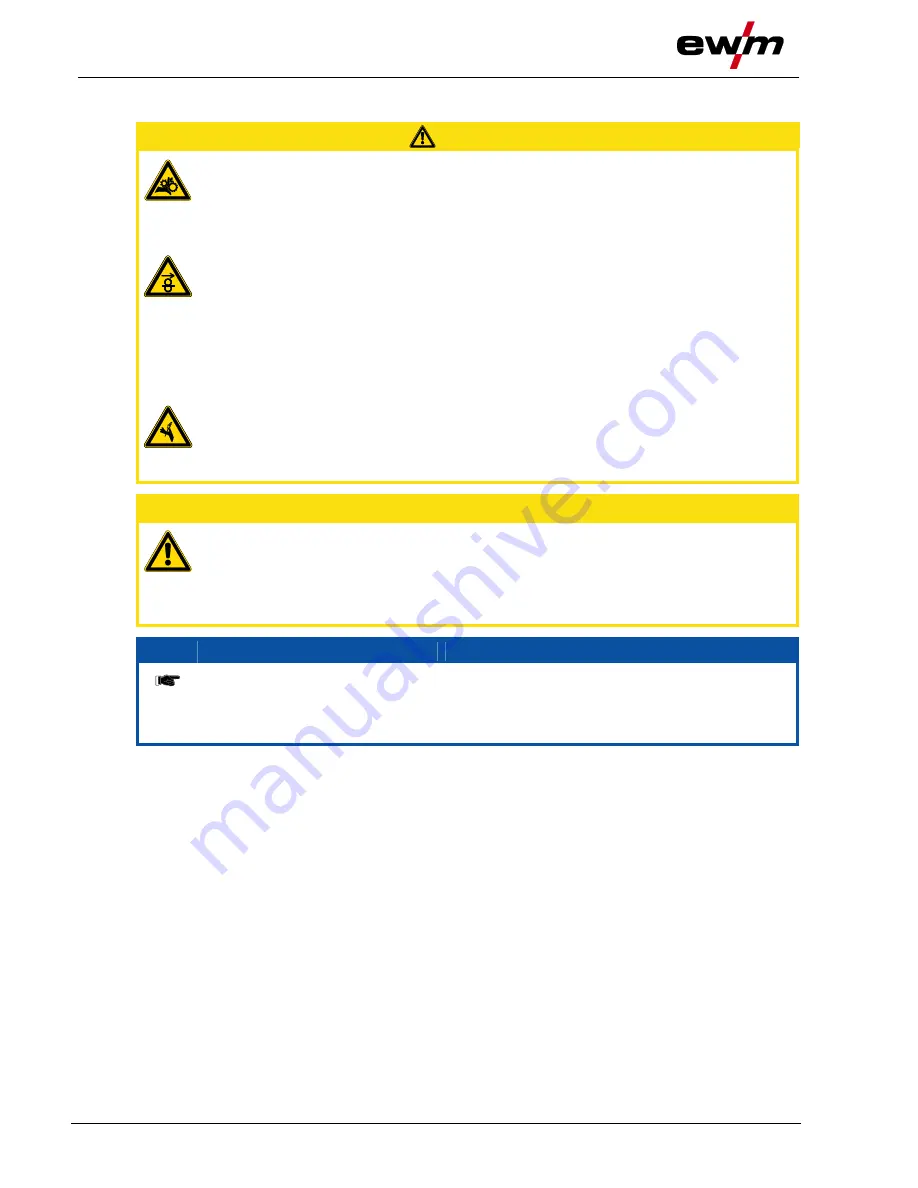
Design and function
MIG/MAG welding
40
099-005230-EW501
02.04.2014
5.8.2.4
Inching the wire electrode
CAUTION
Risk of injury due to moving parts!
The wire feeders are equipped with moving parts, which can trap hands, hair, clothing
or tools and thus injure persons!
• Do not reach into rotating or moving parts or drive components!
• Keep casing covers or protective caps closed during operation!
Risk of injury due to welding wire escaping in an unpredictable manner!
Welding wire can be conveyed at very high speeds and, if conveyed incorrectly, may
escape in an uncontrolled manner and injure persons!
• Before mains connection, set up the complete wire guide system from the wire spool to the
welding torch!
• Remove the pressure rollers from the wire feeder if no welding torch is fitted!
• Check wire guide at regular intervals!
• Keep all casing covers or protective caps closed during operation!
Risk of injury due to welding wire escaping from the welding torch!
The welding wire can escape from the welding torch at high speed and cause bodily
injury including injuries to the face and eyes!
• Never direct the welding torch towards your own body or towards other persons!
CAUTION
Extensive wear due to incorrect contact pressure!
Incorrect contact pressure will cause extensive wear of the wire feed rollers!
• With the adjusting nuts of the pressure units set the contact pressure so that the wire
electrode is conveyed but will still slip through if the wire spool jams.
• Set the contact pressure of the front rollers (in wire feed direction) to a higher value!
NOTE
The inching speed is infinitely adjustable by simultaneously pressing the wire inching
push-button and turning the wire speed rotary knob. The left display shows the wire
feed speed selected, the right display shows the current motor current of the wire feed
mechanism.