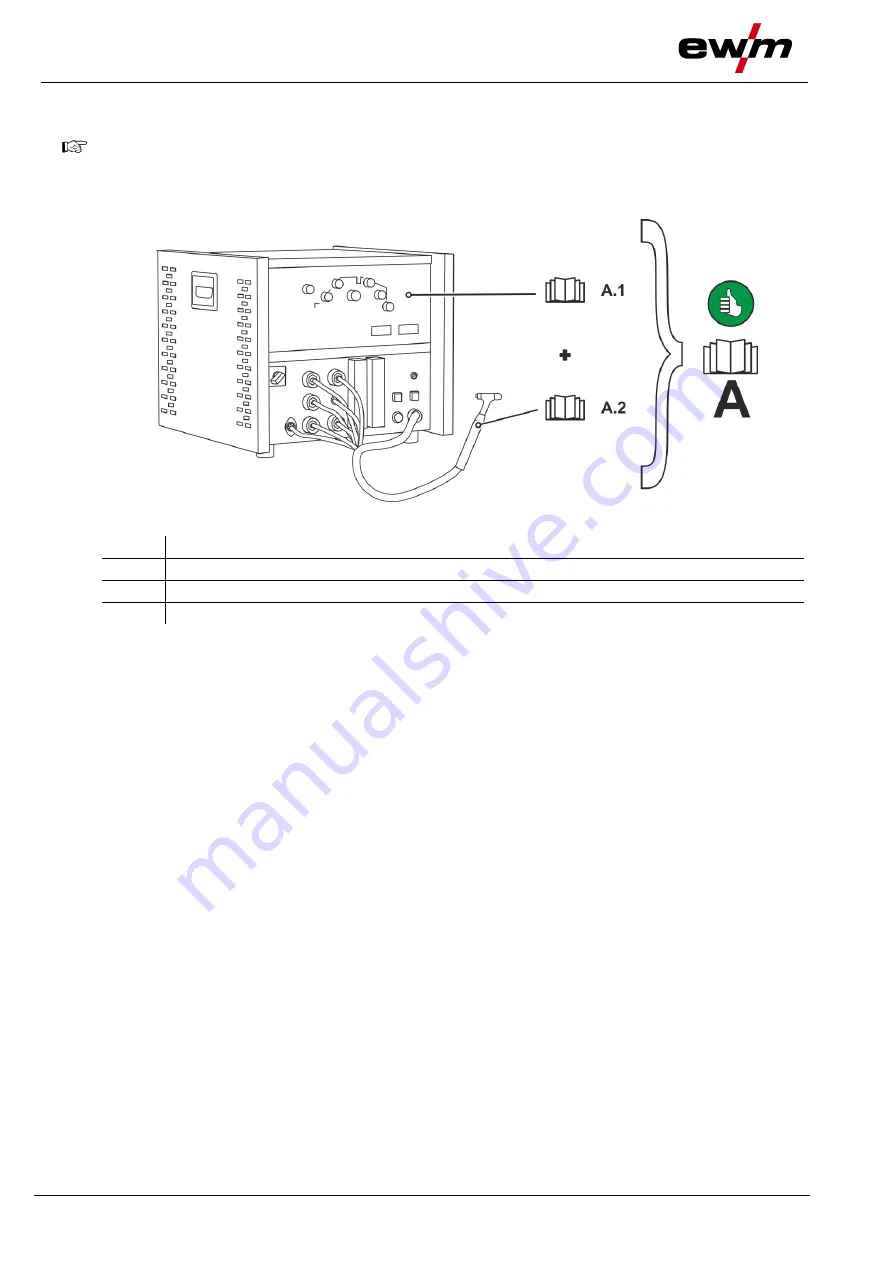
For your safety
Part of the complete documentation
6
099-002025-EW501
29.11.2017
2.3
Part of the complete documentation
These operating instructions are part of the complete documentation and valid only in
combination with all other parts of these instructions! Read and observe the operating
instructions for all system components, especially the safety instructions!
The illustration shows a general example of a welding system.
Figure 2-1
Item
Documentation
A.1
Power source
A.2
Welding torch
A
Complete documentation