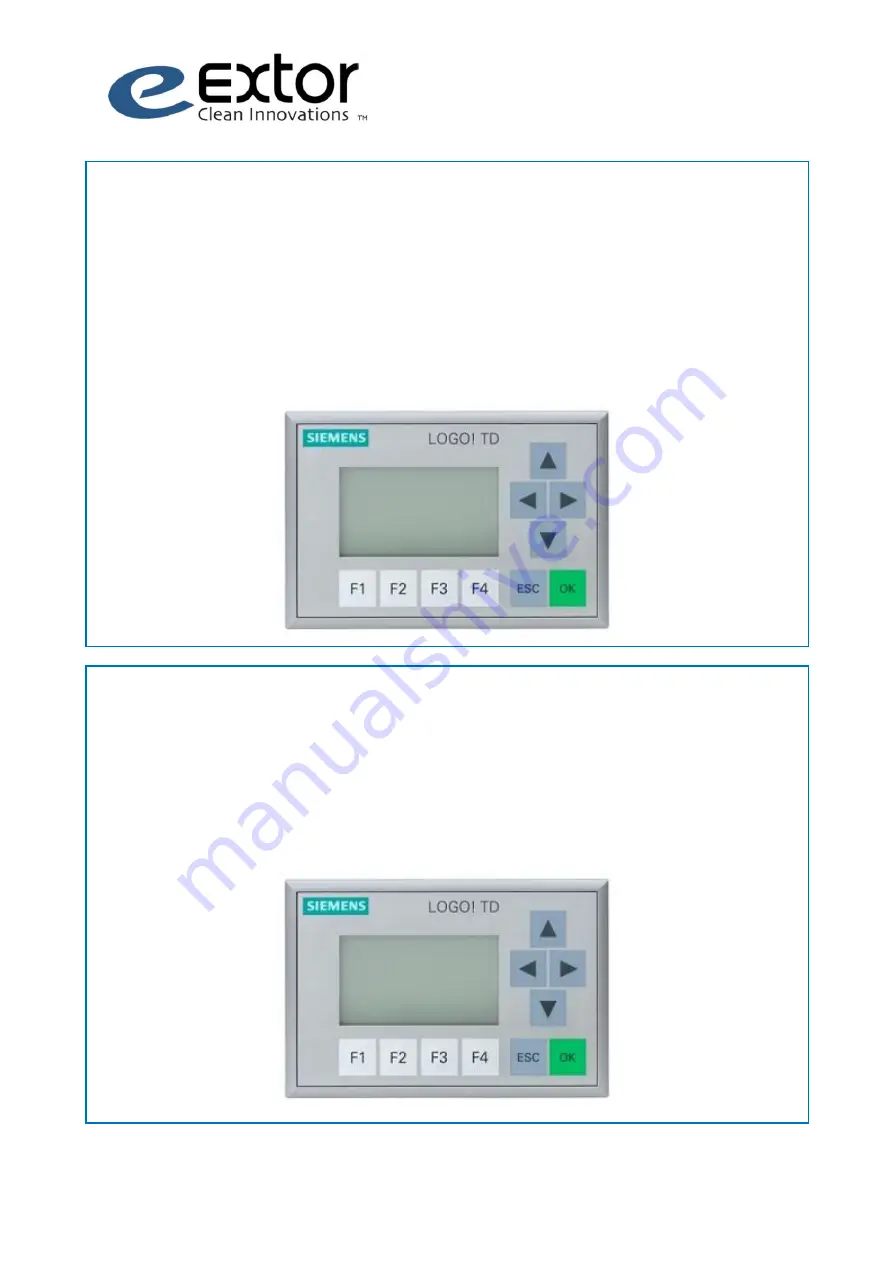
Page
21
/
37
CLEANING AFTER USE
Cleaning after use begins when you press the 'F2' button to stop the suction machine. The
suction machine continues to operate, with the suction inlet closed, during cleaning. It is
possible to change the number of cleaning rounds from the display device or via the control
centre logic display. The factory has pre-defined 10 cleaning rounds.
CLEANING DURING USE
The filter cleaning system has been designed to be fully automatic. The cleaning round begins
when the pressure loss of the filters is high enough. Cleaning ends when the pressure limit set
has been reached. It is possible to change the pressure limit thresholds for cleaning from the
display device or from the control centre logic display. The factory has pre-defined pressure
limits for filter cleaning for Cleaning on 3000 and for Cleaning off 2000 Pa.
Cleaning on
3000 pas
Cleaning off
2000 pas
Cleaning
rounds
10