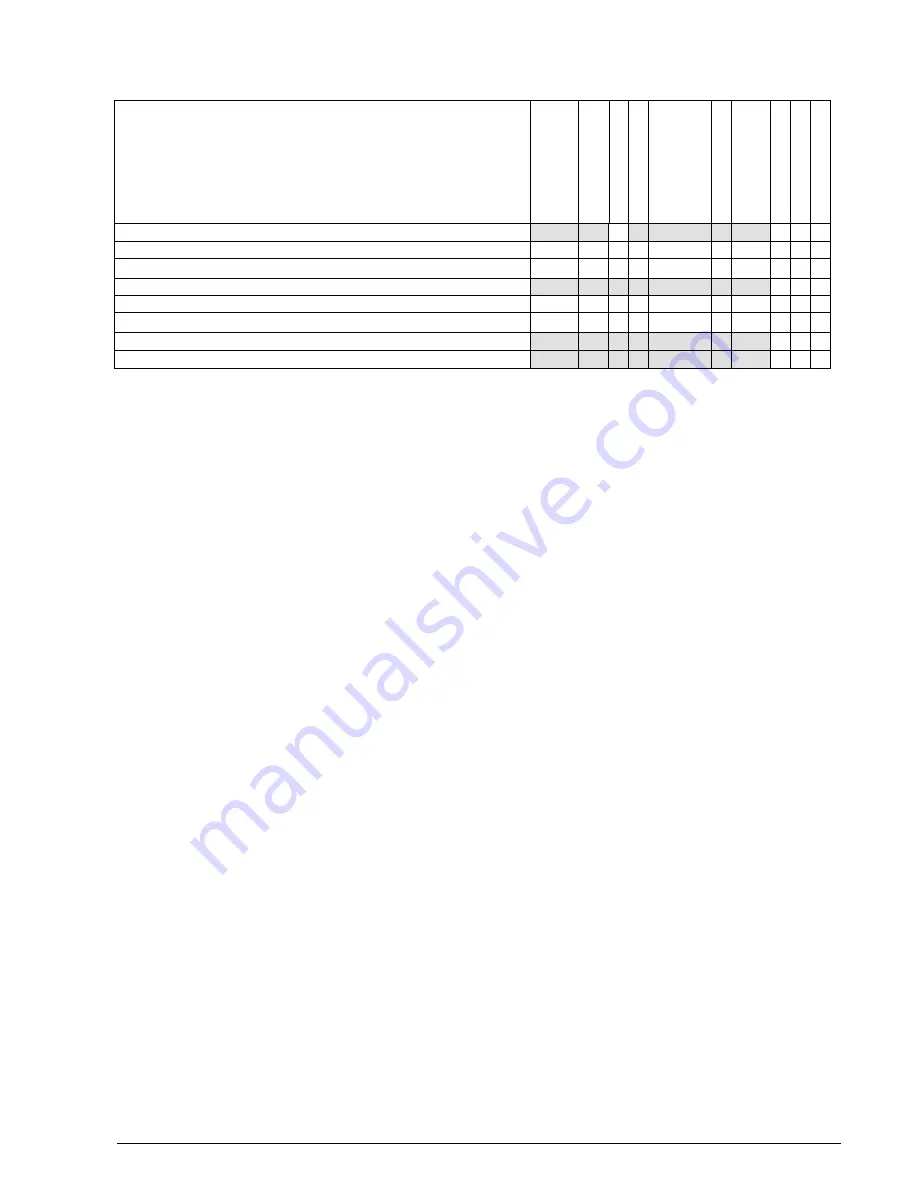
Operating instructions EcoStar 530 F-M
Datei:1_EcoStar530F-M_9662597_Betriebsanleitung_EN_2009-05.doc
Update: 2012-12-18, S. 34 , 40
9662597
41/42
W e reserv e the right to change ex ecution and construction!
MEIKO Maschinenbau GmbH & Co. KG, Englerstr. 3, D-77652 Offenburg, Tel.: +49/781/203-0, Fax: +49/781/203-1121
Maintenance procedures
FV
2
8
G
/
FV
2
8
GI
O
E
c
o
S
ta
r
4
3
0
F
E
c
o
S
ta
r
5
3
0
F
-M
FV
4
0
.2
/
FV
6
0
.2
/
FV
7
0
.2
D
GK
6
0
OR
5
0
H
E
co
S
ta
r 5
4
5
D
-M
/
DV
8
0
.2
/
DV
1
2
0
.2
/
DV
1
2
5
.2
/
DV
2
0
0
.2
/
DV
2
0
0
.2
P
W
D
V
2
7
0
B
FV
1
3
0
.2
–
FV
2
5
0
.2
/
D
V
2
7
0
.2
C
o
mpo
n
e
n
t
OK
C
o
mpo
n
e
n
t
fa
u
lt
y
C
o
mpo
n
e
n
t
re
p
lac
e
d
Check dosage, adjust if necessary
10. Operation check of the complete machine
Check machine for correct interaction of all functions
11. Test run
Check results of test wash and rinse
Brief instruction for new personnel
20 Environmentally acceptable measures, Disposal of the
installation
Each discarded appliance is to be made immediately unserviceable - to avoid later acci-
dents.
Switch the machine off completely via the on-site power disconnection device.
When you eventually dispose of the installation (dismantlement/scrapping), the parts and
their corresponding materials should preferably be re-used.
Here is a list of the materials that most frequently occur when dismantling:
Chrome-nickel-steel
Aluminium
Copper
Brass
Electrical and electronic parts
PP and other synthetic materials
21 Documentation
Installation drawing / technical sheet
Technical data sheet
Wiring diagram / Programming instructions