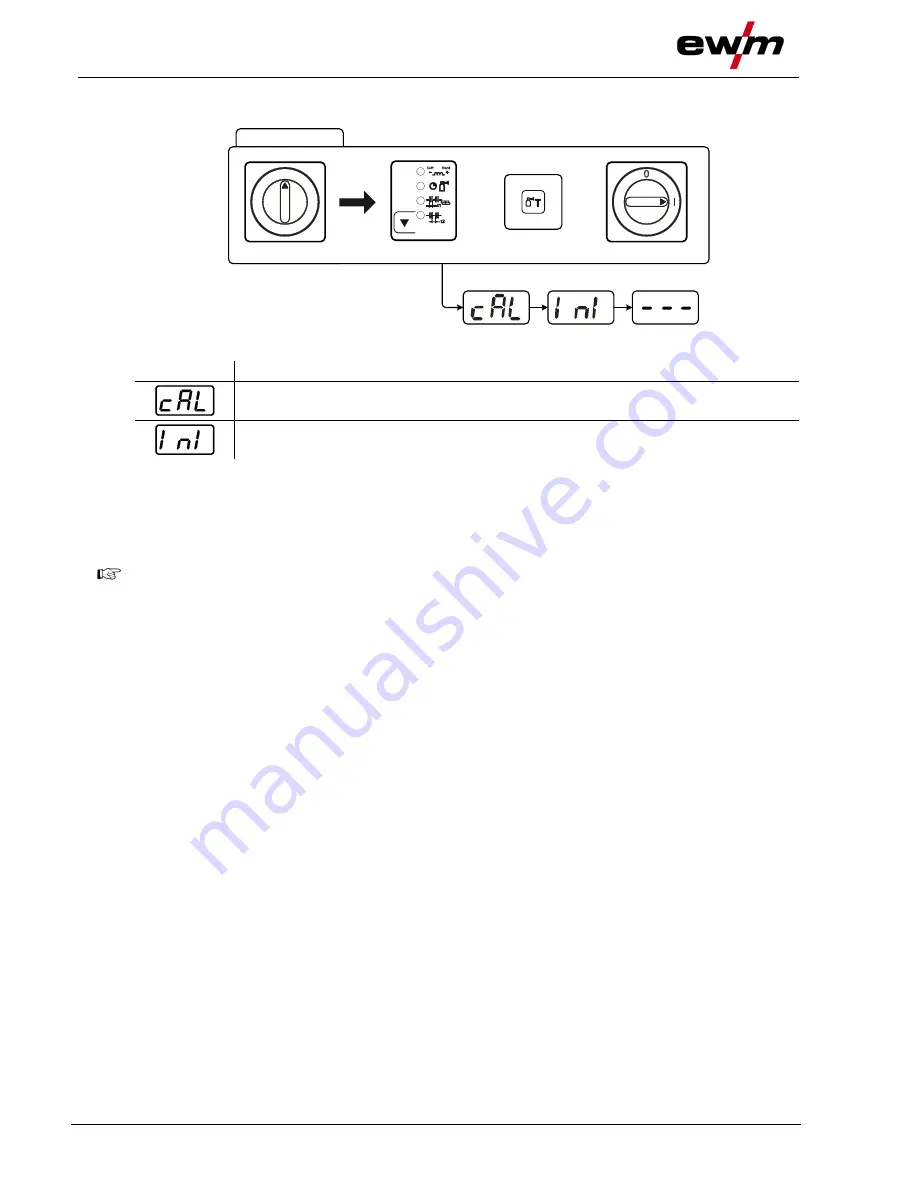
Rectifying faults
Resetting welding parameters to the factory settings
56
099-005548-EW501
27.10.2017
7.3
Resetting welding parameters to the factory settings
RESET
+
+
l
0
Figure 7-1
Display
Setting/selection
Calibration
The machine will be calibrated for approx 2 seconds each time it is switched on.
Initialising
Keep the push-button pressed until "InI" is shown on the display.
7.4
Display machine control software version
The query of the software versions only serves to inform the authorised service staff. It is available in the
machine configuration menu
> see 5.6 chapter
.
7.5
Dynamic power adjustment
This requires use of the appropriate mains fuse.
Observe mains fuse specification > see 8 chapter!
The dynamic power adjustment automatically adjusts the welding performance to an uncritical level for
the fuse.
The dynamic power adjustment can be set in two increments in the machine configuration menu using
parameter "FUS": 20 A, 16 A
> see 5.6 chapter
.
The currently selected value will be shown on the "cal" section of the display for three seconds after the
machine has been switched on.