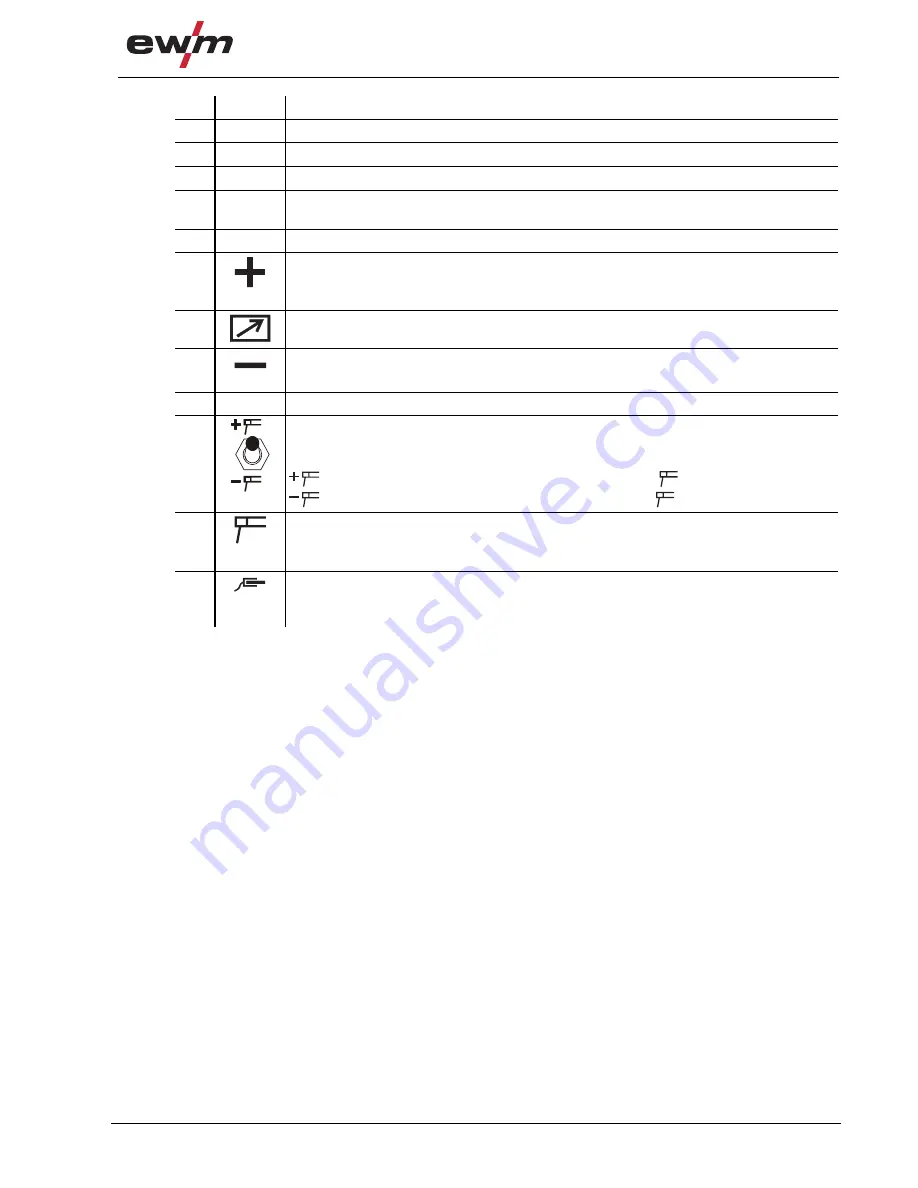
Machine description – quick overview
Pico 300 cel
099-002032-EW501
29.04.2010
15
Item Symbol Description
0
1
Carrying strap
2
Transport bar
3
Carrying handle
4
Machine control
See Machine control – operating elements chapter
5
Cooling air inlet
6
Connection socket, "+" welding current
• TIG: Connection for workpiece lead
• MMA: Electrode holder or workpiece lead connection
7
Connection socket, 19-pole
Remote control connection
8
Connection socket, “-” welding current
Electrode holder or workpiece lead connection
9
Machine feet
10
Pole reversal changeover switch
The changeover switch is used to switch over the welding current polarity (“+” or “-” ) of
the electrode holder and workpiece lead connection sockets.
=
Welding current polarity “+” on connection socket
.
=
Welding current polarity “-” on connection socket
.
11
Connection socket, electrode holder
The welding current polarity (“+” or “-”) are based on the setting of the “Welding current
polarity changeover switch”.
12
Connection socket, workpiece lead
The welding current polarity (“+” or “-”) are based on the setting of the “Welding current
polarity changeover switch".