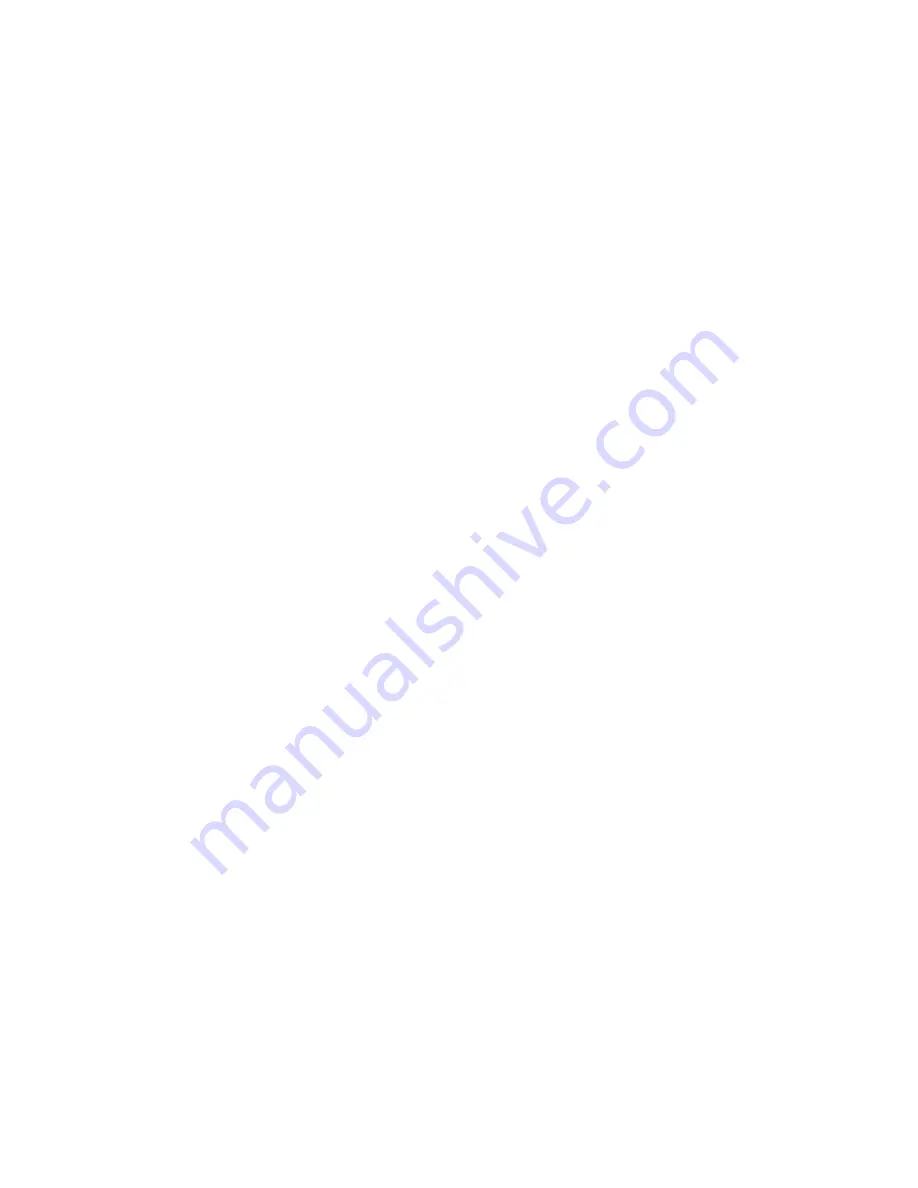
Replace parts in reverse order. Take care not to over
tighten gland nut to avoid possibility of cracking
ceramic material. The spark gap is pre-determined
and cannot be adjusted. Do not attempt to alter gap
by bending electrode.
3.7 HIGH TEMPERATURE LIMIT DEVICE
This is an electrical thermostat which interrupts
thermocouple circuit. In event of failure of control
thermostat (embodied in gas control valve), the high
temperature limit device will sense excessive oil
temperature and open - thus allowing gas valve in
control to close.
Once triggered, high temperature limit device must be
manually re-set by pressing red button on
thermostat body.
To Remove
a) Drain pan.
b) Remove front facia panel by removing fixings in
panel underside.
c) Pull off electrical connections from interrupter
situated at gas control valve rear and release
electrical leads.
d) Undo four fixings and remove control chamber
base panel.
e) Undogland nut sealing capillary tube where it
enters pan.
Note
THE SAFETY PHIAL IS THE UPPER PHIAL
f) From inside pan, release thermostat phial from
mounting bracket by moving it slightly toward rear
of pan and then upward.
g) Ease phial and capillary tube through pan fitting.
h) Remove two fixings that secure thermostat to
bracket and remove complete unit from fryer.
Replace in reverse order, taking care not to damage
capillary tube. Thereafter -
j) Press red button to ensure contacts are closed
before lighting fryer.
k) Fill pan with oil to level mark.
m) Check sealing gland does not leak but do not
overtighten gland nut.
n) Heat pan at maximum temperature setting and
allow control thermostat to cycle once or twice to
ensure that high temperature limit device does not
trigger prematurely.
Operation of safety thermostat must be checked at
regular intervals. In order to raise oil temperature
sufficiently to enable safety thermostat to operate,
it will be necessary to remove sensor bulb of control
thermostat from oil. This condition can be
accomplished by the following procedure:
a) Drain pan.
b) Remove upper panel above door by removing
fixings in panel underside.
c) Undo fixings and remove controls chamber base
panel.
d) Slacken small gland nut sealing capillary tube
where it enters fryer pan (See Figure 2).
Note
THE CONTROL PHIAL IS THE LOWER PHIAL
e) Remove phial guard and ease control thermostat
sensor towards pan rear to clear locating brackets.
Draw capillary tube through glands to enable
sensor to be suspended out of the oil when pan is
tobe re-filled tomarked level.
f) Tighten small gland nut to temporarily compress
seal on to capillary tube.
g) Temporarily refit phial guard over high limit device
sensor.
h) Refill pan with oil to marked level.
j) Install a means of measuring oil temperature.
A thermocouple-type instrument is preferable but
a mercury thermometer capable of measuring up
to300
o
C can be used. The measuring sensor,
i.e. thermocouple or thermometer bulb must be
suspended 25mm below oil surface in pan centre.
k) Light fryer and carefully observe rising oil
temperature. The safety thermostat, if functioning
properly, will shut-off gas when oil temperature is
between 218
o
C and 224
o
C (maximum).
m) If safety thermostat fails to operate at maximum of
224
o
C, shut off fryer immediately by pressing "off"
button on gas control valve (see Section 2.5,
Figure 1). Allow oil to cool before investigating
fault.
n) All safety thermostats are accurately calibrated
and checked on new appliances during
manufacture. It is unlikely that calibration will need
service adjustment assuming thermostat is not
otherwise faulty.
p) Once satisfied that safety thermostat is functioning
correctly, control thermostat sensor must be
re-located in normal position. A reversal of
procedures (a) to (h) will achieve this condition.
Note
Replace seal on control thermostat gland and ensure
that nooil leaks are present.