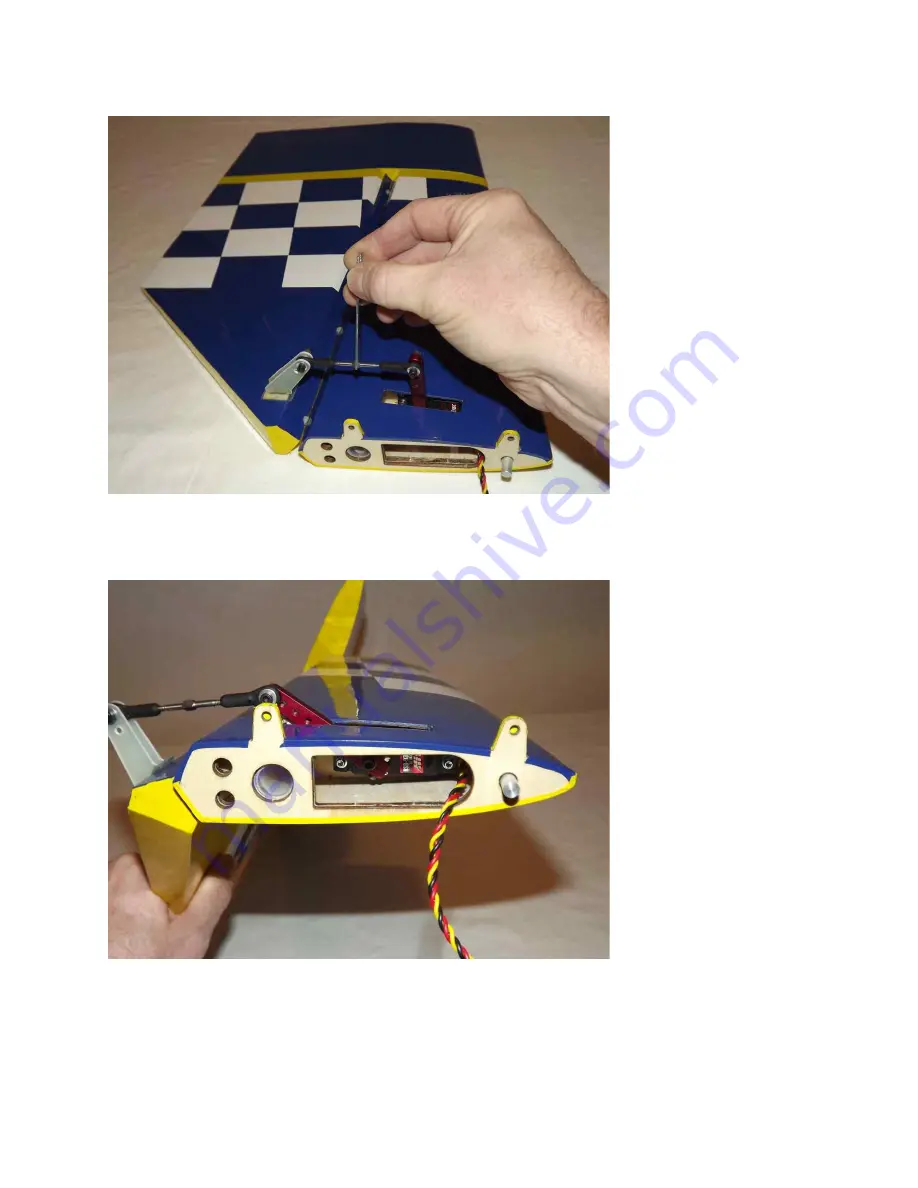
21. With the servo arm centered (as described in Step 17), adjust the turnbuckle on
the control rod until the elevator is in the neutral position.
22. Set the servo endpoints to achieve maximum travel. You may need to enlarge the
size of the servo arm exit slot. Repeat these steps for the other stab assembly.
Note: Now is a good time to take a covering iron and go over all of the seams with a
medium heat setting, paying special attention to the ends of thin trim stripes. At this
point, clean the 2 elevator/stab assemblies with Windex and a soft cloth and put them
away in their protective bag.
17