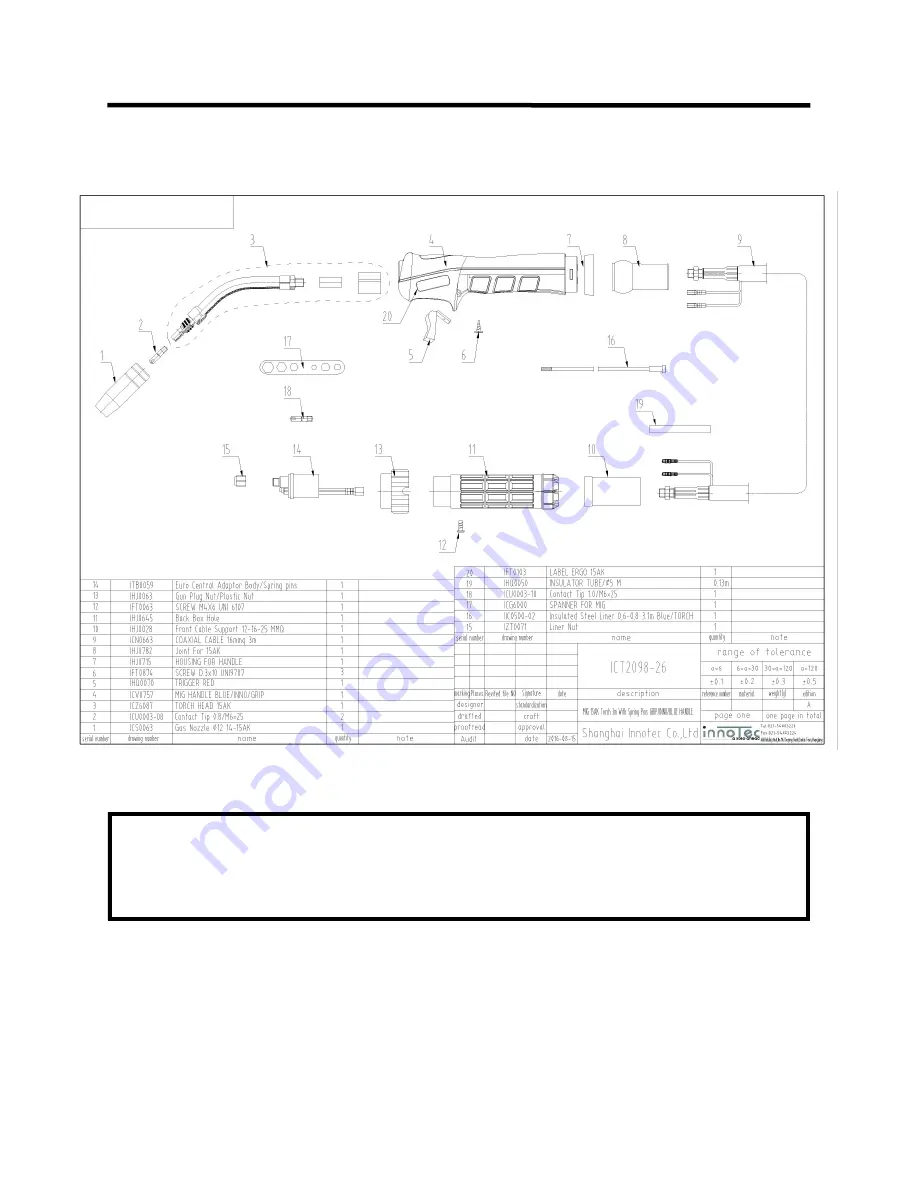
54
15 SERIES MIG TORCH
Expanded View
NOTE
: Some components may appear slightly different as design/supplier changes are made from time to time. At
time of publication, the standard MIG gun provided with Power MTS is commonly known as the 15 Series. The Innotec® listed
above is currently the default supplier of the 15 series. Everlast is not the torch manufacturer, but equips the PowerMTS units
with some of the most proven torches in history. Numerous manufacturers all over the world use interchangeable variations of
these torches including Binzel and Trafimet. Most consumables and parts are interchangeable with other manufacturer
’
s guns
designated as a
“15”.
The widely used Euro
-
connecter on the MIG torch also ensures that the customer can fit and install almost
any other type MIG torch if they desire, since most manufacturers offer torches with a Euro connector as an option.
Basic Theory and Function
Section 3