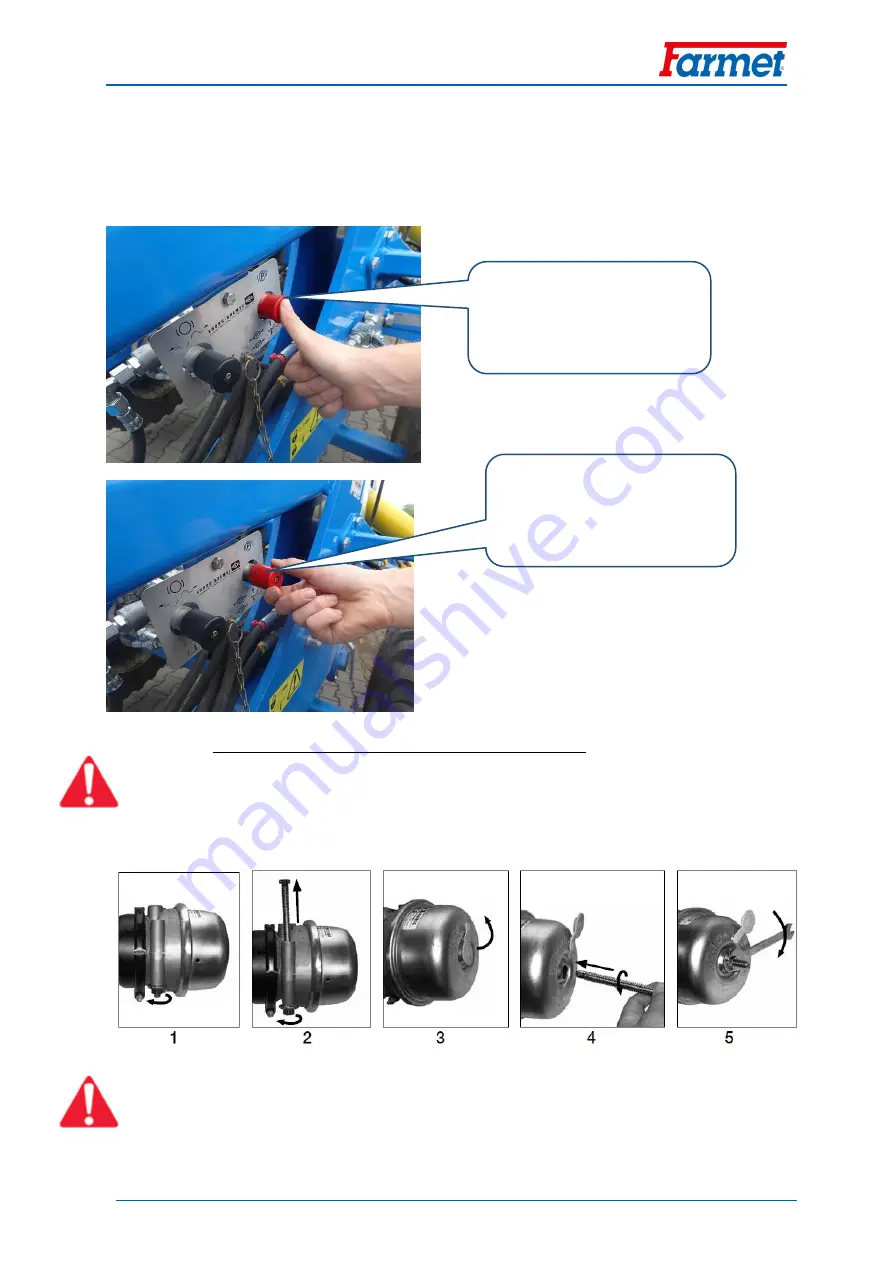
Manual
SOFTER 12,5 PS
20
│
54
Description of the manual brake control when air ducting is connected
The knob has to be pressed when travelling (there is no automatic change over).
It does not need to be used when the machine is disconnected, the brake is automatically
activated when the red quick coupling device of the tractor is disconnected.
1.4.3.
Emergency brake release in case of air leak
It is possible to release the brakes of the machine using special brake release bolts in case of a leak of air from
the brake system.
The bolts are included in the installation unit of the brake cylinder.
Emergency brake release procedure in case of air leak
Remove the bolts from the holders of the brake cylinder (Picture 1 and 2).
Release the cap on the back side of the brake cylinder (Picture 3).
Insert the bolt by its flat end (T-shape) into the opening in the cylinder and turn the bolt by 90° at the end of
the opening so that the screw is arrested and cannot be pulled out (Pic. 4).
Turn the nut (19 mm spanner) clockwise (Pic. 5). ATTENTION: Maximum torque is limited to 68Nm.
PRESSED RED KNOB
=
RELEASED BRAKES
RELEASED RED KNOB
=
APPLIED BRAKES