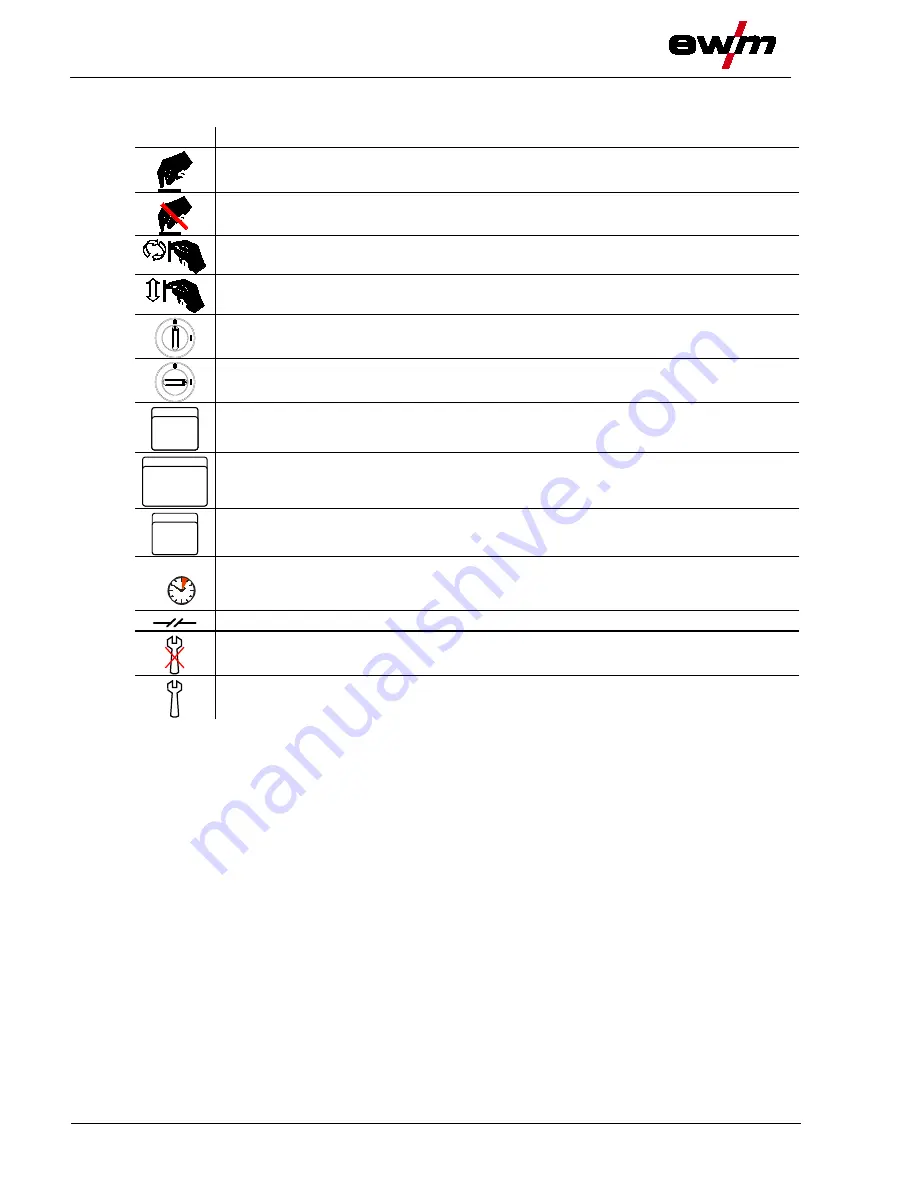
Safety instructions
Explanation of icons
6
099-005219-EW501
10.06.2013
2.2
Explanation of icons
Symbol
Description
Press
Do not press
Turn
Switch
Switch off machine
Switch on machine
ENTER
ENTER
ENTER (enter the menu)
NAVIGATION
NAVIGATION (Navigating in the menu)
EXIT
EXIT (Exit the menu)
4 s
Time display (example: wait 4s/press)
Interruption in the menu display (other setting options possible)
Tool not required/do not use
Tool required/use