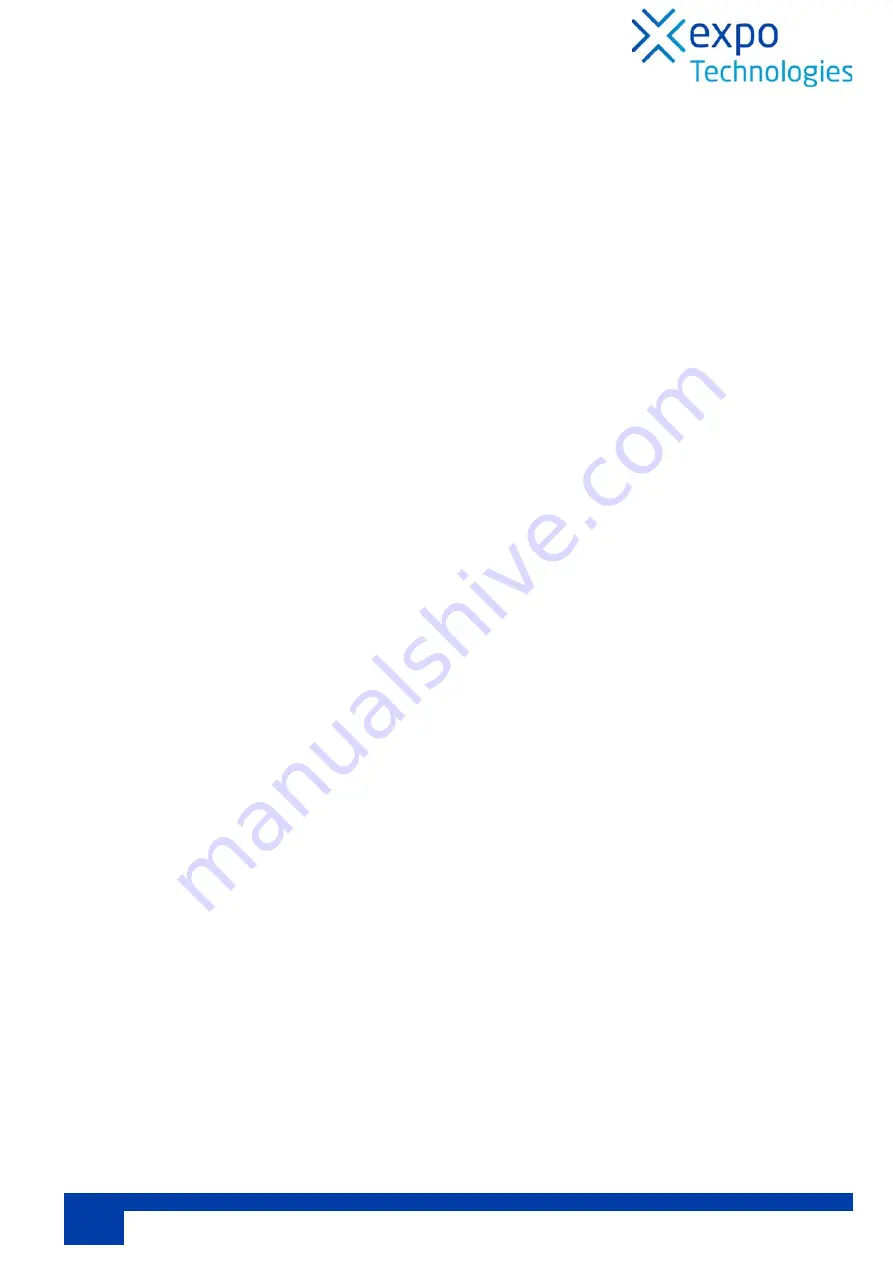
Page
13
ML548 | v11
Expo Technologies UK
T: +44 (0) 20 8398 8011
Expo Technologies US
T: +1 (440) 247 5314
Expo Technologies China
T: +86 532 8906 9858
The switch must be replaced after any short circuit that occurs within the main circuit; the switch is a
piece of encapsulated equipment and as such it is not possible to check the state of the contacts. Technical
modifications to the switch are not permitted.
Prior to commissioning, check that the terminal box is clean, the connections have been made properly, the
cables laid correctly and all screws in the terminals are secure.
In all cases the application and isolation of power must be controlled by the MiniPurge
®
system using the
power interlock signal.
No switches are permitted between the power switch and the MiniPurge
®
system other than an authorized
manual override circuit.
The safe use of this switch is the responsibility of the user, all electrical installations must conform to local
codes of practice.
Exception
Power to apparatus that is already suitable for use in hazardous locations need not be isolated by the
MiniPurge
®
system.
Section 7: Commissioning
Commissioning the System
Note: The steps 11 and 15 to 21 represent detailed commissioning tests
The following equipment is needed for this process:
• Continuity meter
• Gauge manometer (0 to 200 mbarg)
• Differential manometer
• 2 off 4mm plugs
If, after commissioning, the system does not perform as expected, refer to the Fault Finding Section.
Follow the steps as outlined:
1. Connect power to the heater via terminals 1 (Live) 4 (Neutral) and where required 3(Earth) of the Ex d
junction box and check continuity across terminals. An earth terminal is also provided within the junction
box if required. Purging is permissible only when an internal temperature of -10°C or greater has been
validated by purge environment RTD sensor.
2. Check all connections and that the Relief Valve Unit is fitted correctly with an unobstructed path to the
purge exhaust.
3. Set CLAPS regulator & Purge Flow Regulator to 0.
4. Fully open external supply shut-off valve where fitted.
5. Check that the internal logic pressure gauge reads 2.5 barg / 36 psi / 250 kPag.
6. Check that the pressure gauge on main air supply reads 4.2 barg / 61 psi / 420 kPag.
7. Check that the Pressure Relief Valve is correctly set by isolating the High-Pressure Sensor and Purge
Outlet Valve. To do this locate High-Pressure/Open Purge Outlet Signal bulkhead. Follow nylon tube back to
the y-piece connector. Remove tube & plug.
• Remove red plug from the top of the Minimum Pressure Sensor and connect a gauge manometer.
• Raise the internal pressure by turning the CLAPS regulator clockwise till the Low-Pressure Alarm
Indicator turns green. This activates the Purge Flow Regulator.
• Slowly open the Purge Flow Regulator until the Pressure Relief Valve opens. This is the set point.
Summary of Contents for D760-ET MiniPurge
Page 32: ......
Page 33: ......
Page 34: ......
Page 35: ......
Page 36: ......
Page 37: ......
Page 38: ......
Page 39: ......
Page 40: ......
Page 41: ......
Page 42: ......
Page 43: ...2...
Page 44: ...2...
Page 45: ......
Page 46: ......
Page 47: ......
Page 48: ......
Page 49: ......
Page 50: ......