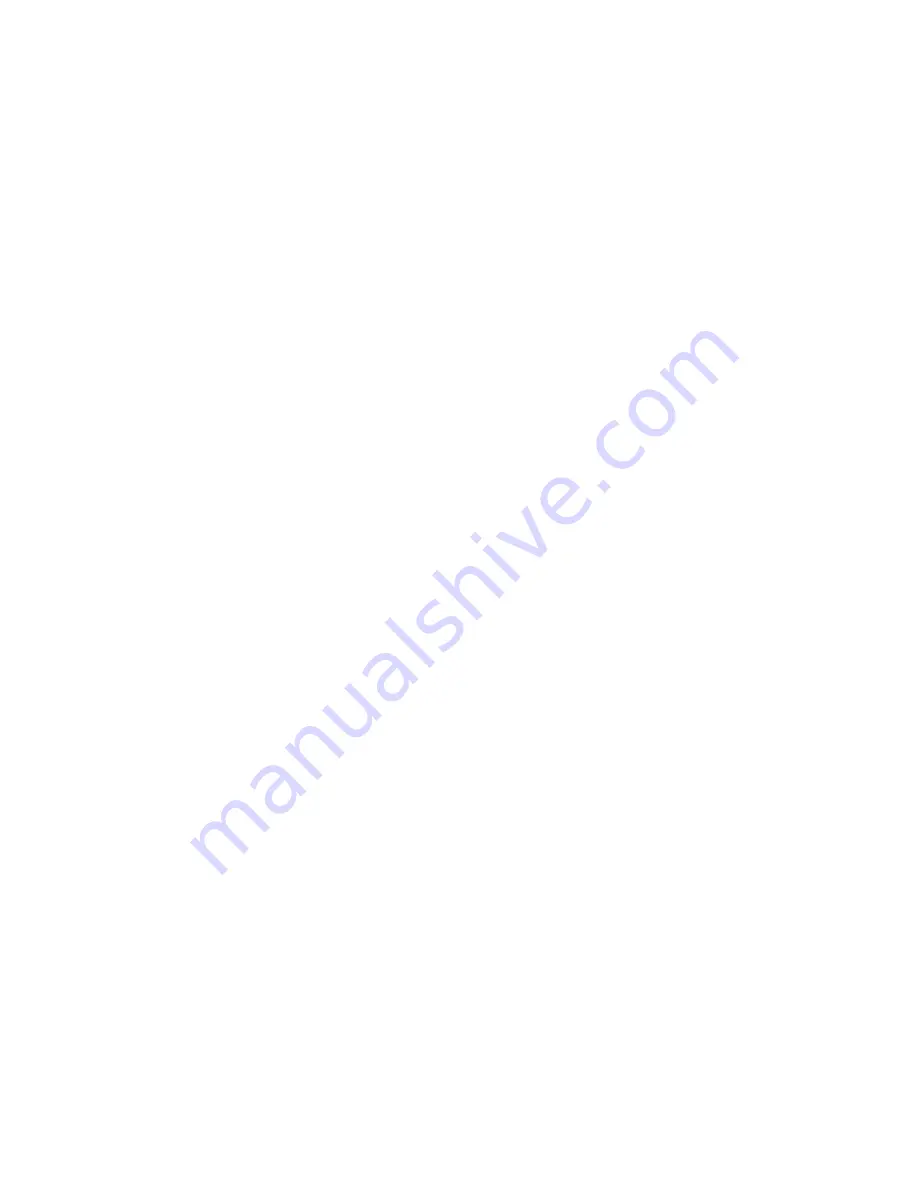
SECTION 3 - SERVICING and
MAINTENANCE
BEFORE ATTEMPTING ANY MAINTENANCE TASK,
ISOLATE THE APPLIANCE AT THE MAIN SUPPLY.
TAKE STEPS TO ENSURE THAT IT MAY NOT BE
INADVERTENTLY SWITCHED ON.
3.1 ELECTRICAL CONTROL GEAR
The terminals are located at rear of unit. The contactor is
contained within box at front.
To gain access, open door and remove cover panel
behind.
The control thermostat and neon lamps are mounted on
the facia panel, which is secured by four fixings.
3.2 NEON INDICATOR LAMPS
These must be replaced by new lamps in event of failure.
To replace a faulty lamp, first remove facia panel and pull
off push-on terminals. Remove lamp by undoing fixing nut
at rear.
3.3 THERMOSTATS
The fryer has two thermostats.
The adjustable control thermostat is mounted upon
control panel.
The safety thermostat is located within the element box.
It has a fixed setting and manual re-set button at rear of
element box. In the event of control thermostat failure and
resultant overheating of frying medium, safety
thermostat will trip supply to elements before oil
temperature becomes dangerous.
To restore circuit having rectified the fault,
it is necessary to press the re-set button. This is situated
within the turret which projects through element box rear.
The oil must be allowed to cool to enable safety
thermostat to be re-set.
A defective safety or control thermostat cannot be
repaired and must be replaced. The capillary tubes pass
through pan wall and are sealed with small glands which
must not be overtightened. The phial must be fixed in
position within pan before tightening gland. The phial tip
should protrude from protective tube by 33mm.
Thermostat capillary tube must be covered with sleeve
insulation. Safety stat phial should be located centrally
within element clip.
3.4 CONTACTOR
This should require little or no maintenance under normal
circumstances. After long service, the burner contacts
may become pitted and at that point, new contacts should
be fitted.
3.5 ELEMENTS
These are individually replaceable. Access to terminals
and fixing nuts is gained upon removing element box
cover. When fitting a new element, ensure that sealing
gasket is fitted and tighten fixing nut firmly, preferably with
the aid of a tubular box spanner or socket.
When re-fitting element box cover, check condition of oil
resistant gasket. Do not use excessive force when
securing cover as this may deform it and allow oil to enter
box.
3.6 CLEANLINESS
To maintain maximum performance, the pan must be kept
clean. Periodically, oil must be drained off and the pan
should be filled with water and detergent. Boil up contents
and drain whilst still hot before flushing out with clean
water. Thoroughly dry pan and all fittings before re-filling
with oil. The elements can be lifted and hinged backward
to gain full access to all surfaces of pan and elements.
3.7 TILT SWITCH
Located in element terminal box, this component should
require no maintenance.
SECTION 4 - SPARES
When ordering spares, quote the unit type and serial
number. This information will be found on data plate
located on cover panel behind door.
An identity label is also provided on front frame.