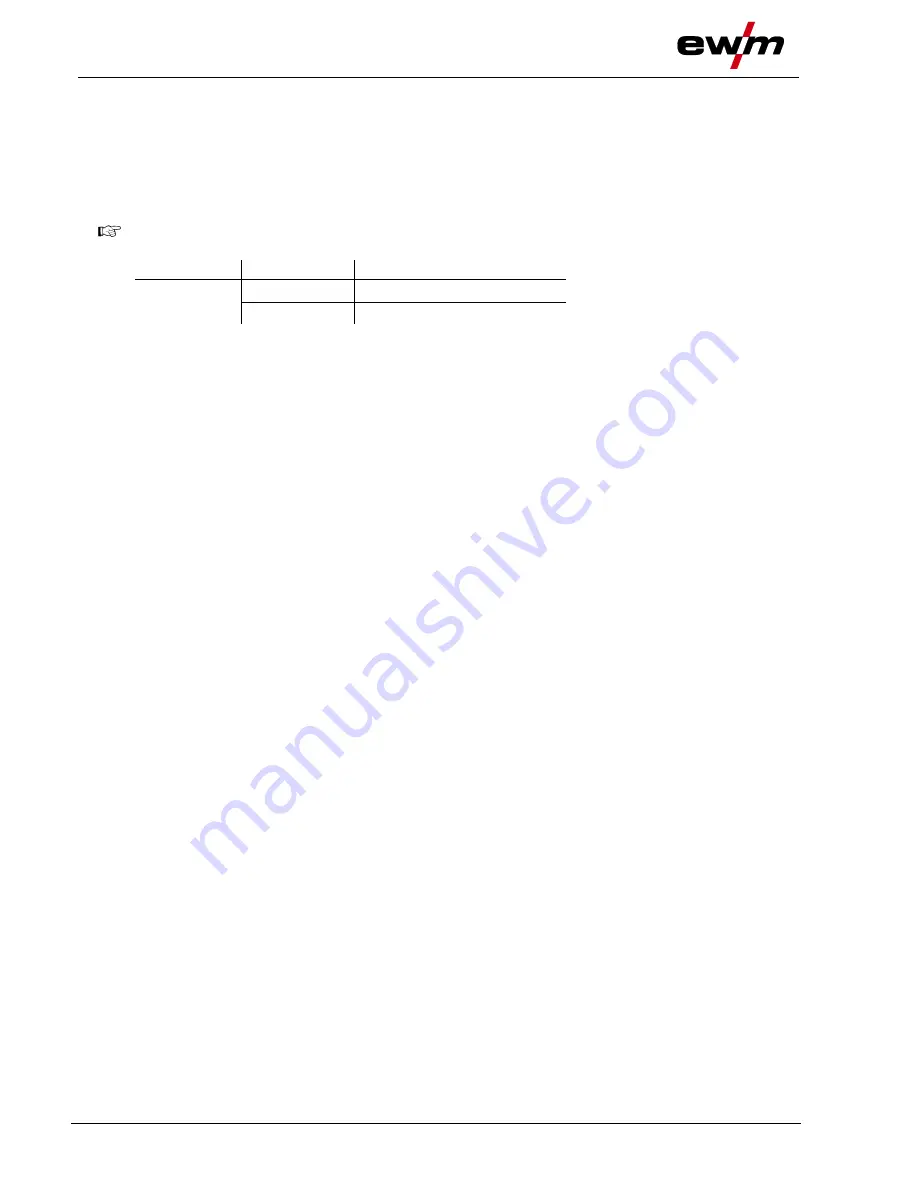
Rectifying faults
Checklist for rectifying faults
54
099-002060-EW501
19.10.2015
7
Rectifying faults
All products are subject to rigorous production checks and final checks. If, despite this, something fails to
work at any time, please check the product using the following flowchart. If none of the fault rectification
procedures described leads to the correct functioning of the product, please inform your authorised
dealer.
7.1
Checklist for rectifying faults
The correct machine equipment for the material and process gas in use is a fundamental
requirement for perfect operation!
Legend
Symbol
Description
Fault/Cause
Remedy
Excess temperature signal light illuminates
Excess temperature, welding machine
Allow the machine to cool down whilst still switched on
Functional errors
Machine control without displaying the signal lights after switching on
Phase failure > check mains connection (fuses)
Connection problems
Make control lead connections and check that they are fitted correctly.
Loose welding current connections
Tighten power connections on the torch and/or on the workpiece
Tighten contact tip correctly