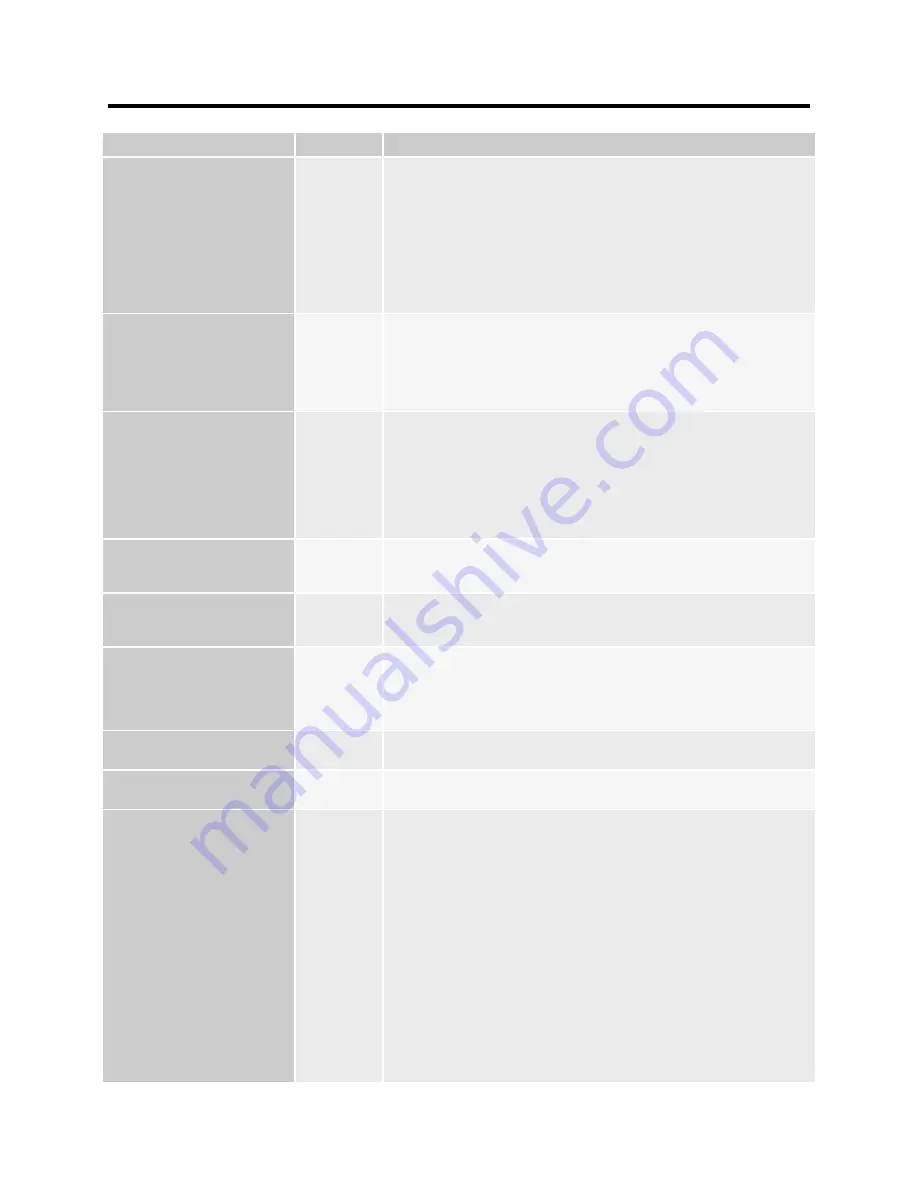
20
POWERPRO 256Si FEATURES
PARAMETERS
PURPOSE
8. Pulse Frequency Control
.5-250 Hz
Represented as Hertz (Hz), the Pulse Frequency adjusts the number of times per sec-
ond the pulse makes one complete cycle between the welding amp value (Peak) and
the pulse amp value (Background current or base amps). This is also commonly re-
ferred to as Pulses Per Second (PPS). Low pulse frequencies can be used to time the
addition of the filler metal and improve weld appearance. High pulse frequencies are
useful for preventing excessive puddle wicking on edges and thin seams. Also, it is
useful for overall heat control while welding thicker gauges of metal, which can be
used to help control warping. Higher pulse frequencies are often used in automated
TIG welding processes. Caution: Welding at high pulse frequencies increases the deci-
bel level of the arc. Wear hearing protection while welding at high pulse frequencies.
9. Pulse Amps (Ratio) Control
5-95%
Sets the value of the Pulse Amps (also referred to as the base or background current)
during the pulse cycle. This is expressed as a percent of Welding Amps. For example,
a welding amp value of 125 amps with a pulse amps setting of 50% will result in a
pulse amp value of 75 amps. The Pulse Amp setting chosen represents the lowest amp
value achieved during the pulse cycle. When the pulse mode is selected, the position
of the main amp knob determines the Welding Amp (Peak) value.
10. Pulse Time On (Balance) Control
10-90%
Sets the duty cycle (balance) of the pulse. This is accomplished by dividing or skewing
the amount of time the pulse spends at the maximum amp value of the pulse against
the Pulse Amp (background current) stage which is the lowest part of the pulse. The
pulse consists of two stages: Welding Amps (Peak) and Pulse amps (Base/Background
current). This is represented by a % of total time during one full pulse cycle that the
pulse spends in the upper (peak) stage. Practically speaking, the Pulse Time on control
can be used to increase or decrease welding amp (Peak) time relative to the pulse
amp time of the cycle to help manage heat input.
11. Positive Connector
35-70 mm²
Location of the Positive terminal connection. DINSE-style connector. (35 Series)
Stick: Electrode holder connection. TIG: Work clamp connection. Plasma: Work
clamp connection.
12. Quick Connect Gas Outlet
9 mm
Connects the gas supply to the TIG and air supply to the Plasma torch. To connect:
Push the torch fitting into the connector until the collar slides forward with a click. To
Release: Slide the collar back.
13. Control and Pilot Arc Connector
7 Pin
Connect the foot pedal or torch switch to the pinned socket to control the welder.
Only the foot pedal or torch control connector can be plugged in at one time. If the
torch has a torch switch feature, tie the loose connector back or leave it hanging while
using the pedal. Loosen the black thumb screw to connect the pilot arc wire to the
plasma cutting torch. The thumbscrew is only used with the plasma torch.
14. Negative Connector
35-70 mm²
Location of the Negative terminal connection. Dinse-style. (35 series)
Stick: Work clamp connection. TIG: Torch connection. Plasma: Torch connection.
15. AC/DC Selector
AC/DC process Select DC output for Steel, Stainless and most metals.
Select AC output for Aluminum and Magnesium alloys.
16. AC Balance Control
10-90% of EP
Selects the percentage of Electrode Positive (EP) used during the AC welding mode to
provide the needed cleaning. Represented as a percent of EP, it actually divides the
relative amount of time that the AC cycle spends in Electrode Positive and Electrode
Negative polarity during one full AC cycle. In short, it controls the balance between
cleaning and penetration to achieve the best balance or desired effect while welding
in the AC mode. When the control knob is rotated left, more Electrode Negative is
present and more penetration will be achieved. When the control knob is rotated
clockwise, more Electrode Positive is present and more cleaning (cathodic etching)
action will be achieved. Too much cleaning action will result in the balling of the tung-
sten tip, nodules or splitting, requiring the use of a larger tungsten necessary for the
same amperage range to prevent tungsten issues. Too little cleaning action will result
in a dull, dirty or sooty looking weld. Remember: This is expressed as a percent of full
Electrode Positive. This unit uses 100% Electrode Positive as the point of reference,
which may be contrary to what the user may find in some other brands. Using the
welder in excess of 50% EP can quickly vaporize the tungsten and reduce welding
capability when all other variables are the same. For most welds, no more than 45%
cleaning is needed. Ideally, start with 30% EP as a reference point, then adjust it up
or down to achieve best results.
Section 2
FRONT PANEL FEATURES AND CONTROLS CONTINUED
QUICK SETUP AND USE GUIDE