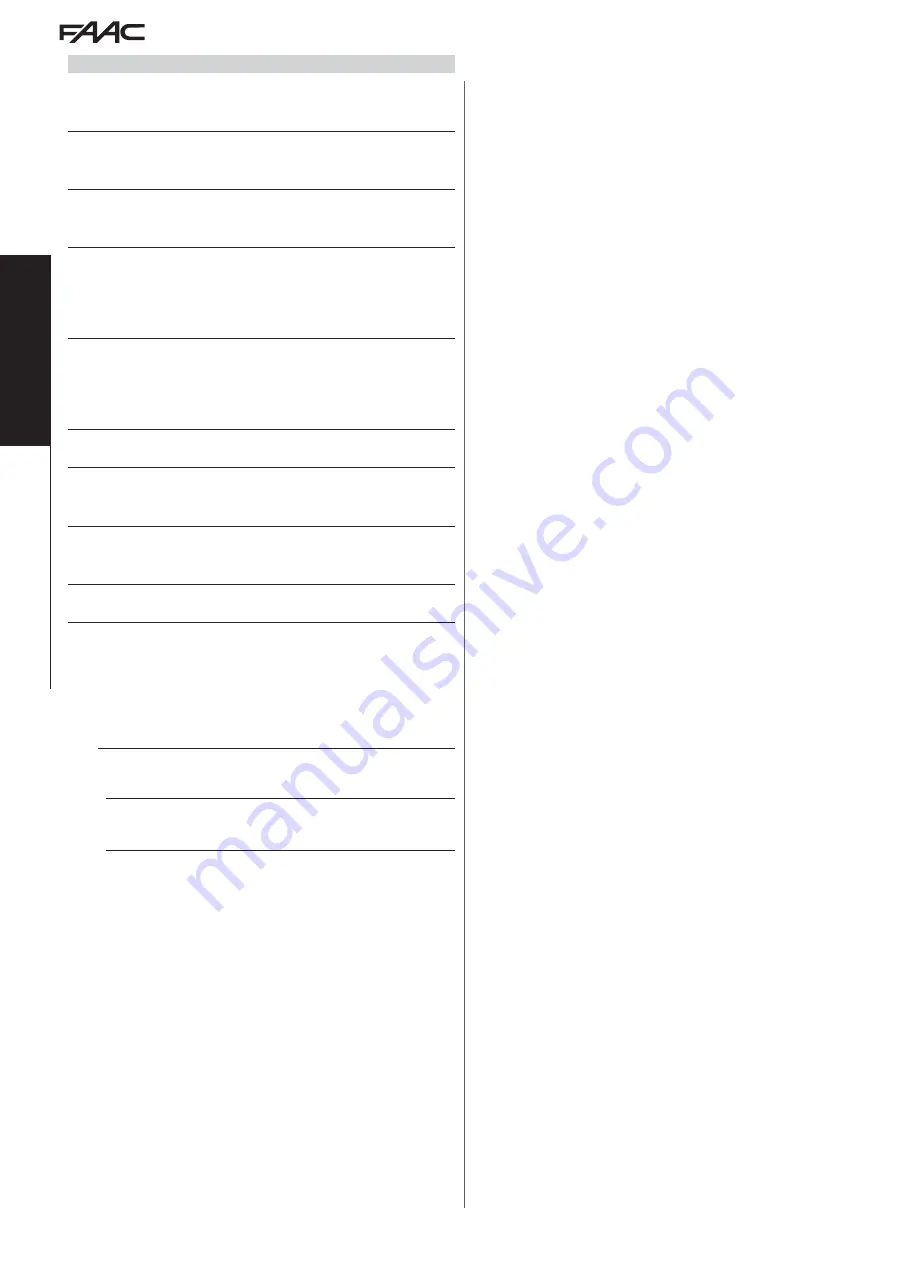
746 E R
30
732099 - Rev.D
Tr
ansla
tion of the original instruc
tions
ENGLISH
OPEN during closing, causes it to reopen.
If the closing photocells are triggered during the pause time, they
reset the pause time.
■
S
AUTOMATIC
SAFETY
This logic only requires the OPEN command to be used.
OPEN if the automation is closed, causes it to open. The automation
closes automatically after the pause time has elapsed.
OPEN during the pause, causes it to close.
OPEN during opening, causes it to close.
OPEN during closing, causes it to reopen.
If the closing photocells are triggered during the pause time, they
close the automation 5 seconds after they have been released.
■
E
SEMI-AUTOMATIC
This logic only requires the OPEN command to be used.
OPEN if the automation is closed, causes it to open.
OPEN if the automation is open, causes it to close.
OPEN during opening, stops it and the followingOPEN command
closes it.
OPEN during closing, causes it to reopen.
■
E P
SEMI-AUTOMATIC
STEP-BY-STEP
This logic only requires the OPEN command to be used.
OPEN if the automation is closed, causes it to open.
OPEN if the automation is open, causes it to close.
OPEN during opening or closing, stops it and the following OPEN
command reverses the direction.
■
C
DEAD-MAN
This logic requires the maintained OPEN and CLOSE commands to
be used.
CLOSE is obtained by the connection to terminal OPEN B (partial open-
ing is not available). The controls must be activated intentionally and
the automation must be visible.
Maintained OPEN opens the automation.
Maintained CLOSE closes the automation.
Movement stops if the photocells are triggered.
■
b
SEMI-AUTOMATIC
b
This logic requires the OPEN and CLOSE commands to be used.
CLOSE is obtained by the connection to terminal OPEN B (partial
opening is not available).
OPEN if the automation is closed, causes it to open.
CLOSE if the automation is open, causes it to close.
CLOSE during opening, has no effect.
OPEN during closing, causes it to reopen.
Movement stops if the photocells are triggered.
■
b C
MIXED (b during opening / C during closing)
This logic requires the OPEN impulse command to open and the
maintained CLOSE command to close.
CLOSE is obtained by the connection to terminal OPEN B (partial
opening is not available). The CLOSE command must be activated
intentionally and the automation must be visible.
OPEN opens the automation.
Maintained CLOSE closes the automation.
Maintained CLOSE during opening has no effect.
OPEN during closing, causes it to reopen.
Movement stops if the photocells are triggered.
ADVANCED FUNCTION
Default
Ph
Closing photocells operation (FSW CL)
Y
stop, reverse to open when released
n o
reverse, immediate open
no
oP
Opening photocells operation (FSW OP)
Y
reverse, immediate close
n o
stop with opening when released
no
EC
Encoder obstacle detection sensitivity
0 0
obstacle detection not enabled
0 1
(max sensitivity)…
9 9
(minimum sensitivity)
99
rP
Pre-limit switch deceleration
0 0
not enabled
0 1
…
9 9
duration of slowdown in steps of 0.1 s (if the encoder is not
enabled) or in steps of 1 revolution of the motor (the adjustment is more
precise if the encoder is enabled)
10
rA
Post-limit switch deceleration
0 0
not enabled
0 1
…
2 0
duration of slowdown in steps of 0.1 s (if the encoder is not
enabled) or in steps of 1 revolution of the motor (the adjustment is more
precise if the encoder is enabled)
02
PO
Partial opening (OPEN B)
level
0 1
…
2 0
05
t
Time-out
0 0
…
4 . 1
adjustment in steps of 1 s from 0 to 59, then in steps of 10 s
E.g.
4 1
= 41 s ;
4 . 1
= 4 min and 10 s (max time)
2.0
AS
Request assistance alert
Y
enabled
n o
not enabled
no
nc
Cycle counter
0 0
…
9 9
(thousands of cycles)
00
St
Exit from programming mode and display the status of the automation:
0 0
Closed
0 1
Opening
0 2
Stopped
0 3
Open
0 4
Open in pause
0 5
Failsafe test failed
0 6
Closing
0 7
Reversing
0 8
Photocells tripped
8.3 OPERATING LOGICS
The STOP command has priority over all other commands and stops the
automation in all the logics. The CLOSE command closes the automation if
it is open and stops the automation if it is opening.
■
A
AUTOMATIC
This logic only requires the OPEN command to be used.
OPEN when the automation is closed, causes it to open. The auto-
mation closes automatically after the pause time has elapsed.
OPEN during the pause, resets the pause time.
OPEN during opening, is ignored.
OPEN during closing, causes it to reopen.
If the closing photocells are triggered during the pause time, they
reset the pause time.
■
A P
AUTOMATIC
STEP-BY-STEP
This logic only requires the OPEN command to be used.
OPEN if the automation is closed, causes it to open. The automation
closes automatically after the pause time has elapsed.
OPEN during the pause, stops it and the following OPEN command
closes it.
OPEN during opening, stops it and the following OPEN command
closes it.
Summary of Contents for 746 E R Z16
Page 1: ...746 E R Z16 746 E R Z20 Translation of the original instructions...
Page 41: ...746 E R 41 732099 Rev D...
Page 42: ...746 E R 42 732099 Rev D...
Page 43: ......