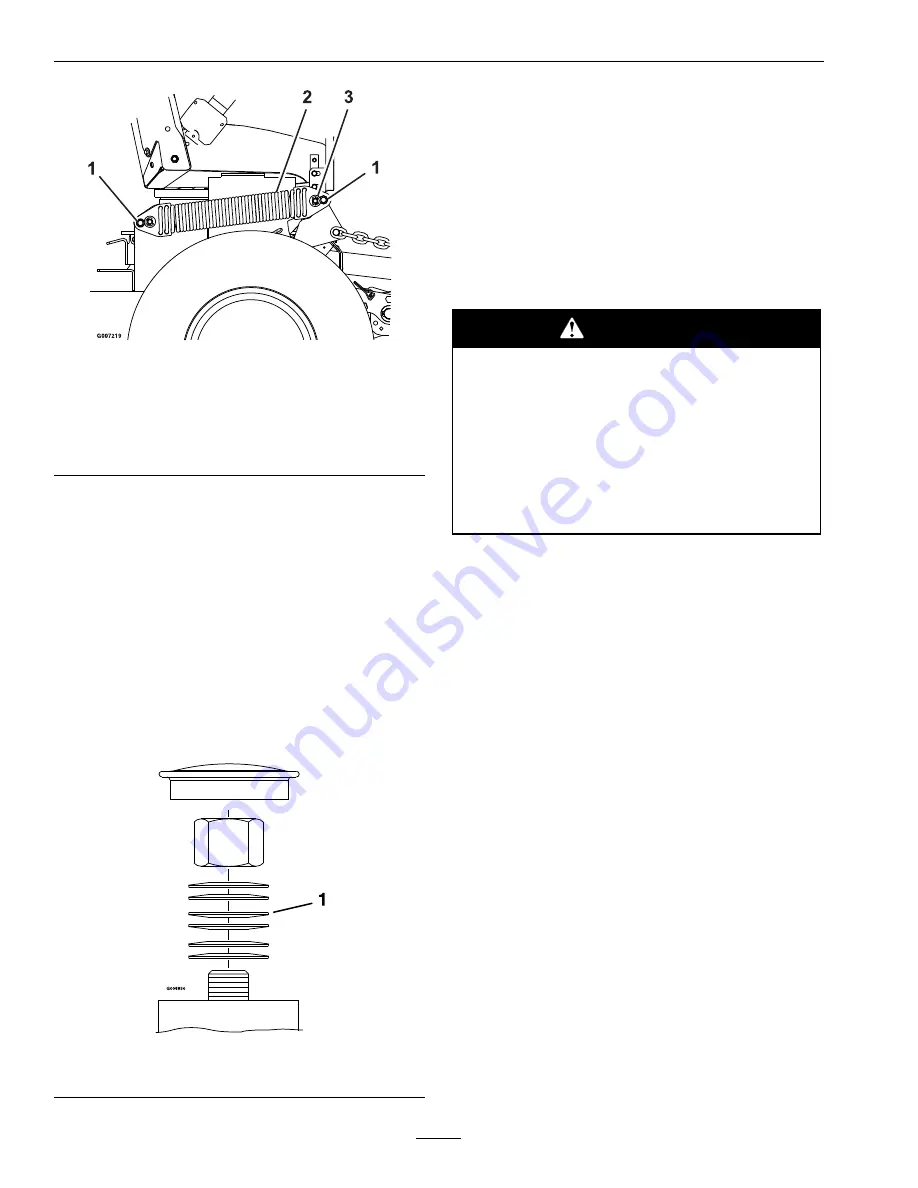
Maintenance
Figure 16
Right-Hand Side of Unit Shown
1.
Re-install spring in outer
holes to reduce spring
tension.
3.
Remove e-ring and
washer.
2.
Weight transfer spring.
7. Re-install the left fender
8. For additional weight transfer adjustment, repeat
steps 4 through 7 on the right side of the unit.
Caster Pivot Bearings
Pre-Load Adjustment
Remove dust cap from caster and tighten nyloc nut
until washers are flat and back off 1/4 of a turn
to properly set the pre-load on the bearings. If
disassembled, make sure the spring disc washers are
reinstalled as shown in Figure 17.
Figure 17
1.
Spring disc washers
Cleaning
Clean Engine Cooling
System
Service Interval: Before each use or daily
(May be required more
often in dry or dirty
conditions.)
CAUTION
Excessive debris around the engine cooling
air intake and inside of the pump drive
belt compartment and damaged or missing
rubber baffles can cause the engine and
hydraulic system to overheat which can
create a fire hazard.
Clean all debris from inside of pump drive
belt compartment daily.
1. Stop engine, wait for all moving parts to stop, and
remove key. Engage parking brake.
2. Clean all debris from rotating engine air intake
screen and from around engine shrouding.
3. Clean all debris from around the engine and drive
belts.
Remove Accumulated Debris
from Engine (Briggs &
Stratton Units Only)
Service Interval: Before each use or daily
Engine parts should be kept clean to reduce the risk
of overheating and ignition of accumulated debris.
1. Stop engine, wait for all moving parts to stop, and
remove key. Engage parking brake.
2. Remove front panel from engine and clean around
the intake manifold, fuel pump, and carburetor.
3. Reinstall the front panel.
Important:
Do Not use water to clean engine.
Use low pressure compressed air. See Engine
Owner’s Manual.
34