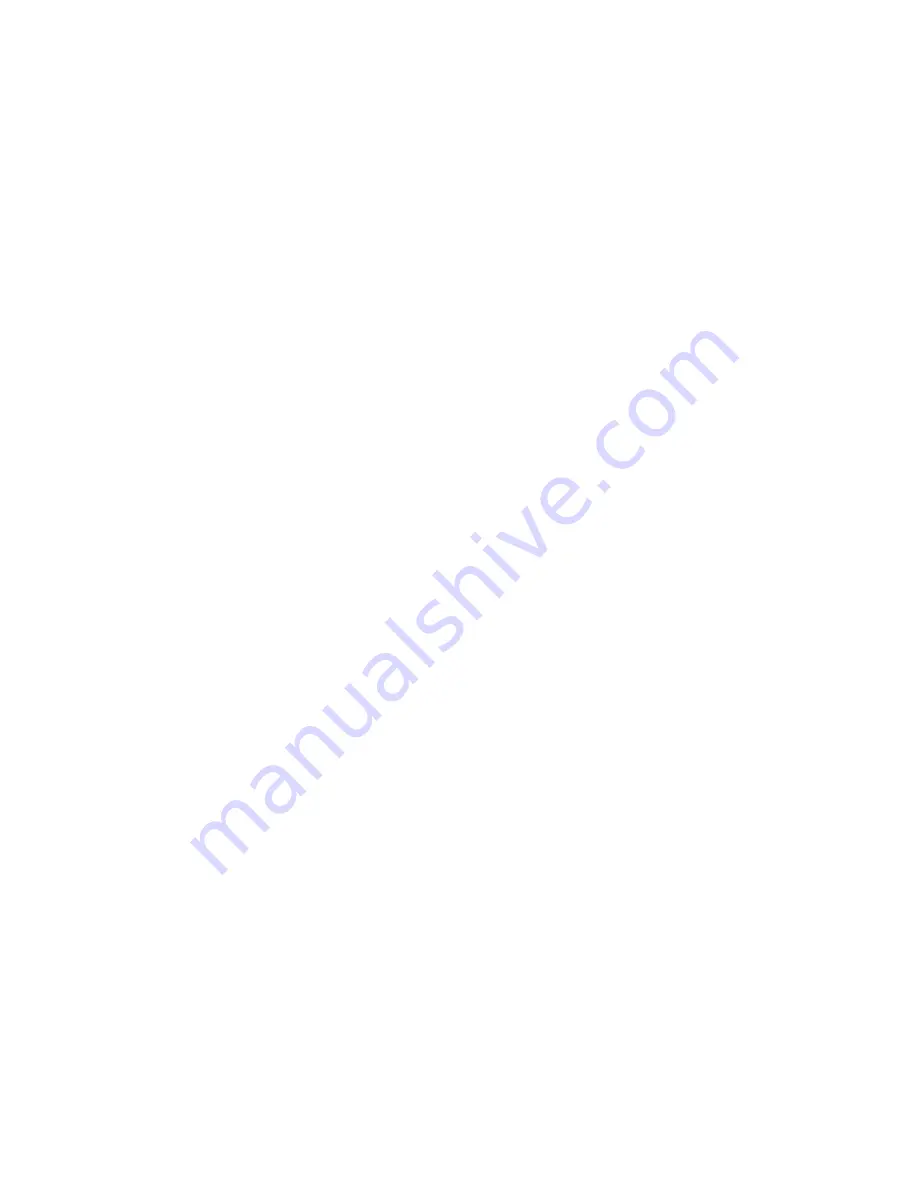
17
Checking the Motor’s
Direction of Rotation
If you are using the 844 B/C control panel, you next
need to check the direction of the motor’s rotation.
Note
: If you are using the 844 MPS control panel
you do
not
need to check the direction of rotation.
To check the motor’s direction of rotation, first make
sure the motor is disengaged with the Manual Release.
Then, move the gate by hand to the half-open position.
Now re-engage the motor with the Manual Release.
Caution:
If you check the motor’s direction of
rotation before you install the limit switch plates,
you must prevent the gate from completely opening
or closing by quickly sending a second input signal
to stop the gate. You may damage the gate if it fully
opens or closes without the smooth-braking
function of the limit switch plates.
Next turn on the main power. Send an input signal to
the operator with the activating device. The gate should
open. If it closes, turn off the main power. You need to
reverse the brown and black motor leads on the terminal
strip of the control panel. Once you have reversed the
motor leads, re-check the direction of the motor’s
rotation.
Adjusting the Braking
The 844 Operator provides up to 2 in. (5 cm) of
distance for braking the travel of the gate leaf before it
actually stops. You can adjust the force of the braking
and this distance with a potentiometer (see Figure 14 or
16, depending on your control panel).
•
Turn the potentiometer clockwise to decrease
the braking distance and increase the force of
the braking.
•
Turn the potentiometer counterclockwise to
increase the distance of the braking and
decrease the force of the braking.
Caution
: To prevent any stress to the operator, be
sure to leave about 3/4 in. (2 cm) between the fully
closed or opened gate leaf and any physical limit
stop.
Connecting Other
Accessories
WARNING!
Turn the main power off before you
make any electrical connections or set any switches
inside the cover of the 844 Operator.
The 844 B/C Control Panel
: Connect other normally
open (N.O.) opening devices in parallel to terminals 1
and 4. Connect N.O. closing devices (in parallel) to
terminals 2 and 4.
Devices to stop the gate should be normally closed
(N.C.) and should be connected (in series) to terminals
3 and 4. If your gate has no stopping device, make sure
a jumper is installed instead between terminals 3 and 4.
Connect all N.C. reversing devices in series to terminals
7 and 8 on the 844 B/C panel (Figure 15). If no
reversing devices are installed, then you must install a
jumper between the terminals.
WARNING!
Turn the main power off before you
make any electrical connections or set any switches
inside the cover of the 844 Operator.
The 844 MPS Control Panel:
Connect other normally
open (N.O.) activating devices in parallel to terminals 1
and 2. Devices to stop the gate should be normally
closed (N.C.) and should be connected (in series) to
terminals 1 and 3. If your gate has no stopping device,
make sure a jumper is installed instead between
terminals 1 and 3.
Connect all N.C. reversing devices in series to terminals
4 and 5 on the 844 MPS panel (Figure 17). If no
reversing devices are installed, then you must install a
jumper between these terminals.
Connect accessories that require 24 VAC power to
terminals 6 and 8.
Adjusting the
Clutch Torque
For safety reasons, a torque adjustment is incorporated
in the 844 Operator. According to FAAC safety
standards, the gate should stop when it meets with a
force of approximately 33 lb (15 kg).
To adjust the torque pressure, turn off the main power.
Next, hold the drive shaft with a 15 mm open end
wrench and, using a 6 mm Allen wrench, turn the clutch
adjustment screw clockwise to increase the torque and
counterclockwise to lessen the torque (see Figure 1).
Increased torque means more force is required to stop
the gate.
Caution:
Do not over tighten the clutch adjustment
screw or you may damage the clutch pin.
The torque setting can be adjusted to suit individual
requirements by estimating the force of the gate with
your hand. The gate should always stop when coming
up against a force of about 33 lb (15 kg).
Upswung.com
Summary of Contents for 844
Page 22: ...22 Upswung com...