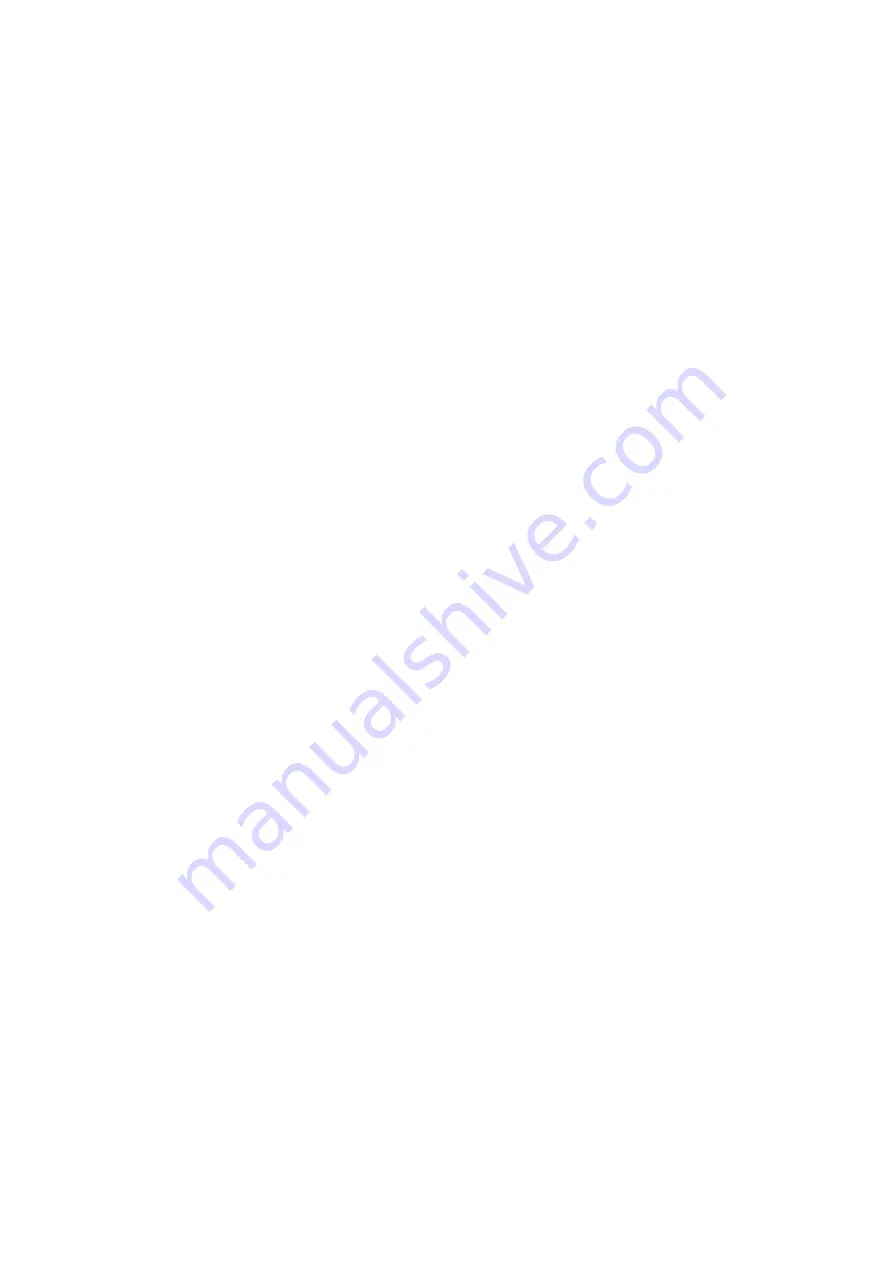
35
A.4.5 Compressed air for breathing apparatus
from EN529
A.4.5 Compressed air for breathing apparatus (EN12021)
A.4.5.1 General
A compressor system will have produced the compressed air supplied to a breathing apparatus. The compressor system
may be used for filling individual high-pressure pressure vessels or those on a mobile trolley or to supply air direct to
breathing apparatus and other air-tools used in the workplace.
Contaminants can mix in compressed air at various stages of its production and supply. Any presence of contaminants in
acceptable quantities will render the air unsuitable as “breathable air” and can threaten the health and safety of the
respiratory protective device wearer. For this reason quality assured compressed air should be supplied to a breathing
apparatus. EN12021 stipulates the minimum quality standards for breathable compressed air and includes the levels for
oxygen, carbon monoxide, carbon dioxide, lubricants, water and other types of contaminant and odour.
A.4.5.2 Compressor system
A.4.5.2.1 General
A competent person should be consulted when planning or installing a compressed air system for producing breathable
air. This will help to minimise problems associated with compressors and the down stream effects on the quality of the
air supplied. Table A.2 provides a summary of the main elements associated with a compressor system for producing
breathable air. In addition to the careful and installation of the system it should be maintained by a competent person
to ensure the safe operation of the system.
The compressor should be installed in an area providing sufficient space on all side to ensure good ventilation. The area
should be cool as possible but avoid place where freezing is possible. The air intake point should be located in open air
and away from potential contaminants (e.g. not close to ventilation outlets or in down stream of the outlets or near
vehicle exhaust emission points).
A.4.5.2.2 Air purification elements
The air purification elements should be placed in the correct sequence to ensure the delivery of acceptable quality
breathing air. These purification elements should be replaced in accordance with the advice provided by the competent
person and the manufacturers of these elements.
A.4.5.2.3 Testing and inspection
The volume flow and quality of the supplied air should be thoroughly tested as specified by a competent person after
risk assessment.
Permission to reproduce extracts of EN529 is granted by BSI. British Standards can be obtained from BSI Customer
Services, 389 Chiswick High Road, London W4 4AL. Tel: +44 (0)20 8996 9001. email:
Contains public sector information licensed under the Open Government Licence v3.0
Summary of Contents for F4500
Page 1: ...F4500 F4500ED SAFE AIR TESTER OPERATING MANUAL FAC QAM 181 Issue F 03 21 ...
Page 2: ...1 ...
Page 41: ...40 ...
Page 42: ...41 ...
Page 43: ...42 ...