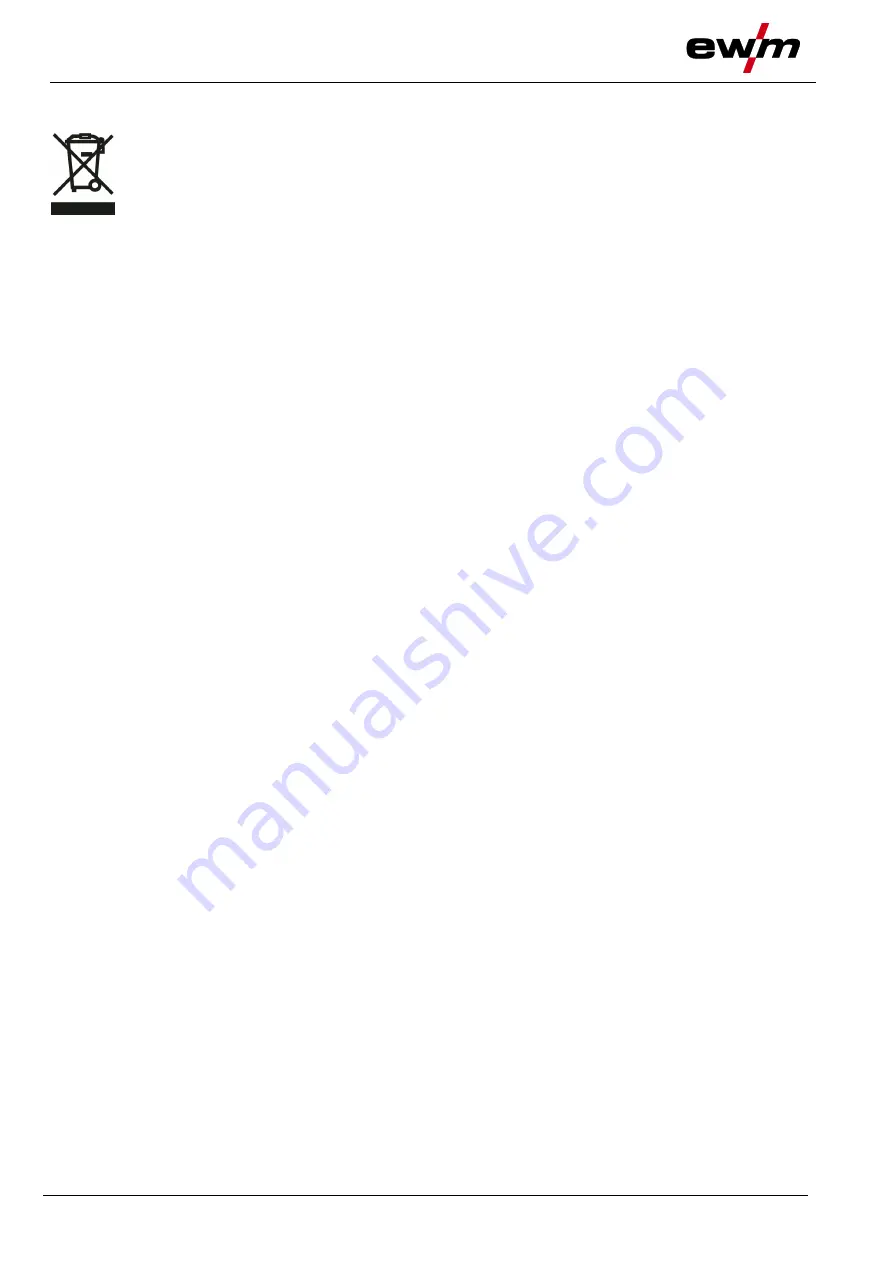
Maintenance, care and disposal
Disposing of equipment
32
099-000235-EW501
17.12.2020
6.3 Disposing of equipment
Proper disposal!
The machine contains valuable raw materials, which should be recycled, and electronic com-
ponents, which must be disposed of.
• Do not dispose of in household waste!
• Observe the local regulations regarding disposal!
• According to European provisions (Directive 2012/19/EU on Waste of Electrical and Electronic
Equipment), used electric and electronic equipment may no longer be placed in unsorted municipal
waste. It must be collected separately. The symbol depicting a waste container on wheels indicates
that the equipment must be collected separately.
This machine has to be disposed of, or recycled, in accordance with the waste separation systems in
use.
• According to German law (law governing the distribution, taking back and environmentally correct dis-
posal of electric and electronic equipment (ElektroG)), used machines are to be placed in a collection
system separate from unsorted municipal waste. The public waste management utilities (communities)
have created collection points at which used equipment from private households can be disposed of
free of charge.
• Information about returning used equipment or about collections can be obtained from the respective
municipal administration office.
• In addition to this, returns are also possible throughout Europe via EWM sales partners.