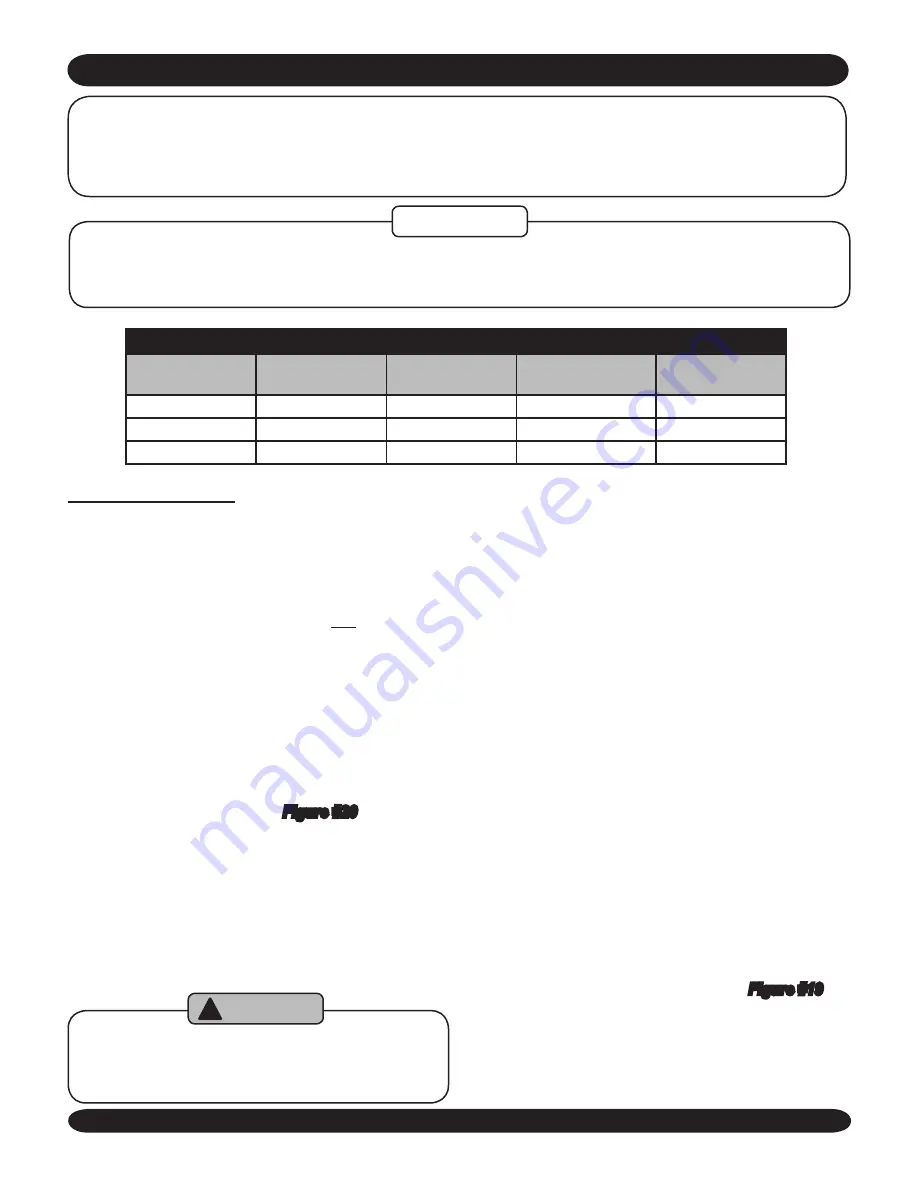
39
TABLe 8: ReCoMMended MiniMuM CHiMney siZes
FiRinG RATe
(gph)
CHiMney
HeiGHT
(ft)
noMinAL
CHiMney
rOunD
LinEr inSiDE
sQuARe
LinEr inSiDE
0.60 -1.30
15
8” x 8”
6”
6 ¾” x 6 ¾”
1.31 -1.80
15
8” x 8”
7”
6 ¾” x 6 ¾”
1.81 -2.00
20
8” x 8”
8”
6 ¾” x 6 ¾”
For elevations above 2,000 feet above sea level, add 3 feet to the chimney heights.
CHIMNEY AND CHIMNEY CONNECTIONS
For oil fired boilers with connections to vents or chimneys, vent installations shall be in accordance
with applicable provisions of nFPA31 insTALLATion oF oiL BuRninG eQuiPMenT, latest revision,
(u.s.) or CsA B139 (Canada) and applicable provisions of local building codes.
Fresh air (ventilation) is important to proper venting. Ventilation and venting are two parts of the same sys-
tem. Inadequate ventilation will result in inadequate venting. Always be sure to have enough ventilation to
ensure proper venting.
NOTICE
CHiMney VenTinG
Chimney venting is an important part of a safe and
1.
efficient oil fired appliance system. Requirements of
NFPA31 – Standard for the Installation of Oil-Burning
Equipment and NFPA 211 – Standard for Chimneys,
Fireplaces, Vents, and Solid Fuel-Burning Appliances
for installations in the United States and the require-
ments of CSA B139 – Installation Code for Oil-burn-
ing Equipment. (Installations in Canada) must be met.
Ensure that there is sufficient draft during the entire
2.
heating season to allow for the safe evacuation of flue
gasses.
The boiler can be vented into a fireclay
3.
tile-lined
masonry chimney constructed from type L vent or a
factory built chimney that complies with the type HT
requirements of UL103. See
Figure #20
for recom-
mended installation.
Chimney Inspection – Prior to the installation of any
4.
new or replacement fuel burning equipment the
chimney shall be inspected by a qualified installer.
The chimney shall be examined by a qualified person
in accordance with the requirements of NFPA 211,
Standard for Chimneys, Fireplaces, Vents, and Solid
Fuel Burning Appliances or CSA B139.
de-rating the appliance may cause conden
-
sation on the interior walls of the chimney
and the boiler.
WARNING
!
Loose Mortar – Loose mortar could be an indica-
A.
tion of prior history of condensing flue gases upon
the inside walls of the chimney. Colder climates are
more susceptible to this condition. Under no circum-
stances shall a chimney of this condition be used
until it meets the requirements of NFPA 211 or CSA
B139.
Unlined Chimney – Under no circumstances shall
B.
a chimney constructed of brick only be used. Only
approved clay liners or listed chimney lining systems
shall be used as specified in NFPA 31 or CSA B139
Abandoned Openings – Openings through the chim-
C.
ney wall that are no longer used shall be sealed in
accordance to NFPA 211. Often abandoned open-
ings are improperly sealed and usually covered by a
gypsum wall covering.
Clean Chimney – Chimney shall be free of all loose
D.
debris.
Install draft regulator at least 18” above breach. At
5.
least 18” of straight run up stream of regulator will
ensure proper operation.
Draft Regulator – the draft regulator supplied with the
6.
boiler must be used with this appliance. No other
draft regulator shall be used. Refer to
Figure #19
.