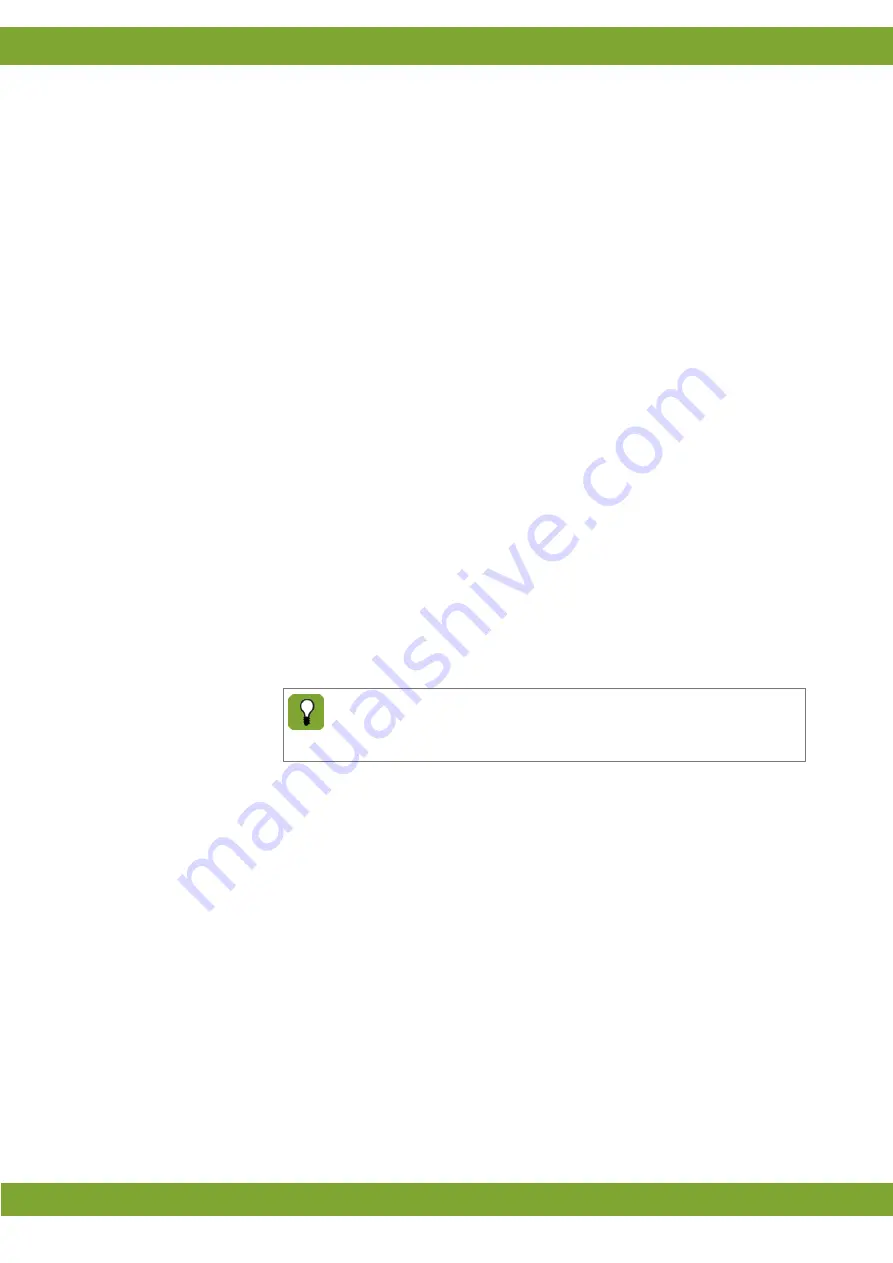
Lumina 71
Process overview
16
Stop
The active feed process will be stopped as soon as the current process is ready. The
weigher will be emptied and the feed dosed out to the hoppers. Then the control
computer will stop the feed process and set the process status to
BLOCKED(STOPPED)
.
The process will remain blocked until it is released using the option
Continue
.
Block
The process is stopped. If the feed process is active, the running process will be
finished first. The weigher will be emptied and the feed dosed to the hoppers.
The process will remain blocked until it is released using the option
Release
.
Emergency stop
The current process will be stopped immediately. Weighing, dosing in and dosing out
stop at once and the control computer gives a report. The process status will become
BLOCKED(EMERGENCY STOP)
.
Resume the feed process as follows:
After the feed process has been interrupted, it can be resumed.
Select one of the following options, depending on the feed process status:
Start
If the process status is
READY
or
ENDED
.
Continue
If the process status is
EMERGENCY STOP
or
STOPPED
.
Release
If the process status is
BLOCK
.
Reset
After an emergency stop or if the feed process is not active. Only use the reset option in
emergencies.
Read the instructions on the display before finally carrying out the reset. Restarting the
system takes longer after a reset.
Before re-starting the process ensure the system is empty, as if no feeding
cycle had been run. The weigher/blender, hopper and the transport system
must be empty.
After
Start
,
Continue
and
Release
the control computer resumes the feed process as follows:
•
If the time of the feeding cycle has not yet elapsed, the control computer will supply feed if the feeding cycle
permits this. If the feeding time has elapsed, the status will be automatically set to
FREE
so the next feeding
cycle can start as normal.
•
If the next feeding time is already active, then the next feeding cycle will start at once.