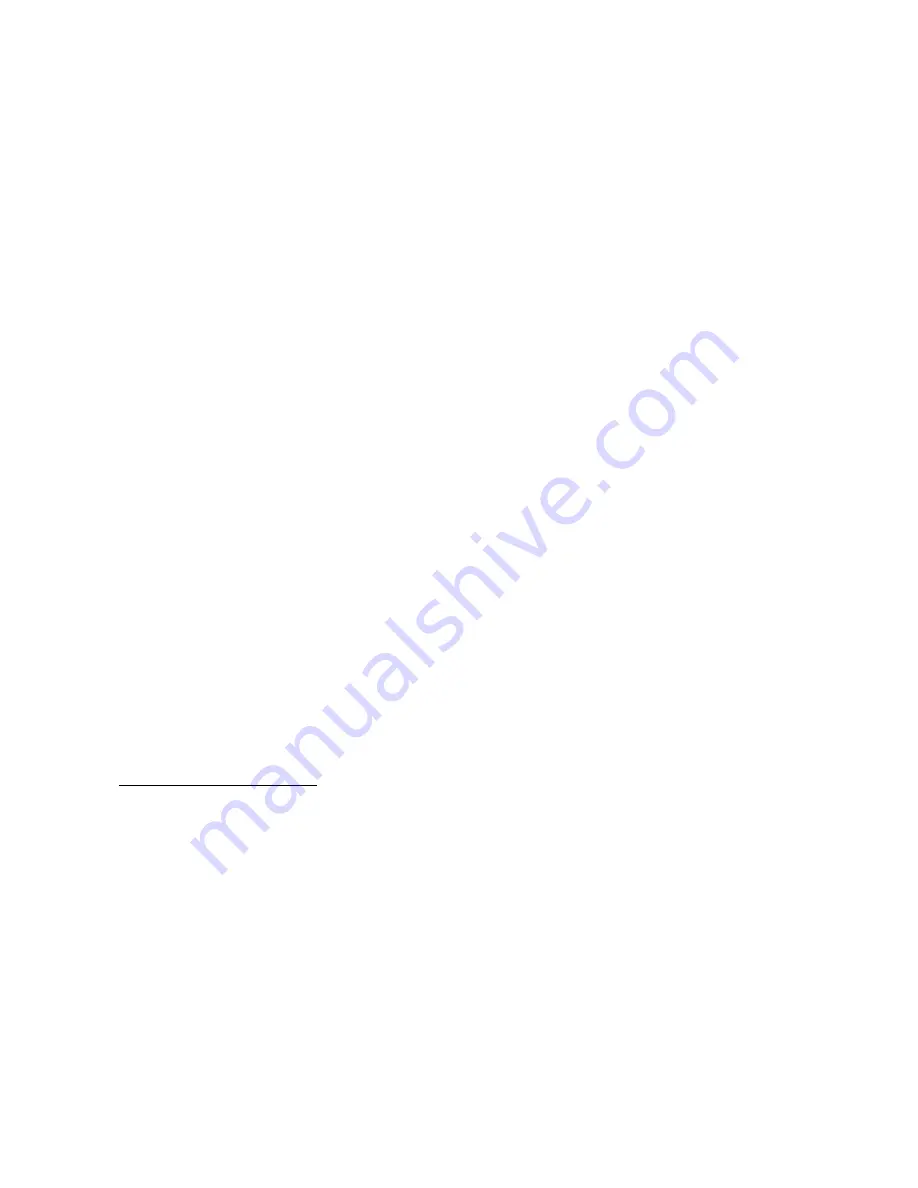
40
To remove water and impurities from the preliminary and primary fuel filters 1, 2 (Fig. 5.3.3) :
loosen the drain plugs 10 (Fig. 5.3.3) at the bottom of the filters and allow the water/fuel to drain into a
suitable container.
Every 600 hours of operation change the felt element of the preliminary fuel filter. 2 (Fig. 5.3.3).
Every 900 hours of operation change the felt element of secondary fuel filter 1 (Fig. 5.3.3).
In order to replace a filter element unscrew bolt at filter top cover, remove used filter element and put
new clean element.
Water separator
The tractor is fitted with separator (3-Fig. 5.3.3) to separate water and initial removal of fuel impurities.
The separator should be cleaned whenever there is water in it (the red ring reaches the red line on
the separator housing) or other impurities. In order to remove them, unscrew the drain plug (4-fig.
5.3.3) and drain water or/and fuel with dirt.
Bleeding the fuel system
If air enters the fuel system, it must be removed before the engine can be started.
Air can enter in to the system if:
the fuel tank is drained during normal operation,
the low-pressure fuel pipes are disconnected,
a part of the low-pressure fuel system leaks during engine operation.
In order to eliminate air from the fuel system, proceed as follows:
loosen the bleeding screw at preliminary filter cover top (5-Fig. 5.3.3),
unscrew hand primer plunger (10-Fig. 5.3.3),
loosen the banjo bolt at the fuel inlet pipe to the injection pump and operate the hand primer
until fuel, free of air, comes from the banjo bolt. Tighten the banjo bolt,
loosen the union nut at the fuelled starting aid (glow plug) and operate the hand primer until
fuel, free of air, comes from the connection. Tighten the union nut at the starting aid,
loosen the high-pressure pipe union nut at two of the injectors ,
set the throttle fully open and operate the starter motor until fuel is forced out from the pipes,
then tighten the union nuts,
operate the engine at low idle speed for minimum of two minutes immediately after air has been
removed from the system. This will ensure that the system is free of air.
Start the engine and check to ensure there are no fuel leaks.
5.3.3. Dry air cleaner.
Dry air cleaner maintenance.
Remove any accumulated dust from the dry air cleaner dust collector every 10 hours of operation, or
daily in extremely dusty conditions (Fig. 5.3.6);
Clean the outer element every 50 hours of operation, or whenever the air cleaner warning light on the
instrument panel comes on..
To clean the outer element:
Stop engine before air cleaner servicing. Do not operate engine without filter elements.
Remove the retaining wing nut and carefully slide the element out the filter housing,
Clean the element by hand. Do not beat the element against a hard surface as the element may
be damaged or distorted,
A
lternatively, compressed air not exceeding 2 kg/cm² may be used. Insert the air line nozzle
inside the element and blow the dust from the inside to the outside. Keep the nozzle at a safe
distance from the element. Blow loose particles from the outside of the element by holding the
nozzle at least 150 mm from the element,
reinstall the outer element ensuring that the rubber sealing ring on the end is secure.