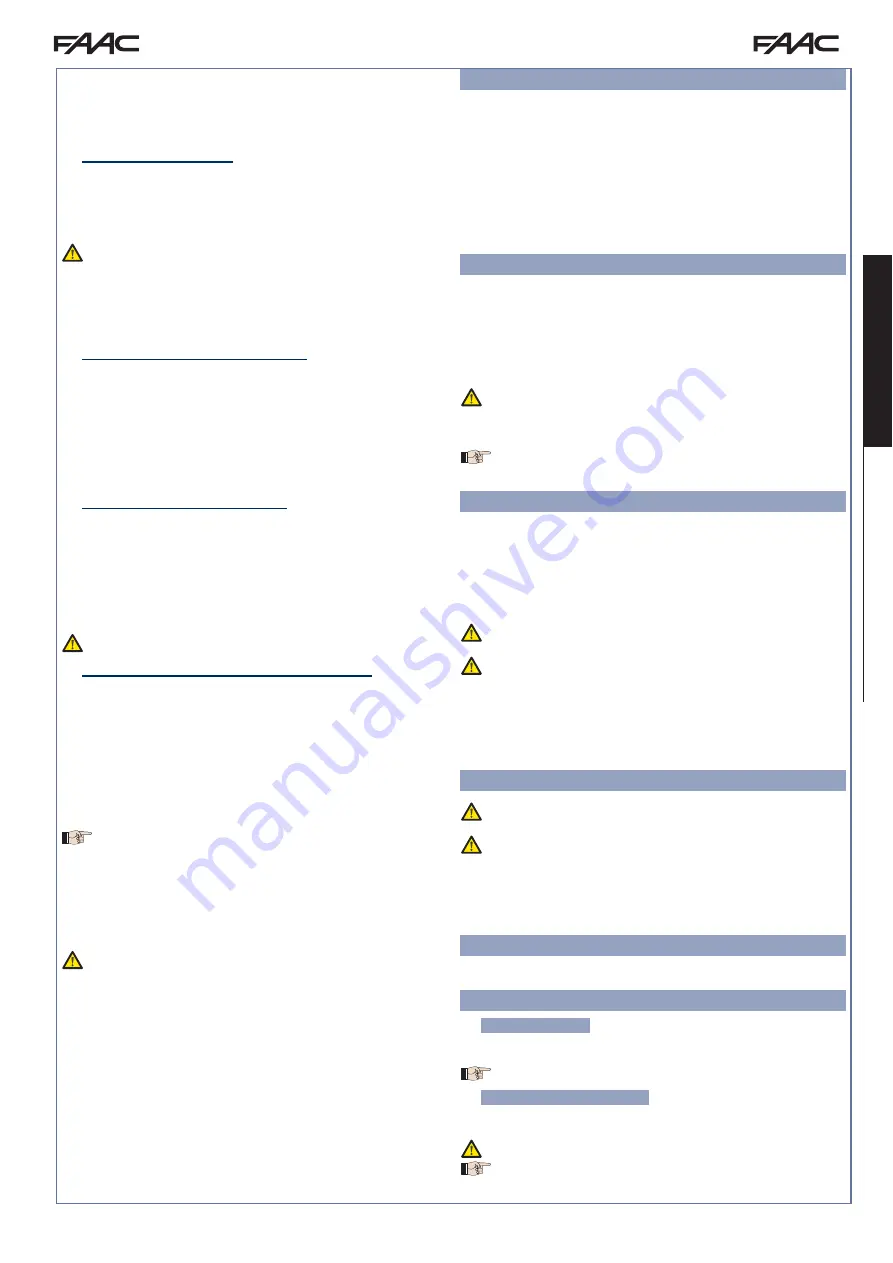
2.
Move the electrical control unit from the right side to the left,
fi
g. 8
ref.
.
3.
Insert the spring adjustment tie-rod in the hole to the right of the
electrical control unit.
4.
Move the spring
fi
xing plate,
fi
g. 8 ref.
, from the left to the right pin.
3.3.2. I
NSTALLING
THE
BAR
To correctly install the bar, follow the instructions below, depending on
the automated system model:
617 3 - 4 - 424 (F
IG
.9-10-11)
1.
Set the bar carrying plate in vertical position.
2.
Insert the bar, and secure it with the screws.
The bar rubber bumper, must be facing the bar closing direction.
617 6 (F
IG
. 12)
1.
Set the bar carrying plate in vertical position.
2.
Rest the bar, on the central pin.
3.
Position the support.
4.
Secure everything using the 6 provided screws.
3.3.3. A
DJUSTING
THE
MECHANICAL
STOPS
The 617 automated systems are factory-
fi
tted with two mechanical stops,
fi
g. 13 ref.
and
, to stop the bar in closing and opening position.
To adjust the two positions, proceed as follows:
1.
Manually set the bar in opening position.
2.
Adjust the stop height so that the bar stays in vertical position.
3.
Tighten the nut to lock in position.
4.
To adjust the other mechanical stop, manually set the bar in closing
position and continue as described above until the bar is in horizontal
position.
3.3.4. A
DJUSTING
THE
LIMIT
SWITCHES
The operators feature 2 limit microswitches that trip and stop movement of
the bar both during opening and closing. They are driven by two adjustable
cams,
fi
g. 14 ref.
and
.
To correctly adjust the two cams, proceed as follows:
1.
Manually set the bar in vertical position.
2.
Turn the corresponding cam until the limit switch trips.
3.
Set the bar in closing position and adjust the corresponding cam until
the limit switch trips.
For correct operation of the automated system, the two limit
switches must trip before the mechanical stop is reached.
3.3.5. I
NSTALLING
AND
ADJUSTING
THE
BALANCE
SCREW
To operate correctly, the automated system requires a balance screw,
fi
g.
15 ref.
, which must be ordered separately (like the bar).
The screw type used with the automated system must be chosen, among
the ones listed, depending on the type of bar and any accessories
fi
tted
on it.
For correct installation and adjustment of the spring, proceed as follows:
1.
Ensure that the operator is released, see par. 4.
2.
Remove the adjustment tie-rod,
fi
g. 15, ref.
.
3.
Keeping the bar in vertical position, connect the spring to the plate,
fi
g. 15 ref.
.
For quicker installation, we recommend keeping the open side of
the eye-bolt facing the installer.
4
Insert the adjustment tie-rod, ref.
, in the lower eye-bolt of the spring
and afterward in its
fi
xing hole.
5.
Tighten one of the two nuts,
fi
g. 15 ref.
, until spring play has been
completely restored.
6.
Manually place the bar at half travel (approx. 45°).
7.
Using the previously tightened nut, begin tensioning the spring.
The spring is correctly tensioned when it is able to keep the bar
steady once it is at 45°.
8.
Tighten the tie-rod lock nut and secure everything.
9.
Restore normal operation, as described in paragraph 5.
4. START-UP
• Proceed with the installation of the control unit following the provided
instructions.
• Verify the correct operation of the limit switches ensuring that the
corresponding LED on the unit goes off.
• Verify the correct operation of the automated system, paying special
attention to the connected safety devices.
• Properly train the end user as to the correct operation of the automated
system.
• Give the user the “User’s Guide” (the removable booklet contained in
this manual).
• Fill in the maintenance record enclosed with the “User’s Guide”.
5. MANUAL OPERATION
Should manual operation of the barrier be required due to electrical power
cut-off or inef
fi
ciency of the automated system, proceed as follows:
1.
Cut off power to the system using the differential switch located
upstream from the system.
2.
Open the door.
3.
Insert the release key,
fi
g. 16 ref.
, in the release device opening.
4.
Turn the key anti-clockwise until the mechanical stop is reached.
The mechanical stop consists of a pin, fi g. 17 ref.
. Do not go
beyond it to avoid compromising system operation.
5.
Manually move the bar, in both directions, until release of the locking
device can be felt.
If the automated system must stay released:
• remove the release key and close the door
• do not restore power to the system.
6. RESTORING NORMAL OPERATION
To restore normal operating conditions, proceed as follows:
1.
Ensure that the system is powered down.
2.
Open the door using the provided key.
3.
Insert the release key,
fi
g. 18, ref.
, in the corresponding opening.
4.
Turn the release key clockwise until it rests against the shaft,
fi
g. 18.
5.
Once the key is resting against the shaft, move the bar manually until
insertion of the release device is felt.
Once the key is resting against the shaft, do not go further to
avoid compromising operation of the device.
If turning of the release key becomes excessively diffi cult and
the key is still not resting against the shaft, try moving the
bar manually until insertion of the release device is felt. Then
continue turning the key until it is resting against the shaft.
6.
Close the door again, ensuring that the earth cable connection between
the door and the upright is intact.
7.
Restore power to the system.
8.
Ensure that the automated system is operating correctly.
7. MAINTENANCE
All automated system maintenance operations must be carried
out by qualifi ed personnel.
All system inspection and/or maintenance operations must
be carried out only after cutting off system power and with
the bar in vertical position (the balance spring must be at
minimum length).
To ensure correct operation and a constant safety level over time, every
six months perform an overall system check paying special attention
to safety devices. The “User’s Guide” contains a servicing report form.
8. REPAIRS
The end user must avoid any attempt to repair or service the system, and
must contact only quali
fi
ed FAAC personnel or FAAC service centres.
9. AVAILABLE ACCESSORIES
9.1. SKIRT KIT
The skirt kit,
fi
g. 19, allows increased visibility of the bar and is available
in lengths starting from 2 metres.
Installation of the skirt kit involves adapting of the balance spring.
9.2. ARTICULATION KIT
The articulation kit,
fi
g. 20, is designed to articulate the rigid bar allowing
installation in covered areas.
The articulation kit can be used only with 617 3 and 4 models.
Installation of the articulation kit involves adapting of the balance
spring.
T
ranslation of the original instructions
ENGLISH
617
7
532041 - Rev.B