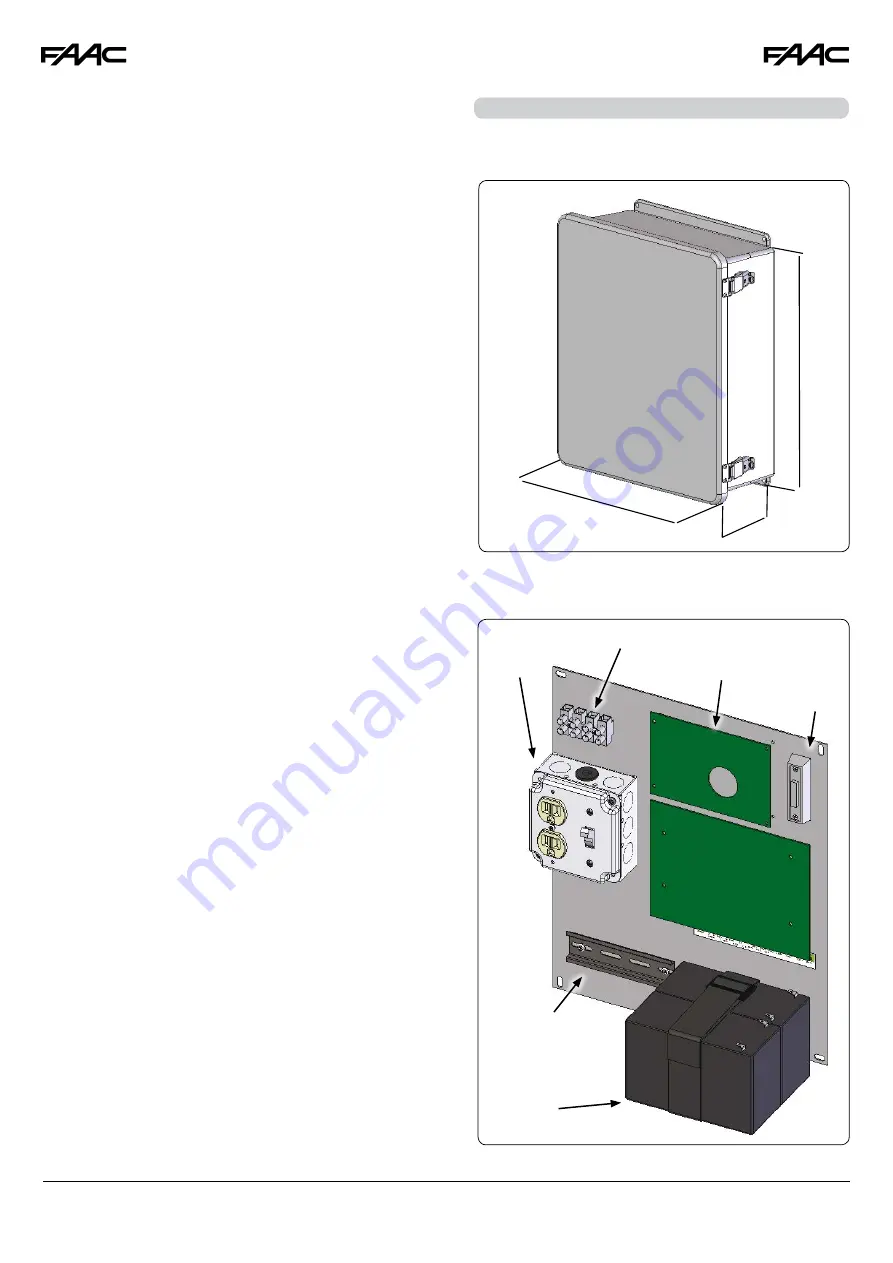
The obstacle detection function is achieved by controlling the
current absorption and / or through the encoder connected to
the motors.
If the gate encounters an obstacle during the movement of
opening or closing, the obstacle detection function is activa-
ted and the operator reverses the direction of the gate.
In case of a second consecutive obstacle the operator stops
the gate right away and any further command is inhibited.
To re-enable the automation, you must remove power (and
disconnect batteries if present) or open the STOP contact input.
The Audio Alarm output will be active until this “reset”.
This is a more detailed description of what happens after an
obstacle detection:
Gate opening, obstacle detected:
Gate reverses partially (for 3 sec.) and STOPS. After that either
the gate is in a halfway position or completely closed
An open_A command is received:
the Gate tries to open from the current position:
If there is another obstacle detection:
complete stop, alarm goes off
If the gate reaches the open position:
obstructions count reset, return to normal operations
Gate closing, obstacle detected:
Gate reverses partially (for 3 sec.) and STOPS. After that either
the gate is in a halfway position or the gate is completely open
An open_A command is received:
In NON Automatic mode:
if the gate was not completely open:
execute
an
open
if the gate was completely open:
execute
a
close
in Automatic mode:
if the gate was not completely open:
execute an open, wait for the pause
time and then closes.
if the gate was completely open:
reload the pausetime, and then closes
If there is another obstacle detection:
complete stop, alarm goes off
If the gate reaches the close position:
obstructions count reset, return to normal operations
7. At the point where you want the slowdown to start give an
OPEN A command with the push button or the remote that
is already stored in memory. Leaf 2 starts to slow down and
stops when it reaches the mechanical stop or FCA2.
8. Leaf 2 starts to close at the set speed (trimmer speed).
9. At the point where you want the slowdown to start give an
OPEN A command with the push button or the remote that
is already stored in memory. The leaf 2 starts to slow down
and stops when it reaches the mechanical stop or FCC2.
10. Leaf 1 starts to close at the set speed (trimmer speed).
11. At the point where you want the slowdown to start give an
OPEN A command with the push button or the remote that
is already stored in memory. Leaf 1 starts to slow down and
stops when it reaches the mechanical stop or FCC1.
12. The manual time learning procedure is complete.
15
15/32
”
6 7/32”
17
15/32
”
The E024U board is supplied on a panel that fits in a 16x14”
enclosure.
On the back panel there are: the control board, the power supply
and additional accessories.
Power Supply
AC connection
Power outlet
and switch
(optional)
Pushbutton
(optional)
E24U board
DIN rail
Batteries
6.3 OBSTACLE DETECTION FUNCTION
7. ENCLOSURE
A12