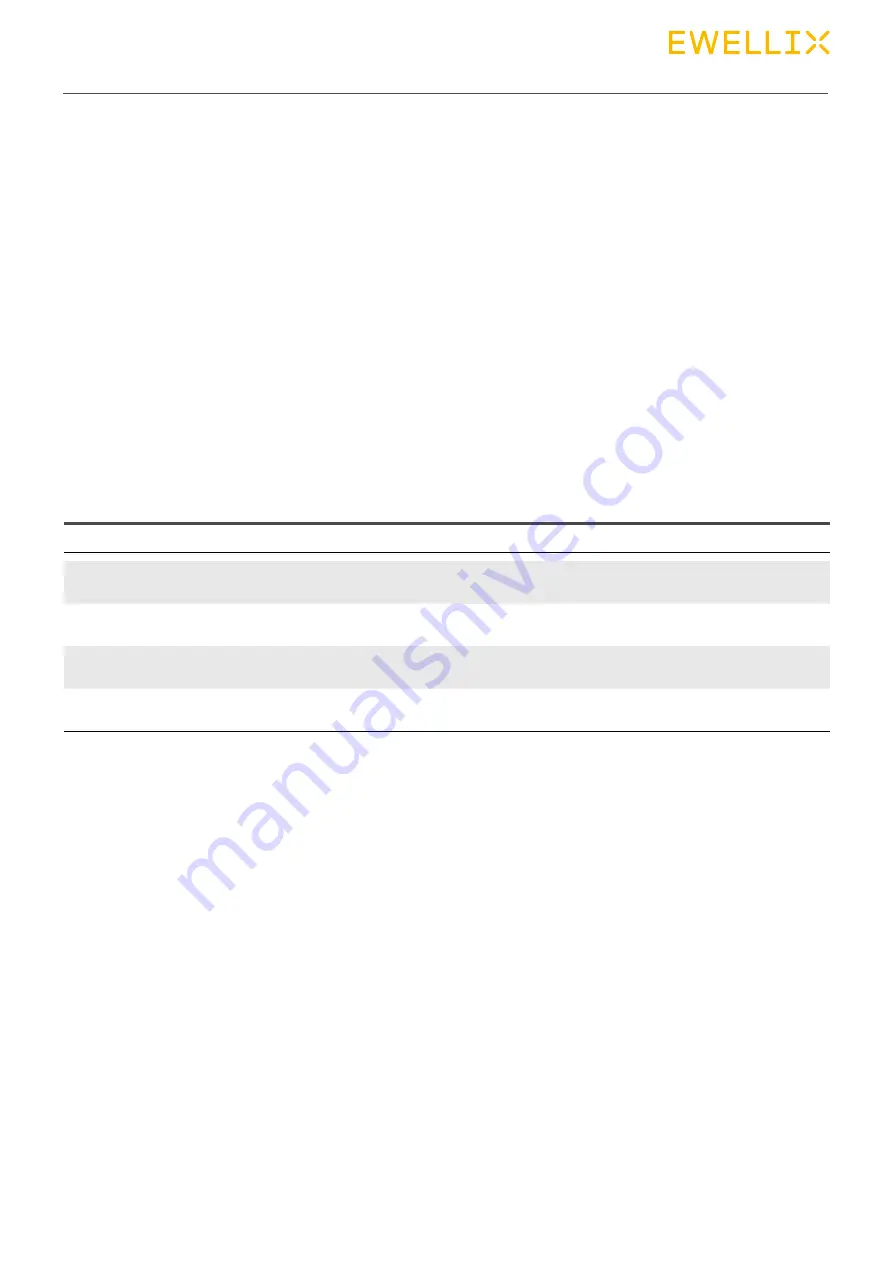
7
2 .0 S afety
7
2.5 Potential risks
The following risks during LIFTKIT operation have to be con-
sidered in an application specific risk assessment
• The pillar does not detect an impact automatically and
does not stop movement upon impact. This can lead to:
-
Crushing of a person or an object in the path of the pillar,
causing serious injury or death or property damage.
-
Dynamic impact to a person or an object causing serious
injury or death or property damage.
• It is possible that the pillar movement does not stop at the
desired position and the UR control software does not rec-
ognize this
-
Movement of the robot can occur at a different position
than intended, causing significant serious injury or death
or property damage.
2.6 Stopping behavior
LIFTKIT stops differently depending on the stop mechanism
triggered. The following four stopping behaviors can occur:
Stopping mechanism
Stop distance
Stop time
Power line to SCU controller is cut by safety relay (Category 0,
LIFTKIT de-energized, uncontrolled stop)
28 mm
750 ms
Emergency stop button pressed on the Universal Robots system
(Category 1, LIFTKIT energized, uncontrolled stop)
18 mm
200 ms
Software triggered stop if the robot stops due to an impact or the
serial connection is damaged
tbc
tbc
Software triggered stop in normal operation. LIFTKIT energized,
controlled stop using speed ramp down
50 mm
800 ms
Test report LTV180157