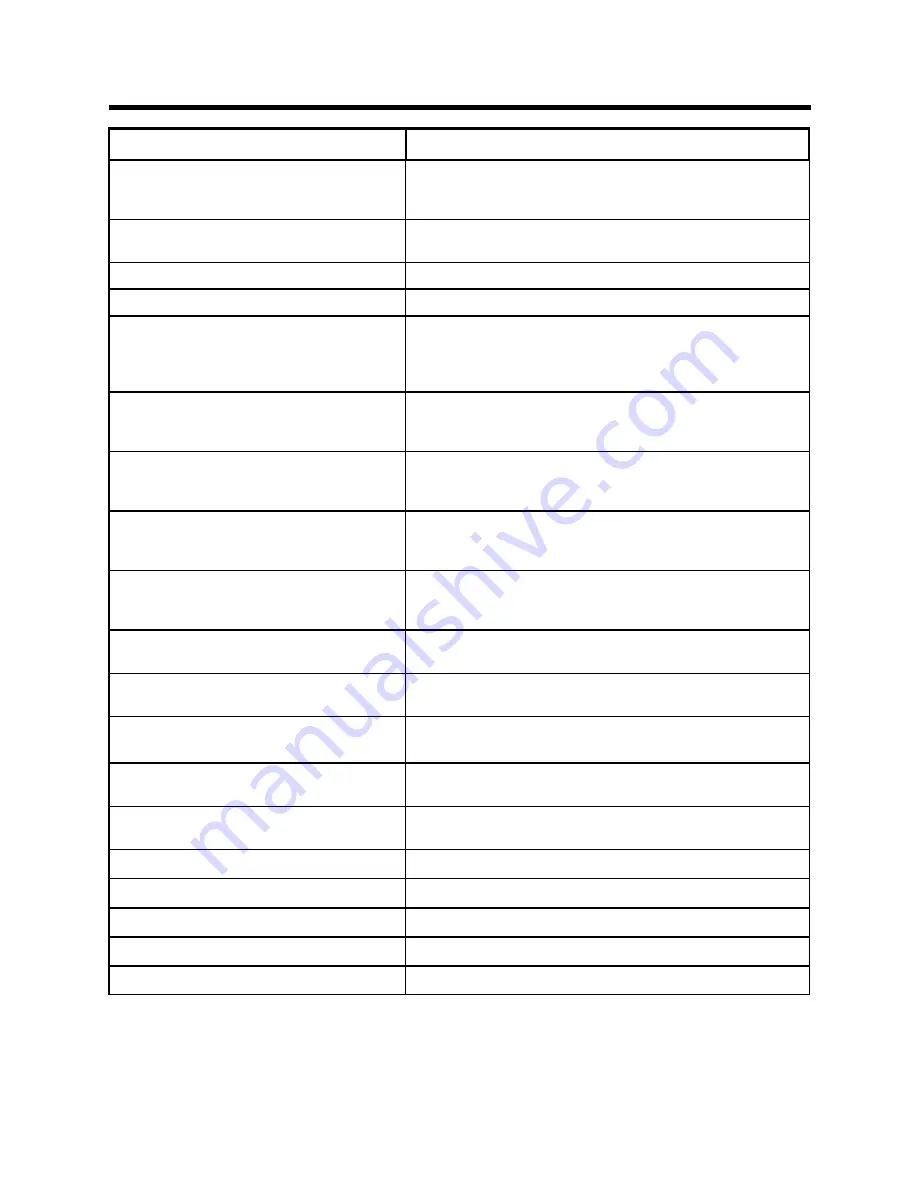
40
Section 6
Trouble Shooting
PLASMA TROUBLE SHOOTING:
CAUSE/SOLUTION
Air Flows but arc does not start within 2-3 seconds. Check consumables for wear and tightness. Check fuse.
Check Air Pressure. Sticky or slow spring/piston on torch blow back
mechanism. Release trigger and try again. Preflow turned on.
Air Flows but arc does not start or spark when noz-
zle is rubbed on the metal.
Pre Flow is turned on. Fuse blown. Missing swirl ring. Worn or loose
consumables. IGBT issue. PCB issue.
OK to cut light is not on. Will not start arc.
Increase air Pressure. Make sure air is connected.
Pilot arc will not light.
Fuse blown. Check fuse. Make sure consumables are correct.
Pilot arc will not transfer and amps read approxi-
mately 25-27 amps while switch is held. (Arc barely
cuts or only
“
scratches
”
the surface of the metal or
cut is extremely slow on thin materials.)
Check work clamp connection. Make sure rust is removed from work
clamp contact area. Faulty Clamp. Arc continuity is not being sensed.
If these steps do not correct the issue, contact Everlast.
Arc Sputters.
Inadequate air flow or air pressure. Improperly sized nozzle. Decrease
size as amps are lowered. Increase air pressure to 70- psi while air is
flowing through torch. Loose consumables. Check tightness.
Consumables are dirty, smutty looking upon inspec-
tion. Premature wear on consumables. Shortened
consumable life.
Moisture, oil contamination of consumable. Wrong consumables. Poor
quality aftermarket consumables.
Premature wear on consumables. Short consuma-
ble life. Uneven wear of consumables, melting of
cup.
Moisture, oil contamination of consumable. Excessive pilot arc time.
Improper cutting technique. Wrong piercing technique. Wrong/
mismatched consumables.
Arc will not start. Air will not flow. Machine runs.
Torch cup is loose, safety contact pins dirty or not making contact with
cup face. Torch switch wire is loose. Problem with connector. Torch is
not properly connected.
Arc will not start. Air flows. Machine runs.
Swirl Ring damaged or missing. Wrong Polarity. Wrong process select-
ed.
Unstable Arc at lower amps.
Consumable orifice size is too large. Reduce orifice size. Wrong air
pressure. Poor work clamp connection. Check clamp and connectors.
Arc tries to start but irregular, dancing arc and/or
arc melts through side of nozzle.
Missing swirl ring, or worn electrode or both. Check and replace. Make
sure swirl ring is not cracked.
Arc will try to start if touched to the metal, but no
air flow while switch is pressed.
Stuck or dirty solenoid valve. Contact Everlast. Wrong Process select-
ed.
Air flows continuously.
Post flow turned set too long. Preflow is turned on. Solenoid is stuck.
Contact Everlast.
Excessively Beveled Cut.
Worn consumables, too high of stand-off height.
Cup and/or nozzle is melting or cracking.
Improper cutting technique/excessive piercing.
Power input circuit breaker trips repeatedly.
Improperly sized circuit. Internal issue. Contact Everlast.
Arc
“
Blows Out
”
when ready to cut.
Too high of air pressure. Reduce to 72 psi. Use smaller nozzle
Arc will not stop when switch is released.
Unit is in 4T. Switch to 2T. Torch trigger is stuck.