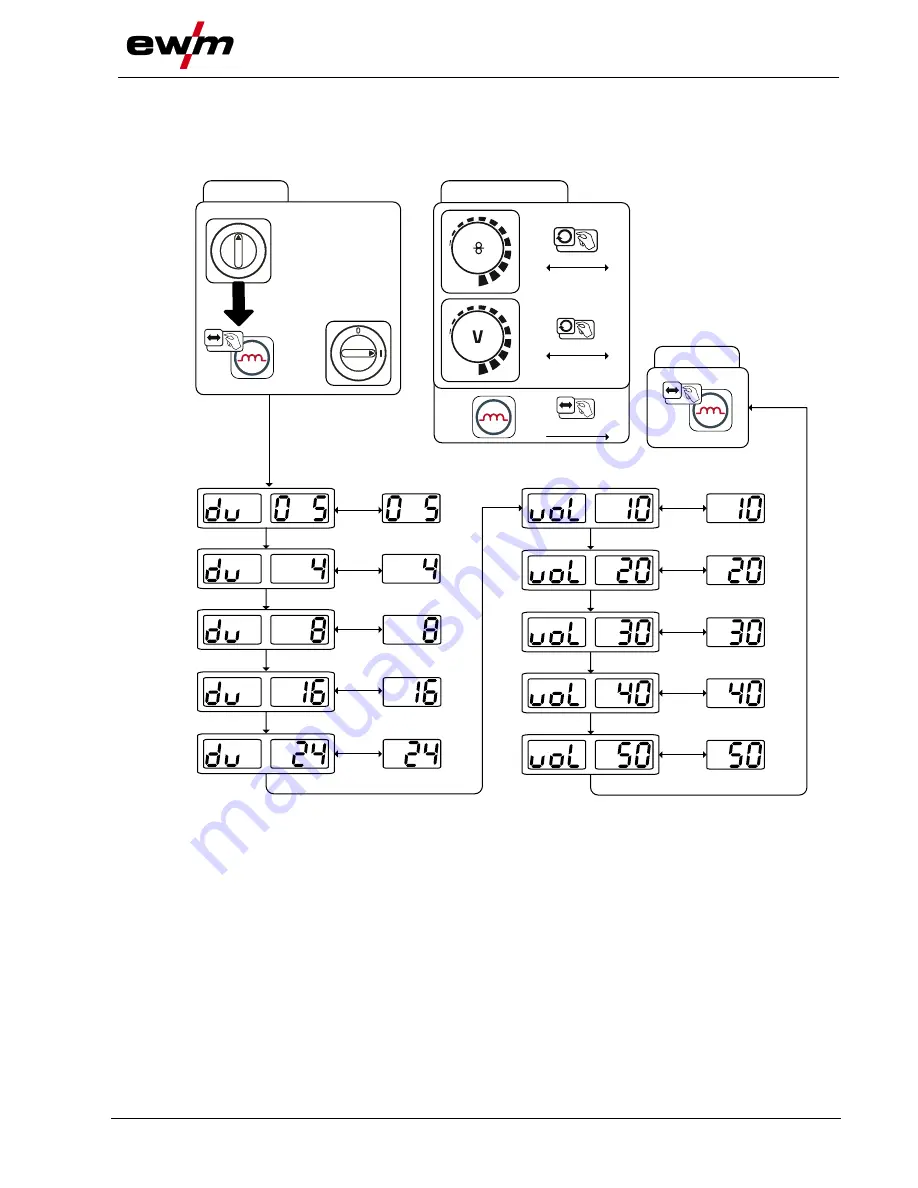
Rectifying faults
Welding parameter calibration
099-005425-EW501
14.07.2016
63
7.3
Welding parameter calibration
When differentiating between the welding parameters set on the wire feed unit/remote control and those
shown on the welding machine, they can be calibrated easily with this function.
NAVIGATION
C
B
A
C
C
B
C
B
C
B
C
B
B
A
A
C
C
C
C
A
A
A
EXIT
ENTER
+
l
0
Figure 7-1