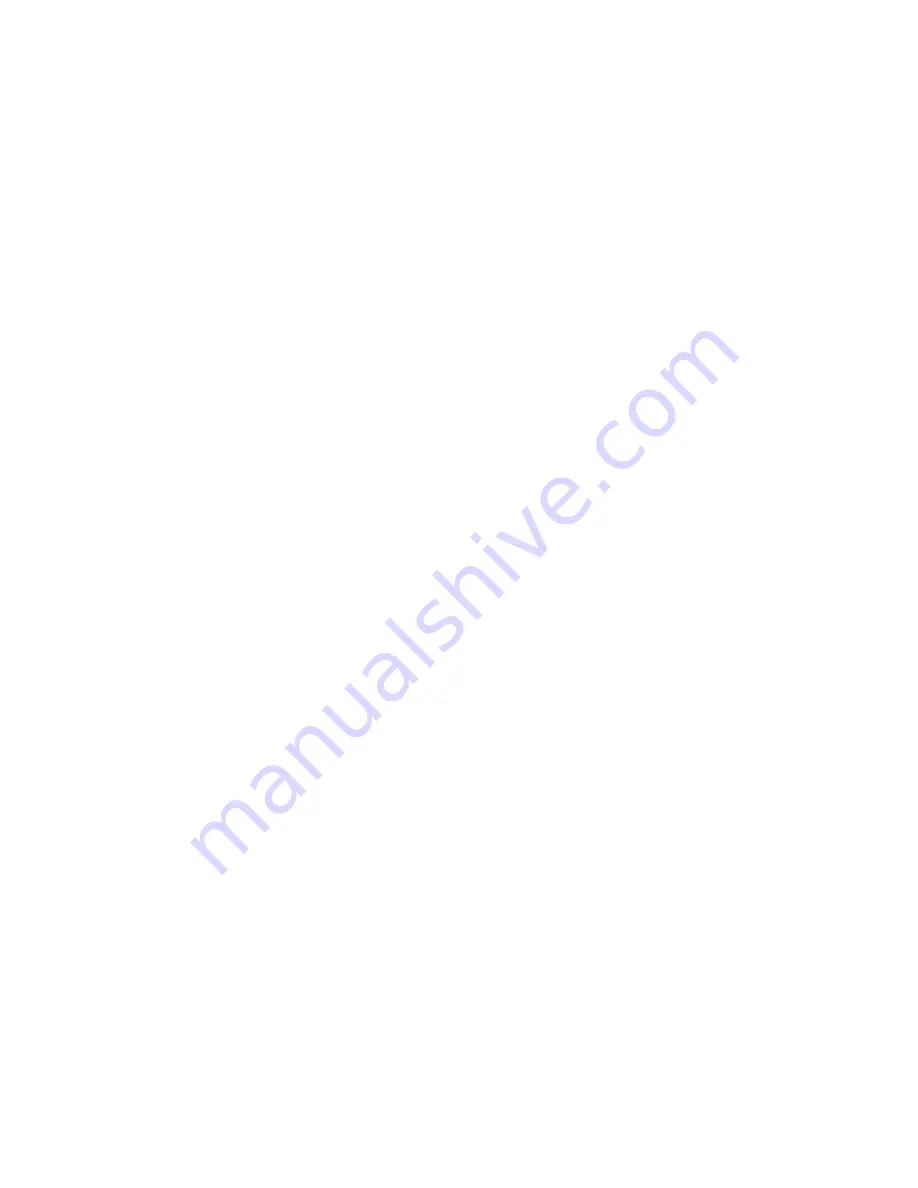
6
The 844 Compact Slide Gate Operator
General Characteristics
The FAAC 844 Compact Slide Gate Operator is
available in a rack and pinion or a chain model. The
operator comes as a package containing the drive unit
and electronic control panel. All external reversing
devices and other accessories must be ordered
separately.
The electronic control panel installed in the cover of the
844 Operator is a microprocessor-based controller that
accepts a full range of product accessories and reversing
devices to allow the maximum flexibility in designing
the gate system.
The advanced design of the operator features a small,
self-contained unit composed of an electric motor with a
built-in clutch and a reduction gear box, both housed in
a die-cast aluminum casing. The motor drives the rack
or chain to slide the gate.
An adjustable friction clutch is located on the input side
of the gear box so that when torque exceeds a preset
value, the drive torque on the output shaft remains at a
constant level. The holding power of the gear
mechanism ensures that the gate stays perfectly shut.
There is no need to fit an additional lock on the gate.
The electric motor, two-disc clutch, and reduction gear
are completely immersed in oil that lubricates the
moving parts and also dissipates heat generated during
operation. The heat is dissipated through the outer
casing of black anodized aluminum.
The Manual Release mechanism, a key- and lever-
operated device, allows you to open or close the gate by
hand whenever the need arises. The Manual Release
mechanism is useful, for example, when the electrical
power goes out and you want to open or close the gate.
A limit switch assembly stops the drive motor when the
limit switch plates mounted on the rack or chain are
sensed. The limit switch is inductive and watertight to
increase its reliability and functionality. The adjustable
electronic braking system insures that the gate stops
exactly where and when required.
Two die-cast flanges surround the pinion to prevent
foreign objects from being inserted between the rack
and pinion either accidentally or intentionally. A guard
around the sprockets on the chain version of the 844
Operator functions similarly.
Operating Logic
The 844 Operator functions with either the 844 B/C
control panel or the 844 MPS control panel. The two
panels provide two different sets of operating logics:
•
844 B/C: B, C, B/C, and C/B
•
844 MPS: E1, A1, S1, and S2
The paragraphs below explain the various logic modes.
The tables on page 8 summarize some of the
information below.
B Mode
Available only on the 844 B/C control panel, the B
mode of operation is designed for a gate system that is
attended by a person who uses a three-button switch to
open, close, or stop the gate.
In B mode you must press the switch for the movement
you desire. For example, if you want the gate to open,
you must press the
open
button on the switch. The
exception to this is when changing the direction of the
gate’s travel during opening or closing before the gate
reaches its limit stop. To change direction, you must
first stop the gate.
C Mode
Available only on the 844 B/C control panel, the C
mode of operation requires a person to attend a two
button (at least) switch to open and close the gate.
In C mode, the gate leaf moves only while the activating
button is being pressed. Thus, the attendant must press
the activating button for as long as is necessary for the
gate to fully open or fully close.
BC Mode
Available only on the 844 B/C control panel, the BC
mode of operation is a combination of B and C modes.
In BC mode, the opening logic is as described in B
mode. The closing logic of the gate is as described in C
mode.
CB Mode
Available only on the 844 B/C control panel, the CB
mode is a combination of C and B modes.
In CB mode, the opening logic is as described in C
mode. The closing logic of the gate is as described in B
mode.
E1 (Semi-Automatic) Mode
Available only on the 844 MPS control panel, the E1
(semi-automatic) operating logic is designed for users
Upswung.com
Summary of Contents for 844
Page 22: ...22 Upswung com...