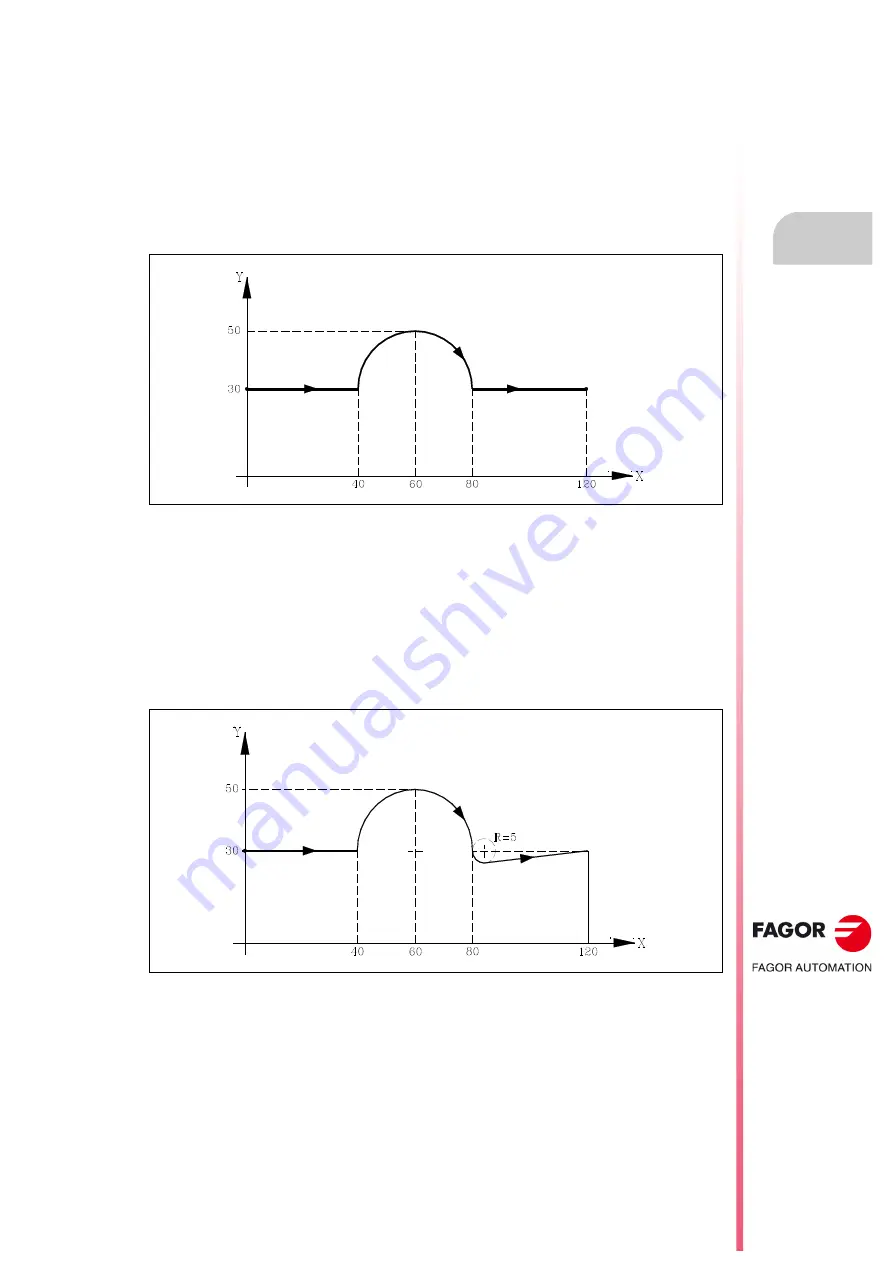
Programming manual
CNC 8055
CNC 8055i
PATH
CONTROL
6.
·M· & ·EN· M
ODELS
S
OFT
: V02.2
X
·97·
Ta
nge
ntial exit at
the
en
d of
a
machi
n
ing
o
perator
(G3
8
)
6.9
Tangential exit at the end of a machining operator (G38)
Function G38 enables the ending of a machining operation with a tangential exit of the tool. The
path should be in a straight line (G00 or G01). Otherwise, the CNC will display the corresponding
error.
Function G38 is not modal, so it should be programmed whenever a tangential exit of the tool is
required.
Value R 5.5 should always appear after G38. It also indicates the radius of the arc which the CNC
applies to get a tangential exit from the part. This R value must always be positive.
If the starting point is X0 Y30 and you wish to machine an arc (with the approach and exit paths
in a straight line), you should program :
G90 G01 X40
G02 X80 I20 J0
G00 X120
If, however, in the same example you wish the exit from machining to be done tangentially and
describing a radius of 5 mm, you should program :
G90 G01 X40
G02 G38 R5 X80 I20 J0
G00 X120
Summary of Contents for 8055 M
Page 1: ...CNC 8055 M EN Programming manual Ref 1711 Soft V02 2x...
Page 8: ...8 Programming manual CNC 8055 CNC 8055i SOFT V02 2X...
Page 12: ...12 CNC 8055 CNC 8055i Declaration of conformity and Warranty conditions...
Page 16: ...16 CNC 8055 CNC 8055i Version history...
Page 22: ...22 CNC 8055 CNC 8055i Returning conditions...
Page 24: ...24 CNC 8055 CNC 8055i Additional notes...
Page 26: ...26 CNC 8055 CNC 8055i Fagor documentation...
Page 448: ......
Page 464: ...464 Programming manual CNC 8055 CNC 8055i D M EN MODELS SOFT V02 2X Key code...
Page 466: ...466 Programming manual CNC 8055 CNC 8055i D M EN MODELS SOFT V02 2X Key code MC operator panel...
Page 467: ...Programming manual CNC 8055 CNC 8055i D M EN MODELS SOFT V02 2X 467 Key code...
Page 468: ...468 Programming manual CNC 8055 CNC 8055i D M EN MODELS SOFT V02 2X Key code...
Page 471: ...Programming manual CNC 8055 CNC 8055i D M EN MODELS SOFT V02 2X 471 Key code 11 LCD Monitor...
Page 472: ...472 Programming manual CNC 8055 CNC 8055i D M EN MODELS SOFT V02 2X Key code...
Page 478: ...478 Programming manual CNC 8055 CNC 8055i F M EN MODELS SOFT V02 2X Maintenance...
Page 479: ...Programming manual CNC 8055 CNC 8055i F SOFT V02 2X 479...
Page 480: ...480 Programming manual CNC 8055 CNC 8055i F SOFT V02 2X...
Page 481: ......