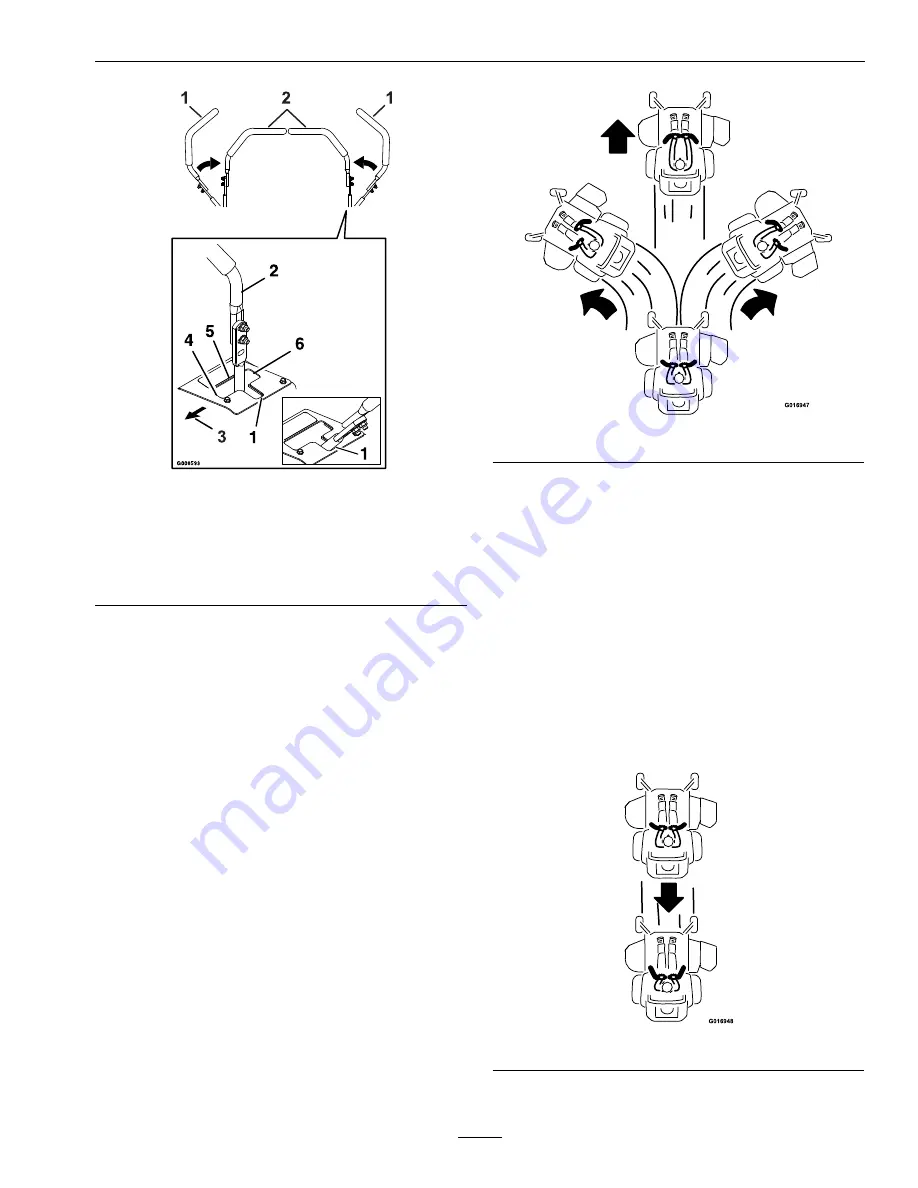
Operation
Figure 13
1.
Neutral lock position
(handles out)
4.
Forward
2.
Neutral operate position
(handles in)
5.
Neutral (operate)
3.
Front of Unit
6.
Reverse
Driving Forward
1. Release the parking brake.
2. Move the motion control levers inward to the
center to the neutral position.
3. To move forward in a straight line, move both
levers forward with equal pressure.
Figure 14
To turn left or right, pull the motion control lever
back toward neutral in the desired turn direction.
The machine will move faster the farther the
motion control levers are moved from the neutral
position.
4. To stop, position both motion control levers in
the neutral operate position.
Driving in Reverse
1. Move the motion control levers inward to the
neutral operate position.
2. To move rearward in a straight line, move both
levers rearward with equal pressure.
Figure 15
29