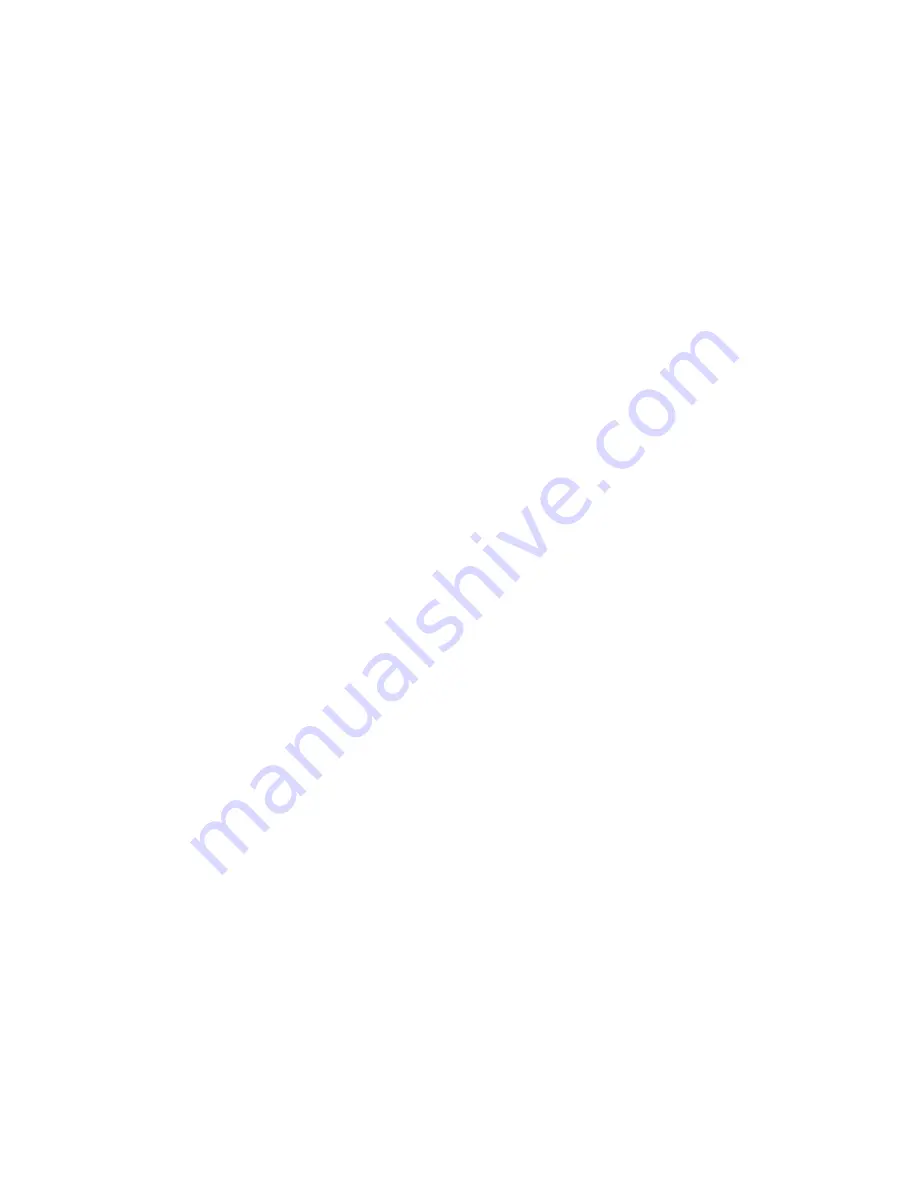
Page 32
ASSEMBLY INSTRUCTIONS CONTINUED:
i) See Fig. 30. Install one (1) 3/8" x 90 degree (9.39 mm) swivel street elbow into the barrel end port of the front R.H. 5" x 36" (127 mm x 914 mm)wing
lift cylinder. Install one (1) 3/8" x 90 degree (9.39 mm) street elbow, into the shaft end port of front R.H. 5" x 36" (127 mm x 914 mm) wing lift
cylinder.
j) See Fig. 30. Install one (1) 1/4" x 54" (6.35 mm x 1372 mm) hydraulic hose, to the 3/8" x 90 degree (9.39 mm) swivel street elbow on the shaft end
port of the front L.H. 5" x 36" (127 mm x 914 mm) wing lift cylinder, and fasten opposite end to one (1) 3/8" (9.39 mm) steel cross, placed on the
L.H.S. of the L.H. lockup valve. Fasten one (1) 1/4" x 54" (6.35 mm x 1372 mm) hydraulic hose, to the 3/8" x 90 degree (9.39 mm) swivel street elbow
on the shaft end port of the front R.H. 5" x 36" (127 mm x 914 mm) wing lift cylinder and fasten opposite end of 3/8" (9.39 mm) steel cross.
k) See Fig. 30. Install one (1) 3/8" x 100" (9.39 mm x 2540 mm) hydraulic hose to the 3/8" (9.39 mm) tee on the shaft en d port of the rear L.H.
5" x 36" (127 mm x 914 mm) wing lift cylinder and fasten opposite end to the 3/8" (9.39 mm) steel cross on front of frame. Run hose through the
lower L.H. hole in the front wing lift cylinder lug.
l) See Fig. 30. Install one (1) 3/8" x 30" (9.39 mm x 762 mm) hydraulic hose to the 3/8" x 90 degree (9.39 mm) swivel street elbow on the barrel end
of the front L.H. 5" x 36" (127 mm x 914 mm) wing lift cylinder, and fasten opposite end to the 3/8" (9.39 mm) steel cross attached to the L.H. lockup
valve.
m) See Fig. 30. Install one (1) 3/8" x 20" (9.39 mm x 508 mm) hydraulic hose to the 3/8" x 90 degree (9.39 mm) swivel street elbow on the barrel end
of the front R.H. 5" x 36" (127 mm x 914 mm) wing lift cylinder, and fasten opposite end to the 3/8" (9.39 mm) steel cross attached to the L.H. lockup
valve.
n) See Fig. 30. Install two (2) 3/8" x 172" (9.39 mm x 4369 mm) hydraulic hoses to the front port of the hydraulic lockup valves, and run hoses to front
of hitch.
o) See Fig. 30. Install one (1) 3/8" x 178" (9.39 mm x 4521 mm) hydraulic hose, from the 3/8" (9.39 mm) steel cross, to the front of disc.
28.
SECURING HYDRAULIC HOSES TO FRAME
- See Fig. 28 for machines with narrow wings. See Fig. 30 for machines with wide wings.
Fasten hoses to frame with one U-shaped hose clamp at each hose hold down point. Each hold down point has a 1/2" (12.7 mm) hex. nut welded to the
top of frame. The hold down clips are supplied in two widths, one for two hoses and one for four hoses. Place hose clamp over hoses and fasten clamp
to weld-on nut with one 1/2" x 3/4" (12.7 mm x 19.0 mm) bolt c/w lockwasher.
29.
HOW MAIN LIFT ROCKSHAFT HYDRAULIC SYSTEM WORKS
- See Fig. 28.
When raising the disc, oil is pumped into the barrel end port of centre frame cylinder causing the cylinder to extend. Oil is then forced from the shaft end
port of same cylinder into the barrel end port of the 3-1/2" x 24" (88.9 mm x 610 mm) cylinder on L.H. side causing wing cylinder to extend. Oil is then
forced from the shaft end port of the 3-1/2" x 24" (88.9 mm x 610 mm) cylinder into the piston end port of the 3" x 24" (76.2 mm x 610 mm) wing cylinder
on R.H.S. causing wing cylinders to extend. The oil from shaft end port of the 3" x 24" (76.2 mm x 610 mm) cylinder on R.H.S. is returned to the tractor.
When lowering disc, oil flows from tractor to shaft end port of the
3" x 24"
(
76.2 mm x 610 mm
) wing cylinder, causing wing cylinder to contract. Oil forced
from piston end port of the
3" x 24"
(
76.2 mm x 610 mm
) wing cylinder flows to shaft end port of L.H.
3-1/2" x 24"
(
88.9 mm x 610 mm
) cylinder, causing
cylinder to contract. The oil forced from the piston end port of the L.H.
3-1/2" x 24"
(
88.9 mm x 610 mm
) wing cylinder flows to shaft end port of main frame
4" x 24"
(
101.6 mm x 610 mm
) cylinder causing cylinder to contract. The oil from piston end port of the
4" x 24"
(
101.6 mm x 610
mm
) cylinder is returned
to the tractor.
NOTE: Lockup valve must be open to allow oil to flow to and from lift cylinders.
All cylinders extend and contract at the same rate because the amount of oil flowing between the shaft end ports and the piston end ports is equal in
volume. For example, the 4" x 24" (101.6 mm x 610 mm) main frame cylinder has a 2" (50.8 mm) diameter piston shaft which displaces enough oil from
the shaft side to fully extend the 3-1/2" x 24" (88.9 mm x 610 mm) L.H. wing cylinder. The same method is used between the 3-1/2" x 24"
(88.9 mm x 610 mm) L.H. wing cylinder and the 3" x 24" (76.2 mm x 610 mm) R.H. wing cylinder.
Each lift (rockshaft) cylinder contains a by-pass to allow oil to flow past piston when each cylinder is fully extended. If all cylinders are not fully extended
when disc is raised, continue to pump oil into lift cylinders until all cylinders are fully extended.
Summary of Contents for 4600 DISC
Page 15: ...Page 14 ...
Page 29: ...Page 28 ...
Page 31: ...Page 30 HYDRAULIC SYSTEM FOR DISCS WITH WIDE WING FRAMES ...
Page 35: ...Page 34 ...
Page 54: ...Page 53 PAGE 53 HAS BEEN LEFT OUT INTENTIONALLY ...
Page 56: ...Page 55 MODEL 4600 DISC ...