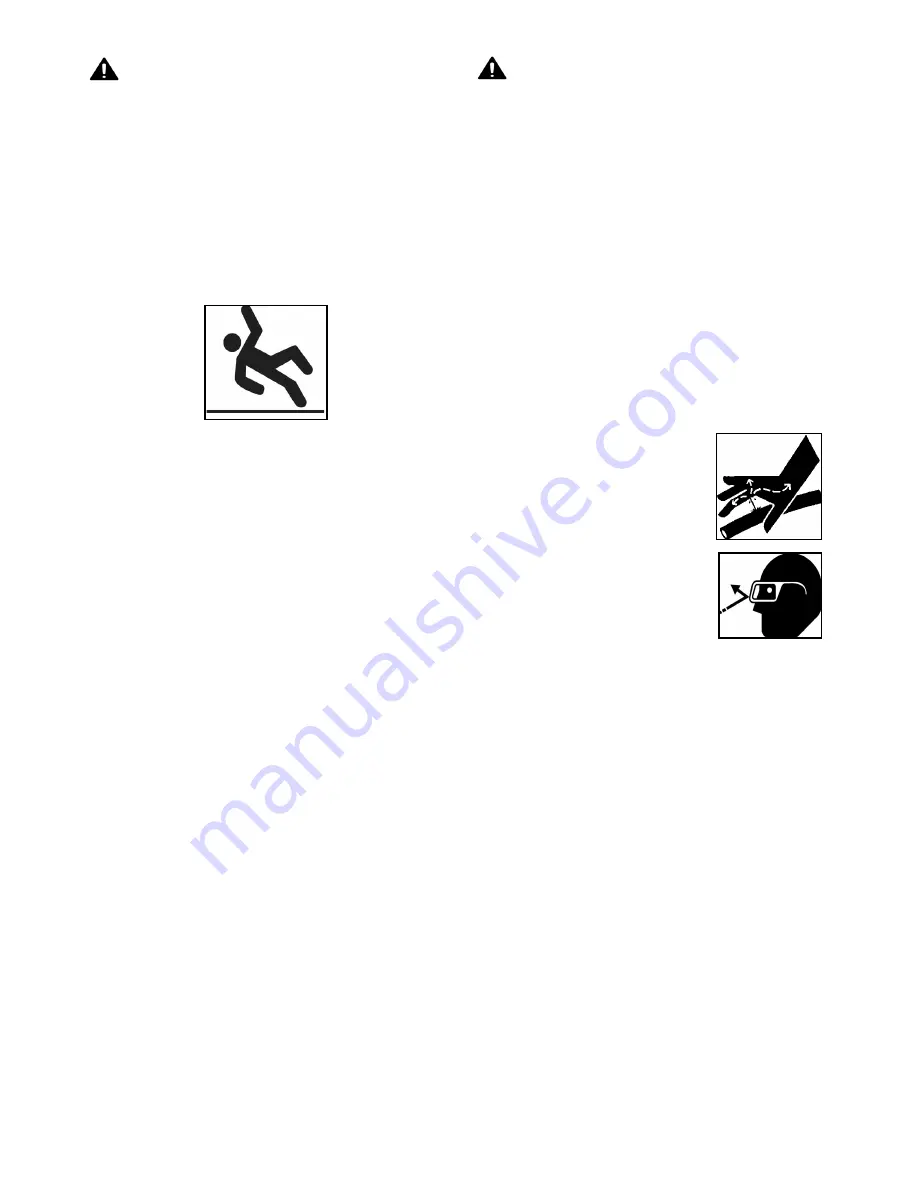
8300 Liquid Fertilizer Applicator 10 FAST AG Solutions
2.4 Maintenance Safety
1. Review Operator’s Manual and all safety items
before working with, maintaining or operating
applicator.
2. Lower machine to ground, place all controls in
neutral, stop engine, set park brake, remove igni-
tion key, and wait for all moving parts to stop
before servicing, adjusting, repairing or unplug-
ging.
3. Follow good shop practices:
4. Keep service area clean and dry.
5. Be sure electrical outlets and tools are properly
grounded.
6. Use adequate light for job at hand.
7. Before applying pressure to a hydraulic system,
make sure all components are tight, hoses and
couplings are in good condition.
8. Relieve pressure from hydraulic circuit before ser-
vicing or disconnecting from tractor.
9. Keep hands, feet, clothing and hair away from all
moving and/or rotating parts.
10. Clear area of bystanders, especially children,
when carrying out any maintenance and repairs or
making any adjustments or filling.
11. Place stands or blocks under frame before work-
ing beneath machine or when changing tires.
12. Be sure all guards are in place and secured when
maintenance work is completed.
13. Use only tools, jacks and hoists of sufficient
capacity for the job.
2.5 Hydraulic Safety
1. Always place all tractor hydraulic controls in neu-
tral before dismounting.
2. Make sure that all components in hydraulic sys-
tem are kept in good condition and are clean.
3. Replace any worn, cut, abraded, flattened or
crimped hoses.
4. Do not attempt any makeshift repairs to hydraulic
lines, fittings or hoses by using tape, clamps or
cements.
5. The hydraulic system operates under extremely
high-pressure. Such repairs will fail suddenly and
create a hazardous and unsafe condition.
6. Pressurized fluids can pene-
trate the skin. Hydraulic
hoses can fail from age, dam-
age and exposure.
7. Do not search for hydraulic
leaks without body and face
protection. A tiny, almost
invisible leak can penetrate
the skin, thereby requiring
immediate medical attention.
Use wood or cardboard to
detect hydraulic leaks, never
use your hands.
8. If injured by a concentrated
high-pressure stream of hydraulic fluid, seek med-
ical attention immediately. Serious infection or
toxic reaction can develop from hydraulic fluid
piercing skin surface.
9. Before applying pressure to system, verify all
components are tight, hoses and couplings are in
good condition.
Summary of Contents for 8300
Page 2: ...990 8300 Liquid Fertilizer Applicator 4 16 2019...
Page 16: ...8300 Liquid Fertilizer Applicator 15 FAST AG Solutions DECAL A DECAL B DECAL C DECAL D DECAL E...
Page 17: ...8300 Liquid Fertilizer Applicator 16 FAST AG Solutions DECAL F DECAL G DECAL H DECAL I...
Page 39: ...8300 Liquid Fertilizer Applicator 38 FAST AG Solutions...
Page 40: ...8300 Liquid Fertilizer Applicator 39 FAST AG Solutions...
Page 41: ...8300 Liquid Fertilizer Applicator 40 FAST AG Solutions NOTES...