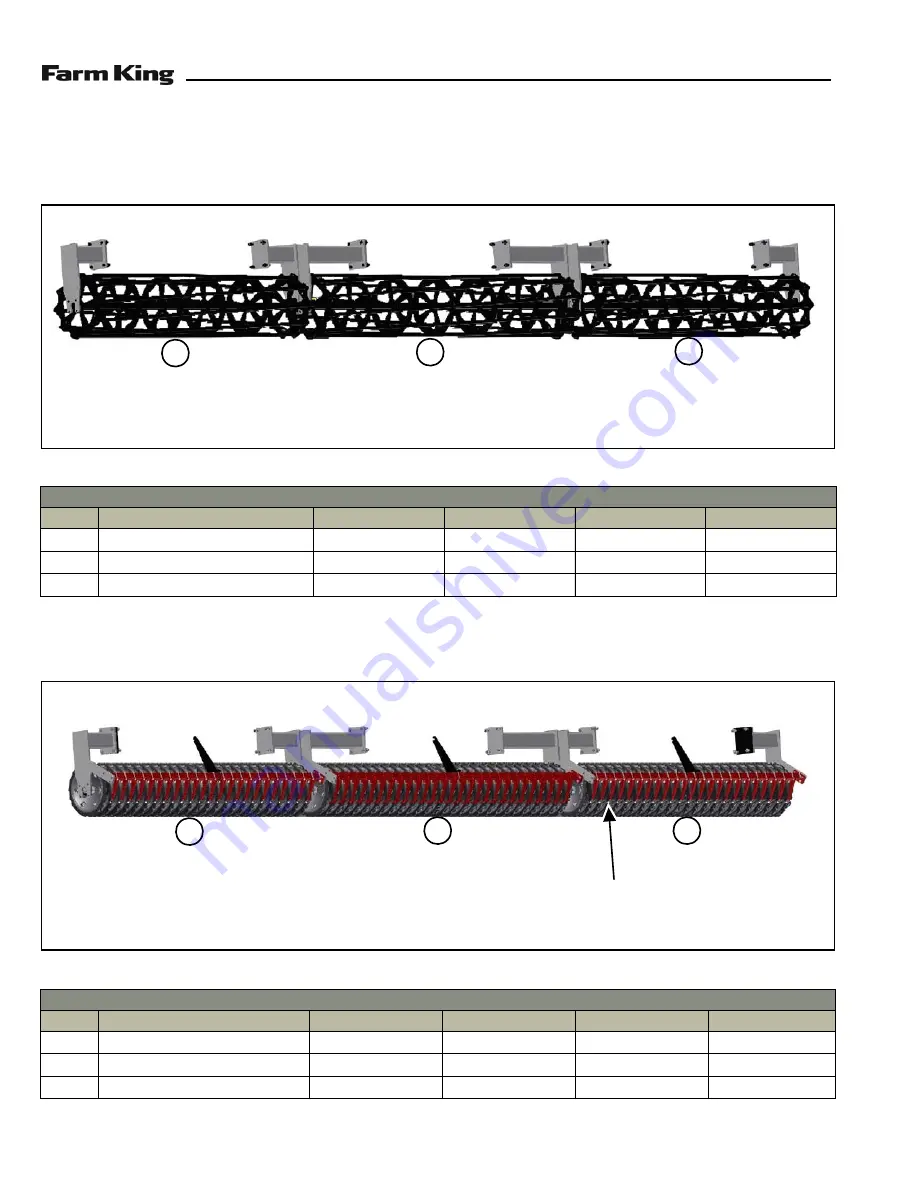
162
Specifications - High Speed Compact Disc
Cage Rollers
Figure 162
Otico Rollers
Figure 163
DIMENSIONS
ITEM
DESCRIPTION
HS8525
HS8530
HS8535
HS8540
1
WIDTH (LH and RH ROLLER)
2.1 m (6.11")
2.9 m (9.6")
3.6 m (11.1")
4.4 m (14.6")
2
CENTER CAGE ROLLER
3.4 m (11.2")
3.4 m (11.2")
3.4 m (11.2")
3.4 m (11.2")
DIAMETER
609 mm (24")
609 mm (24")
609 mm (24")
609 mm (24")
1
2
1
DIMENSIONS
ITEM
DESCRIPTION
HS8525
HS8530
HS8535
HS8540
1
WIDTH (LH and RH ROLLER)
2.1 m (6.11")
2.9 m (9.6")
3.6 m (11.1")
4.4 m (14.6")
2
WIDTH (CENTER ROLLER)
3.4 m (11.2")
3.4 m (11.2")
3.4 m (11.2")
3.4 m (11.2")
DIAMETER
527 mm (21-1/4")
527 mm 21-1/4")
527 mm (21-1/4”) 527 mm (21-1/4")
1
2
1
SCRAPER BARS
Summary of Contents for HS8525
Page 2: ......
Page 4: ...4 Table of Contents High Speed Compact Disc ...
Page 6: ...Warranty Registration High Speed Compact Disc 6 ...
Page 10: ...10 Introduction High Speed Compact Disc ...
Page 14: ...14 Safety High Speed Compact Disc ...
Page 28: ...28 Safety High Speed Compact Disc ...
Page 30: ...30 Assembly High Speed Compact Disc ...
Page 74: ...74 Assembly High Speed Compact Disc ...
Page 76: ...76 Operation High Speed Compact Disc ...
Page 92: ...92 Maintenance High Speed Compact Disc ...
Page 102: ...102 Part Identification High Speed Compact Disc ...
Page 104: ...104 Part Identification High Speed Compact Disc WHEELS TIRES WINGS 3 1 4 5 2 88717299 ...
Page 152: ...152 Part Identification High Speed Compact Disc BLADES 2 1 3 88717644 ...
Page 154: ...154 Part Identification High Speed Compact Disc ...
Page 156: ...156 Specifications High Speed Compact Disc ...
Page 166: ...166 Specifications High Speed Compact Disc ...
Page 167: ...167 Warranty High Speed Compact Disc WARRANTY WARRANTY 169 ...
Page 168: ...168 Warranty High Speed Compact Disc ...
Page 171: ......