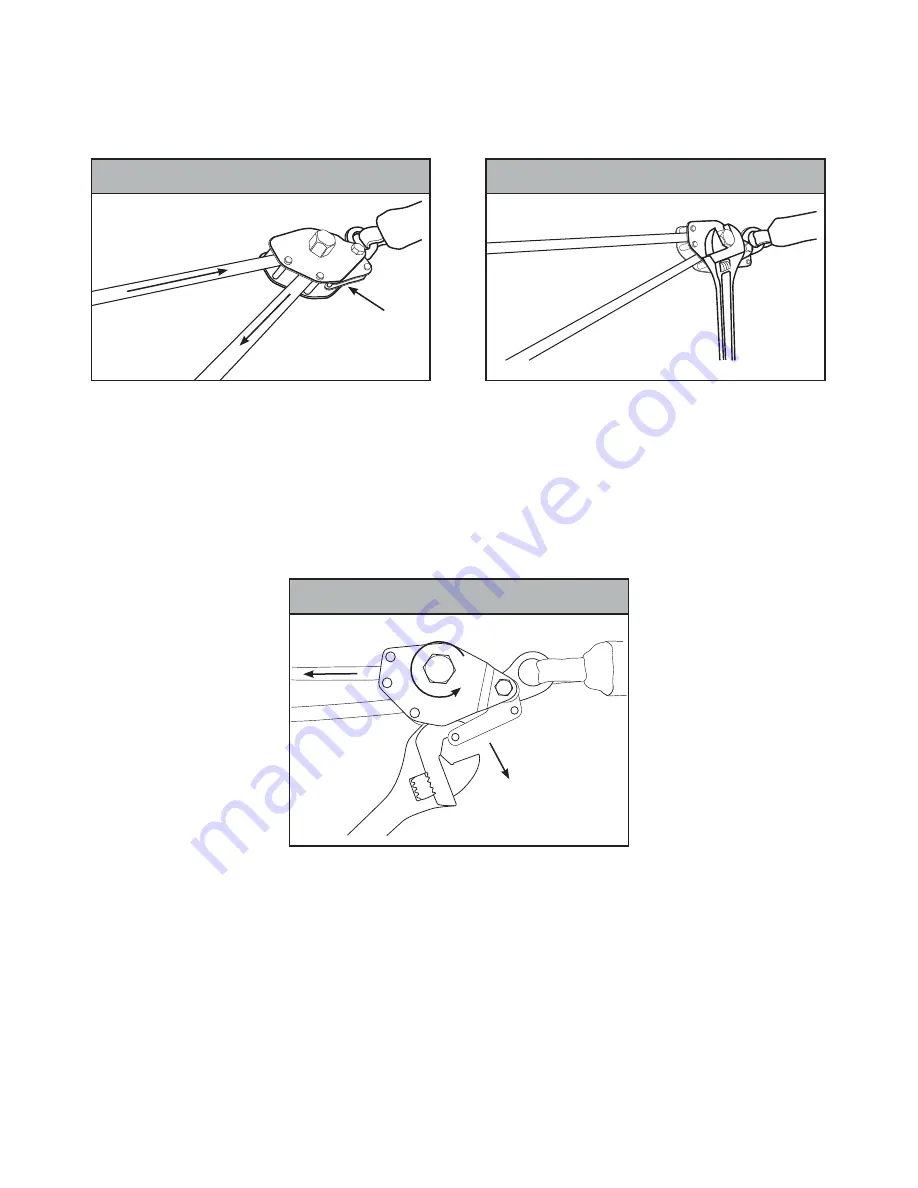
4.6
Releasing Lifeline Tension:
Upon completion of work, to move to a new work location or to disconnect from the end anchorage
connectors lifeline tension should be released. To release lifeline tension:
Step 1:
Lift the locking lever and position the pointed bar or wrench between the tensioner body and locking lever.
Step 2:
Pry upward with the pointed bar or wrench to disengage the lock lever and release the HLL tension, see Figure 12A.
Step 3:
Loosen the tensioning nut with the pointed bar or wrench by turning the tensioning nut counter clockwise until loose, see Figure
12B.
Step 4:
If necessary, the rope can be pulled through the tensioner by hand while holding the locking lever in the disengaged
position, see Figure 12C.
Step 4:
Close the locking lever into the down position so that it is engaged; Figure 10A. Remove the slack from the line by pulling the
preinstalled rope through the tensioner by hand, see Figure 10B . Insert a pointed bar through the tensioning nut or use a wrench to
tighten by turning the nut clockwise until the tensioner slips or can no longer rotate, see Figure 11. Do not alter the tensioner to achieve
greater tension. Final line tension will be approximately 200 - 300 lbf.
Step 5:
Once properly tensioned, connect a PFAS system only to the connection O-rings that have been preinstalled on the lifeline.
A
B
Figure 10 - Removing Slack
Figure 11 - Tensioning
A
B
C
Figure 12 - Releasing Lifeline Tension
MHLL05 Rev A
012920
12